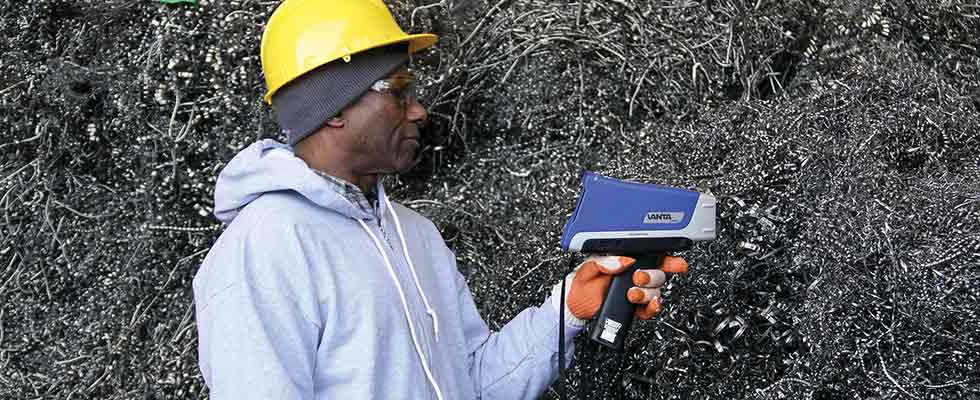
Whose responsibility is it to ensure that the right type of pump is selected? The user’s? Who is responsible for choosing the correct materials for the pump’s construction? The manufacturer? What about ensuring that the pump materials are correct. Who is responsible for that?
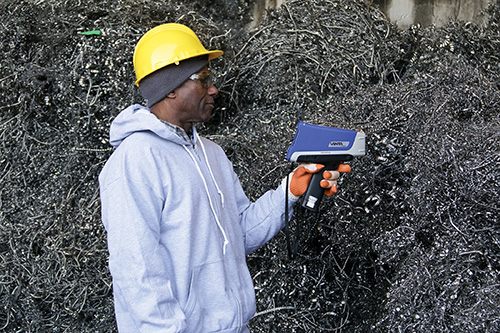
The answers to these questions are critical to both pump and valve manufacturers and users. While choosing the right pump might be straightforward, not everyone verifies that the pump is made of the correct alloy it is supposed to be. There are hundreds of global pump manufacturers and suppliers with thousands of pumps and valves manufactured for and installed in the chemical industry. Mistakes can happen, but using the wrong materials can have consequences. Fortunately, using handheld X-ray fluorescence (XRF) analyzers is a quick and easy way to verify that the correct alloy is being used to provide traceability and help prevent material mix-ups.
Selecting the Right Pump
Centrifugal, diaphragm, positive displacement and turbine pumps are the most common pumps used in the chemical industry. Each has its own method of pumping, depending on the physical and chemical properties of the fluids being transported.
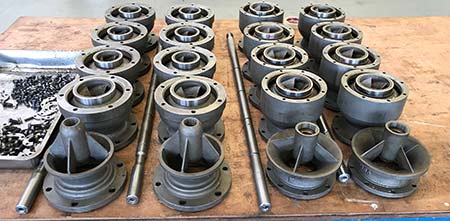
When specifying a pump or valve for a specific application, it is important to understand the operating conditions, operating temperatures and pressures, corrosive tendency, erosive tendency and solids in slurries. Most pump and valve suppliers offer many alloy types, and the choice will depend on the factors mentioned above. For example, typical alloys and applications for casings and impellers include:
- stainless steel: Both SS304 and SS316 are widely used, and SS316 has increased corrosion resistance
- Hastelloy C/Inconel/Alloy 625: These alloys have high nickel and chromium levels with up to 13% molybdenum to provide better corrosion resistance than stainless steel
- titanium: This alloy is ideal to use in oxidizing media, such as hot nitric acid and sodium hypochlorite
Since it is important to use the right alloy for the right application, pumps and valves should be tested during manufacturing, assembly, testing and whenever installing or replacing a part.
Manufacturing
For the chemical industry, almost all pump bodies are made from cast metal alloys, depending on the intended use. The primary raw materials for the castings are scrap metals and revert material.
So, purchasing high-quality materials and verifying their chemistry prior to melting are imperative to help ensure the reliability of the final product. Depending on the material grades for the pumps and valves being cast, scrap may be purchased from various sources, making sorting and testing prior to melting even more critical.
