When thinking of a food manufacturing facility, many people may envision a lockdown area in which all personnel must wear full-body decontamination suits and where every internal surface of the facility must glow from the sheen of stainless steel. While this may be somewhat common for parts of a plant, a range of environments allow for different grades of motors, from general purpose to washdown, which drive many pumping applications. Market research continues to indicate that manufacturing facilities that automate the processes of food production from farm to fork are being built virtually everywhere. The heart and soul of the industrial machine that processes all these raw materials into consumable products is industrial electric motors. Clean, sanitary and environmentally friendly are some key buzzwords commonly used in the food processing industry. From the perspective of the equipment producers, those words mean caustics and chemicals, heat and high pressure. A large segment of this industry caters specifically to the use, sale and dispensing of cleaning sanitation products that can “blast away” all the microbes associated with food production.
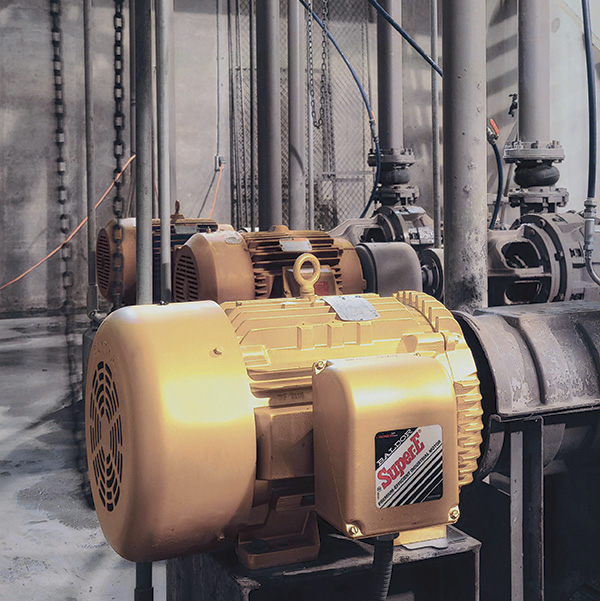
Different Environments Need Different Motors
Pumps that move numerous required liquid products are present throughout manufacturing facilities, and a large number of them are driven by electric motors. Many parts of a food processing plant are considered dry zones. In dry zones, open drip-proof (ODP) pump motors are suitable as long as they do not require cleaning and remain free from moisture or exposure to outside environments. Another common motor seen in other locations—such as a boiler room, a fluid pumping station or perhaps in the on-site water treatment area—is a totally enclosed general purpose motor. While not equipped to handle the harsh and direct spray used in washdown areas, these general purpose motors perform many tasks nicely without the need to upgrade to a fully protected washdown motor. Water or moisture may be present in other areas in which the equipment does not directly contact the food. For instance, some electric pressure washer systems use a totally enclosed general-purpose motor to drive the pump. Although these motors may experience some mist or humidity, if they do not have spray directed at them, a washdown motor may not be required.Food Safety & the Law
Inside a food plant where cheese, chicken, beef or bacon is processed, it is a different story. In these processes, salmonella, listeria, E. coli and other microorganisms thrive in moist or wet environments. If food is not kept free of contamination—from the time it enters the facility until the time it leaves—the consequences can be disastrous. The Food Safety and Modernization Act, signed into law in December 2010, empowered the Food and Drug Administration (FDA) to monitor the U.S. food supply through prevention, inspection and compliance. This new law gives the FDA the authority to shut down a food processing facility or invoke mandatory recalls of any product deemed a threat to the food supply. To comply, food processors are required to follow strict guidelines and establish documented safety measures for their facilities. The FDA works closely with the U.S. Department of Agriculture and the Centers for Disease Control using forensic science to track and isolate the causes of foodborne illnesses.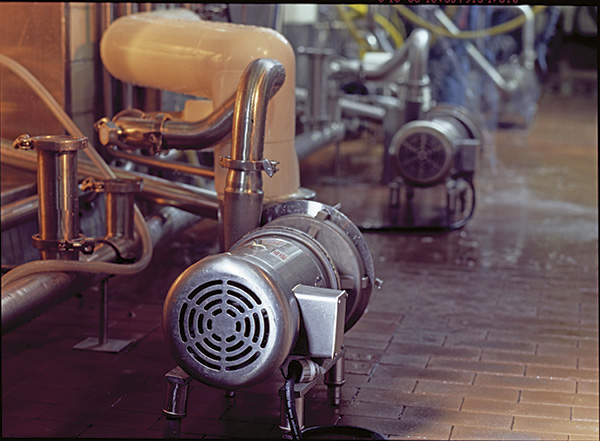
