To ensure the best system setup, end users must first consider operating conditions, then conduct thorough cost-benefit calculations.
07/24/2015
In most U.S. states, running a 100-horsepower pump motor continuously for a year can rack up more than $40,000 in energy expenses. Improving efficiency in industrial pumping systems is one way to reduce these costs. While variable frequency drive (VFD) technology can significantly increase system efficiency by controlling pump speed, not every application requires a VFD. To determine when to apply this technology, end users must conduct detailed calculations to verify the cost-effectiveness of using a VFD.
VFD Benefits
A VFD varies the speed of a three-phase, alternating current (AC) induction motor by adjusting the voltage and frequency of the motor's input power (see Image 1). Varying the speed of the motor improves efficiency by changing the pump's output to match actual pressure/flow requirements.
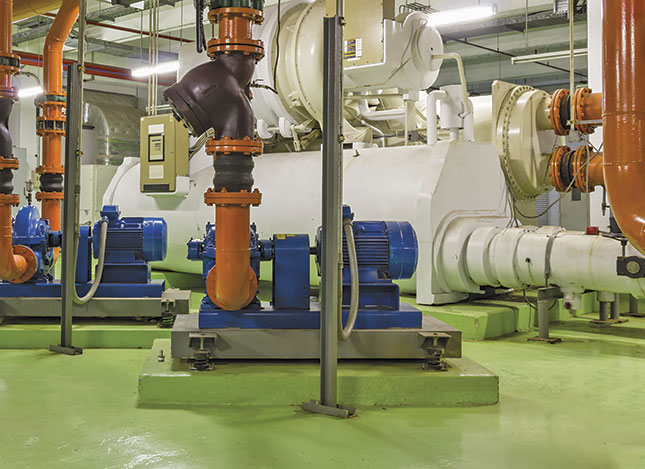
Flow, Pressure2, Power3
The pump affinity laws are based on constant impeller diameter and varying speed. The premise of these laws is that, for a given pump with a fixed-diameter impeller, capacity is directly proportional to the speed (Equation 1), head is directly proportional to the square of the speed (Equation 2), and required power is directly proportional to the cube of the speed (Equation 3).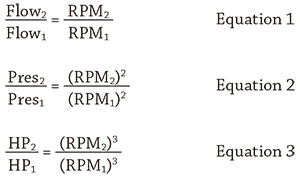
Calculating VFD Cost & Savings
To determine if a VFD is an efficient and cost-effective option for either a new or retrofit design, end users must first consider operating conditions and then calculate cost and energy savings by following 11 steps.- Determine the pump's minimum to maximum pressure/flow (system) curve.
- Include alternate flow paths and related system curves for all operating modes.
- Specify the motor and pump to meet both minimum and maximum requirements on the pump performance curve.
- Estimate time the pump runs at low, medium and high flow rates.
- Estimate cost of kilowatt-hours (kWh) at each flow rate, including a 3-percent VFD loss.
- Translate these costs into yearly savings compared with running the pump at full speed.
- Add in any rebates from the utility for VFD installations.
- Add in reduced maintenance and longer pump life resulting from running the pump at lower speeds.
- Determine the cost of the VFD after installation.
- Add the cost of required supplementary equipment for power factor correction, noise filtering, etc.
- Compare costs and benefits to determine feasibility.
Installation & Control Considerations
The installation of a VFD may require additional components. Electromagnetic interference (EMI) filters, line/load reactors and radio frequency (RF) filters may be needed as part of the installation. Because a VFD is typically larger than the motor starter it will replace, a larger electrical enclosure may be needed. When retrofitting a VFD, the cost of new power cables to the inverter and VFD-rated cable to the motor must also be taken into account. Typical installed costs of VFD systems range from $200 to $500 per horsepower (HP). Suppliers can assist users in selecting a VFD that is properly sized and that includes any necessary filters and reactors. If the application involves an existing three-phase motor, the motor may be used if the winding insulation rating is sufficient. The motor should have an insulation class rating of F or higher. Compare the savings resulting from reduced power consumption with the cost of the installed VFD to determine if the return on investment is sufficient to justify the expense. Operating the pump and motor at lower speeds may lead to increased service life and reduced maintenance intervals, and these savings should be included in the calculations.Application Example
Assume a centrifugal pump operating with a 15-HP, three-phase AC motor has across-the-line starting at 460 volts AC, 60 Hertz. The pump typically turns at a constant speed of 1,750 rpm, consumes 10 HP and discharges 200 gallons per minute (GPM) with a head of 120 feet. A throttling valve is used to vary pump output from 200 to 100 GPM. A review of the system indicates that the pump normally operates with the throttling valve positioned to limit pump discharge to 100 GPM. The reduced flow rate represents 50 percent of the pump capacity, occurring 90 percent of the time. Based on the affinity law, pump capacity is directly proportional to pump speed, so a reduction in speed to 50 percent will achieve an identical reduction in capacity/flow rate (see Equation 4).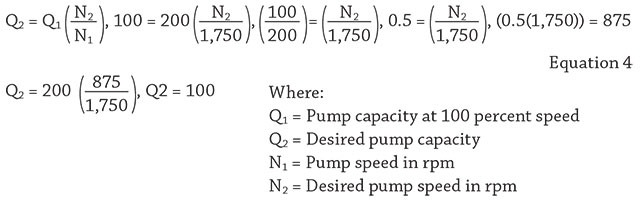
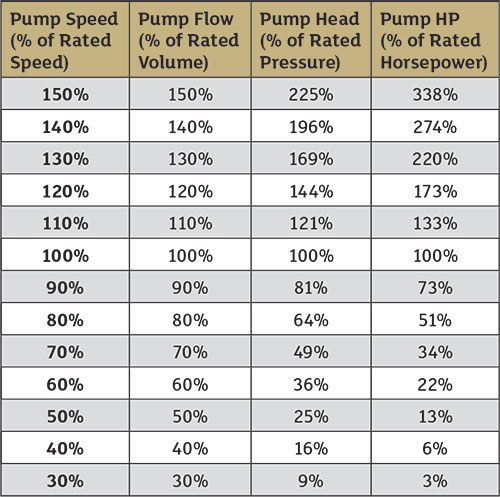