Due to the complexity of the casting process caused by varied material inputs, it is good to test all incoming alloys prior to assembly if castings and machined components are purchased from a third party or supplied by another facility.
Assembly & Testing
When assembling pumps and valves during the manufacturing process, it is important to verify the material identification of the various components, such as the body, impellers and flanges. This process provides traceable data for each product manufactured. With myriad pump and valve suppliers and applications, the number of materials used during the manufacturing process is significant.
For example, a pump made for transporting hot acid can be made of a nickel alloy, but a pump with the same size and design is also sold for lighter duty applications, such as transporting acetic acid. In this case, it might be made of SS410. These two pumps will look identical. If a pump is ordered for hot acid, but one made of SS410 is installed, the casing or impellers can fail and can affect the chemical product.
Maintenance & Replacement Parts
Lastly, the alloy ID of stock parts and complete pumps and valves should be inspected on receipt and again at installation to ensure complete traceability.
How Handheld XRF Works
Handheld XRF analyzers verify that the right alloys are being used. How they work can be broken down into four simple steps:
- Emission: First, the analyzer emits X-rays.
- Excitation: The X-rays hit the sample, causing it to fluoresce and send X-rays back to the analyzer.
- Measurement: The analyzer’s detector measures the energy spectrum from the X-rays it receives. This detects which elements are present and the amount of each element present. It is important to note that handheld XRF analyzers cannot be used to measure every element in the periodic table. In general, handheld XRF analyzers can measure the elements from phosphorus to plutonium (P–Pu).
- Results: The analyzer’s electronics process the energy spectrum and display the sample’s elemental composition. For metals, some analyzers will match the composition to a specific alloy grade.
Features to Look for in a Handheld XRF Analyzer
There are many handheld XRF analyzer models available, and their range of features also varies widely. It is recommended to only pay for what is needed to minimize the total cost of ownership. When looking at available XRF analyzers, purchasing one with the following features is recommended:
X-Ray detector protection:
One of the most expensive repairs in a handheld XRF analyzer is a detector replacement. Choose an analyzer that has features to help protect this critical component. Some analyzers have a shutter that closes to protect the detector while others use a protective material over the detector window, such as Kapton, that can be easily attached and changed if it gets damaged.
Rugged:
Manufacturing and in-field testing are both demanding environments. Make sure to choose an instrument that is up to the task. The last thing a user wants is an analyzer to fail at a critical time. Look for an XRF analyzer that is IP-rated for protection against dust and water intrusion and built to pass a 4-foot drop test (MIL-STD-810G).
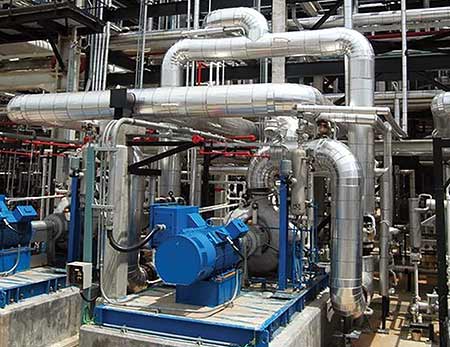
In hot or cold environments, look for an analyzer that can perform continuously in a wide temperature range, such as −10 C to 45 C (14 F to 113 F).
Easy to use:
Make sure the XRF analyzer has enough onboard storage to hold all of the results (at least 1 gigabyte [GB]). The analyzer should also make it easy to offload the data. At minimum, the analyzer should have USB ports for easy data export, but some modern analyzers also have optional wireless connectivity, which makes things even easier. With wireless connectivity, the analyzer can connect to the cloud for easy data transfer, fleet management and more.
The ease of use of the analyzer’s interface is also critical. Employees should be able to pick up and use the analyzer effectively with minimal training. Look for an analyzer that has smartphone-like navigation (swiping, flicking and tapping). Some XRFs enable customization of what features appear on the instrument’s home screen, just like selecting apps on a smartphone.
Other features offered by some popular handheld XRF analyzers include:
- remote troubleshooting/calibrations and real-time instrument health status
- an onboard barcode scanner that can read SKUs, lot numbers, heat numbers, ISO codes, etc.
- the ability to create custom data reports in multiple formats, including spreadsheets and PDFs
With the critical nature of pumps and valves in the chemical industry, handheld XRF is an ideal solution for nearly all alloy verification and analysis tasks, providing material traceability throughout the manufacturing process and the life of pumps and valves. Using a handheld XRF analyzer can enhance quality, efficiency and profitability whether manufacturing pumps and valves or simply using them.