Washdown Environments
In a food-prone environment in which sanitary cleaning is a must, the ideal electric motor for driving all pumps is a totally-enclosed washdown motor. Although some end users attempt to use cast, fin-framed motors (aluminum or cast iron), these types of motors are prone to collecting food and becoming contaminated. While washdown motors and other properly designed electrical enclosures can handle a wide array of spray, the recommendation is to disconnect the motor and all other machinery from the power source during the sanitation process to eliminate any risk of electrical shock. For years, the workhorse of the industry has been the white washdown motor. When white motors were introduced, the primary concern was for motors to run longer than their general purpose counterparts. These motors have been used for years and are still a viable option for applications that require an occasional washdown. Some of the features of these motors include external stainless hardware and shaft, joint sealants, rubber gaskets and seals around entry points, and an epoxy top coat of FDA-approved white paint. Some applications that use these motors include pumping applications using jet pump motors or close-coupled pump motors, which encounter an occasional washdown or regular exposure to moisture and splashing. For end users who require a step up from a painted motor and want to ensure a paint-free exterior on an entry-level budget, a paint-free design may be desirable. These motors provide many of the same features as their white counterparts, using specially processed endplates mounted to a stainless-steel stator band.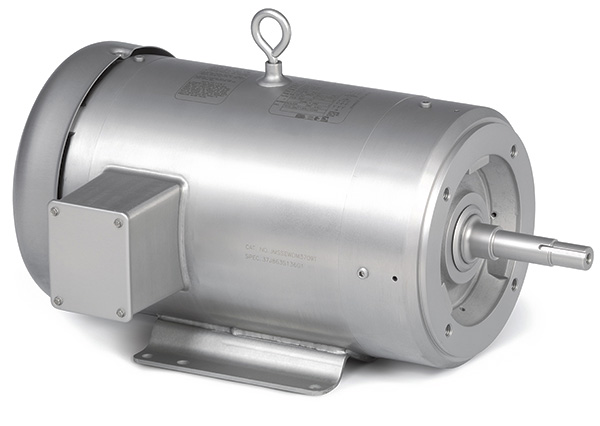
Stainless Motors—the Wave of the Future
While stainless motors were not readily available years ago when washdown motors were first introduced, a growing consensus is that stainless motors are beginning to replace many of the white motors in service. Especially prevalent in wet-food environments, such as meat and poultry production, is the need for motors that can withstand higher temperature spray at much higher water pressure and increased flow rates. End users need motors to run longer without failure. With regulatory control by the FDA, facilities want to remove any areas of their plant that could be perceived as a food contamination issue. Providing stainless motors where necessary and feasible has been the answer.All Stainless-Steel Motors Are Not Created Equal
Maintenance personnel should be aware that many variations of stainless motors are available, including some that are made of inferior components to offset the cost of the stainless steel. While some manufacturers provide entry-level stainless motors, others enhance theirs, providing additional features including improved shaft sealing, smoothly welded contours at potential water entry points and laser-etched nameplate information. For end users who need extra protection, some motors have internal windings that are completely encased in a moisture-repellent potting compound.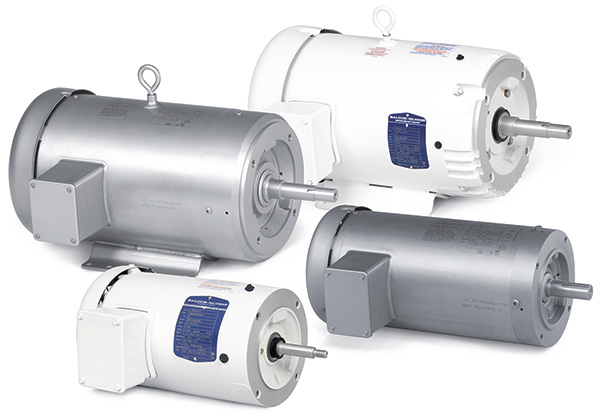