In the quest for energy efficiency and machine automation, more engineers, facility managers, and building owners are turning to variable frequency drives (VFDs). As one of the most promising “green” technologies available, VFDs allow users to operate motors at less than full speed while maintaining the required torque. In fact, VFDs can reduce an electric motor’s power consumption, saving 30 percent or more in electric energy costs. VFDs, however, can require additional protection for the equipment. VFD-induced common mode shaft voltages can damage bearings through the process of electrical discharge machining (EDM), which can shorten electric motor bearing life and reduce the reliability of these systems. To mitigate these voltages, long-term shaft grounding is essential. An effective way to protect electric motors from electrical bearing damage is to install circumferential conductive microfiber shaft grounding rings. Most VFDs use pulse width modulation with insulated gate bipolar transistors to control switching. The output of these drives includes a fluctuating common mode voltage that electrostatically induces voltage on the motor shaft. This shaft voltage tends to discharge through the bearings, possibly causing EDM bearing damage. Shaft voltage can be measured using a digital oscilloscope—with a bandwidth of 100 megahertz (MHz) or higher—by touching a conductive microfiber probe tip to the spinning shaft of a motor. Without a circumferential conductive microfiber shaft grounding ring, shaft voltage will discharge through the motor’s bearings (or those of coupled equipment), then through the motor’s housing to achieve electrical earth ground. The shaft grounding ring protects motor bearings by offering an alternate path to ground for shaft voltage—directly from the motor shaft through the ring to the motor’s housing (ground), avoiding the bearings altogether.
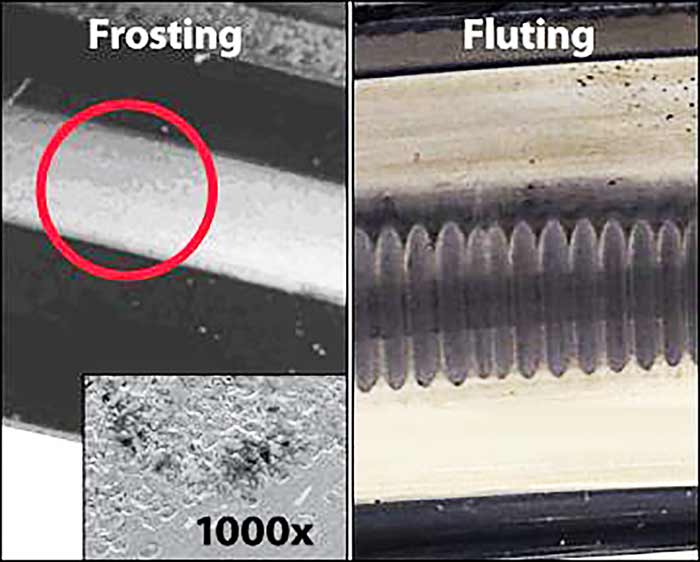