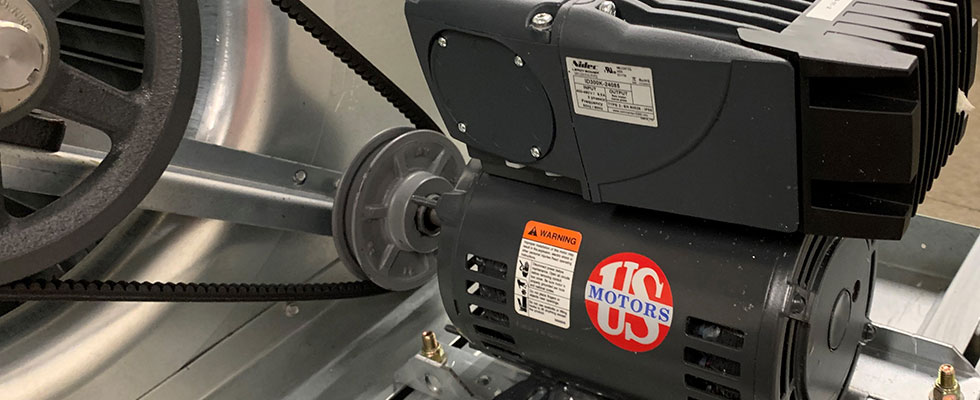
The drive to achieve ever higher levels of energy efficiency shows no signs of slowing down. In fact, the opposite is true. For example, the heating, ventilation and air conditioning (HVAC) industry has numerous new Department of Energy (DOE) regulations launching in 2023, and pumping applications also have a new DOE test rule.
At the offices of motor manufacturers, phones are ringing and emails are pouring in. Commercial HVAC equipment manufacturers are asking questions like, “Will my motor still be compliant this year?” or “Will my motor be enough to get to the new system efficiency?”
One new DOE requirement that the industry is concerned about is that all commercial air conditioning and heat pump equipment from 65,000 British thermal units per hour (btu/h) to 760,000 btu/h must achieve an additional 15% efficiency increase from the 2018 ratings. This is consistent with other stated goals by the DOE to increase levels on other products by reducing losses by 10% to 15%.
HVAC manufacturers are also preparing for new rules for furnace fans and new test methods for central air conditioners, electric motors and variable refrigerant flow (VRF) multisplit units. New test rules and efficiency standards are also in process for commercial pumps, air cleaners, fans, blowers and circulator pumps. In addition, a DOE sponsored negotiation for an updated test method and efficiency standard is under way for unitary air conditioners and heat pumps.
Industrial pump manufacturers are also anxious about keeping up. Serving a wide range of industries, a myriad of energy-related regulations and rules must be tracked and considered in pump design and motor selection. New rules have been announced for dedicated circulator pumps used in hydronics, commercial/industrial pumps for irrigation and water treatment and dedicated pool pump and pool pump motors.
Motors that power HVAC and pumping equipment are arguably one of the most critical pieces of the energy puzzle, as electric motors account for 45% of global energy consumption, according to the International Energy Agency (IEA). That is why the most efficient use of energy from motors is key to slashing energy usage. That includes motor efficiency but also implementation of variable speed motor solutions particularly in air and liquid movement.
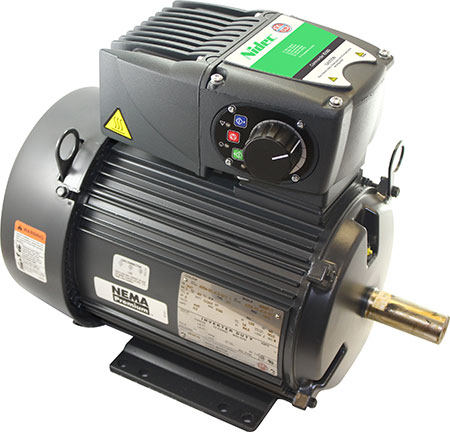
The good news is that motor technology has been evolving at a rapid pace over the past several years, as manufacturers are focusing resources on energy-efficient technologies, such as power drive systems (PDS), integrated motors and controls (IMAC) and synchronous motors.
Understanding these technologies can help pump and HVAC equipment manufacturers better review their options to achieve the efficiencies needed.
Energy Advantages of IMAC & PDS
A motor technology that was introduced to the residential HVAC market 15 years ago is now gaining traction in both commercial HVAC and pumping applications, offering a host of benefits, including greater energy efficiency and easy drop-in motor replacement.
These integrated motors with on-board controls or variable frequency drives (VFDs), known as IMAC, make it possible to operate pumps and blowers at different speeds based on system demand, rather than at a single, maximum capacity speed that eats up energy unnecessarily. The DOE reports that reducing IMAC speed by 20% can in some cases cut power usage in half.
In pumping, as well as commercial HVAC applications, oversized, single-speed motors are still prevalent. They are designed to meet maximum system demand, even though the pumps rarely operate at full capacity.
Fortunately, the advantages offered by IMAC technology, and the fact that it has been proven in the field and backed up by research, have led to recent growth in commercial and industrial fan and pump applications.
In addition to the DOE report, research by the Northwest Energy Efficiency Alliance (NEEA) and other industry groups, verify that IMACs help lower energy bills. A NEEA study of IMACs and other PDS found that pairing a motor and an adjustable speed drive or control reduced energy consumption by up to 45% for variable load systems and up to 23% for constant load systems. A PDS includes a motor and an adjustable speed drive or control but, unlike an IMAC, the two may or may not necessarily be assembled as an integrated unit.
The NEEA calculated that IMAC or PDS payback is 10 months for constant load systems and only four months for variable load systems.
Using a synchronous motor produced even greater savings. When paired with smart building technology, synchronous motors create a more efficient system for blower or pump systems than induction motors by matching application demands with variable speed.
Implementing IMAC
Because the motor and control have been designed to operate together, IMAC advantages consist of more than just the elimination of the setup and wiring. The engineer can expect efficiency improvements, simplified design and system integration, reliability and compatibility as well.
IMACs offer a high efficiency drop-in motor with controls mounted on top to replace lower-efficiency, single-speed products. Motor manufacturers use the same base mounting dimensions used on single speed motors so that the IMAC fits onto the existing pump or fan. The only major issue an installer could encounter when installing an IMAC would be the available clearance above the motor where the drive is now located.
Motor to control optimization is easier with an IMAC product because the specific parameters of the motor are factory-installed into the drive. This includes feedback type and resolution, motor characteristics and optimal points for synchronous motor designs, including permanent magnet (PM), synchronous reluctance and hybrid designs combining both technologies of motors, if used. Motor and control efficiency improves because the control is better matched with the motor.
In current product offerings, both induction and synchronous IMAC designs exist, but IMACs that are integrated with a synchronous motor and VFD are close to becoming the standard in fan and pump applications in HVAC. A common term applied to a synchronous motor IMAC is an electronically commutated motor (ECM). An important item to note is that the DOE has not assigned efficiency standards to ECM motors as a motor/VFD combination. The new motor test rule does specify the test method for ECMs but not an efficiency level. Many other DOE rules do require synchronous motors to meet the higher-level system efficiency that includes consumer furnace fans and the proposed circulator pump efficiency level, which both typically use a synchronous motor IMAC.
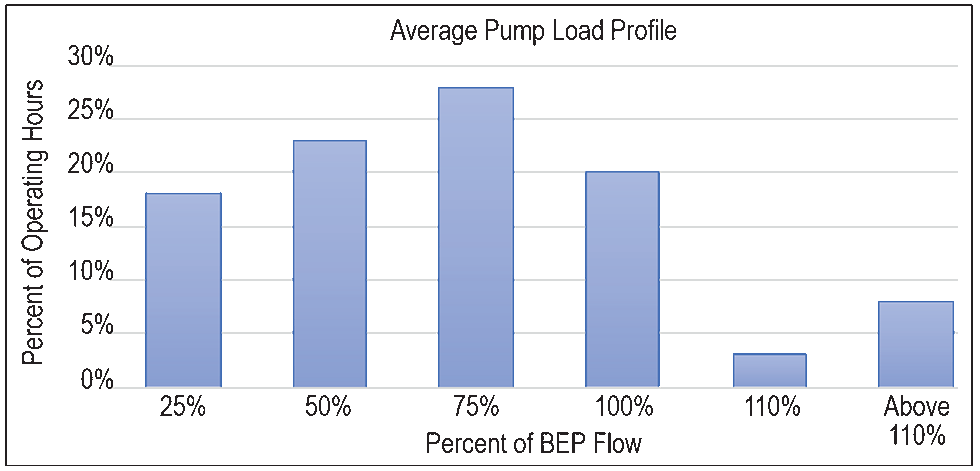
The IMAC design also eliminates the need for on-site wiring between the motor and the control. This allows the end user to avoid the expense of hiring an electrician at a high hourly rate.
Because the control is mounted to the motor in an IMAC, the motor’s insulation integrity is improved by eliminating or minimizing high voltage spikes which can occur when controls are located at longer distances from the motor. Many IMACs also eliminate the requirement for shaft ground rings and other expensive motor features associated with using motors with controls.
While most control manuals consist of more than 100 pages of instructions, most of the pump or fan configuration details are already complete with an IMAC, and this will result in faster and reduced risk installations.
Smart sensors and IoT
Many IMAC or PDS units today connect to a sensor which provides the motor control system information. In a hydronic pump example, a gallons per minute (gpm) sensor would continuously send the motor control the current gpm rate, and if the gpm was lower than the target rate, the motor control would increase the rotations per minute (rpm) of the motor to meet the target.
Newer systems use Internet of Things (IoT) rather than older communication between sensors and IMAC. As commercial buildings move further towards becoming smart buildings, this trend is expected to continue. In a smart building, just one building maintenance person with a notebook computer can monitor and control the operation of elevators, heating/cooling systems, pumps, cooling towers and fans. PDS and IMAC will be instrumental in moving commercial buildings to become smart buildings.
A Future With IMAC as the New Standard
With all of its advantages, IMAC is expected to emerge as the new standard for commercial HVAC and industrial pump and fan applications. Pool pump makers have taken the plunge into IMAC as have many other industries.
The next motor range to convert is 2-10 horsepower (hp) for both pumps and fans moving heavily into the commercial HVAC space. Currently, for many of those applications, the motor and VFD are separate, but that will be changing as variable speed becomes a requirement in many cases to meet efficiency regulations.
As motor manufacturers continue to make investments in R&D and technology, the pumping and HVAC industries will benefit not only by staying ahead of new rules and regulations but also by delivering the highest energy efficiency to users.