Industrial equipment users are often confronted with pump parts issues. Handling these issues requires making experience-based decisions and prioritizing. How pump hydraulic and wear components in existing inventory are treated is an issue that merits consideration. Plant size, age, past purchasing, maintenance and storage-related practices are among the factors that affect a facility’s status with respect to operational readiness and downtime risk. As these generally-known facts are applied on a pump component level, it is often determined that the specific pump components in the storehouse may not be the same as the components currently operating in a particular process centrifugal pump. Nor is it always the case that truly optimized components are presently installed. Therefore, the risk of unforeseen downtime can be reduced by having the right parts on hand. If the parts are truly optimized, installing them at the next opportunity will take the facility beyond being back in business—it will actually take the equipment owners to greater profitability. To ensure that pumps will perform their intended functions, inventoried or stocked parts should be thoroughly inspected and corrected as needed prior to installation. Incoming inspection is practiced by best-of-class equipment owners and only verified-as-correct parts will be placed in the storehouse. This case study examines a real-life scenario and demonstrates essential precautions that can be taken when procuring pump hydraulic and wear components.
A Condensate Pump Repaired & Improved
During a planned outage, a nuclear power plant (NPP) sent a three-stage condensate pump to a highly experienced service center with hydraulic pump design engineers on staff. The NPP provided the hydraulic components, wear rings and bearings from its stock inventory for the pump rebuild project. The hydraulic pump design engineers at the service center performed a thorough inspection of both the disassembled rotor and the parts supplied by the NPP. A visual inspection quickly revealed that the geometry of the replacement impellers did not match the impellers that were removed from the disassembled pump (see Figure 1).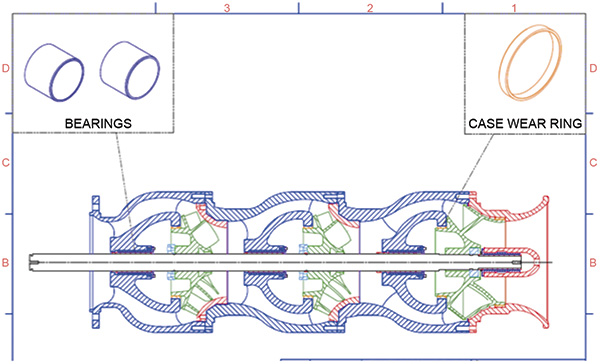
First Mapping, then Comprehensive Engineering Analysis
Figures 1 through 6 are examples of the extensive mapping of before versus after conditions of virtually all components of this condensate pump. The service center hydraulic pump design engineers performed comprehensive engineering analyses which overlapped and intermeshed the mappings. In this instance, the analyses included three-dimensional (3-D) modeling using late edition ANSYS software.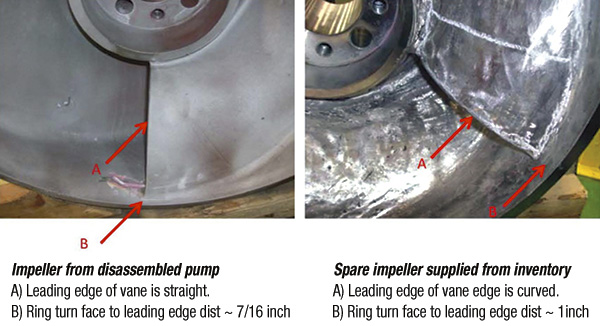
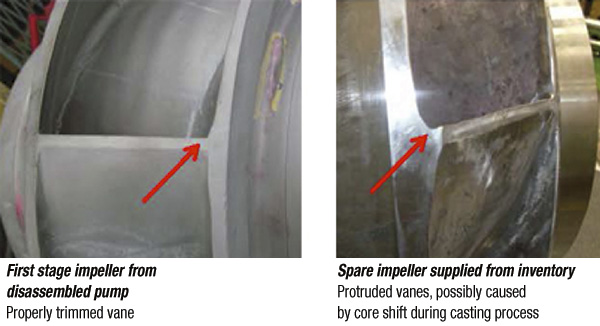
Restoring the Impellers
The service center engineers’ comprehensive engineering analysis determined that using the replacement impellers would alter the pump’s hydraulic performance. Therefore, the service center proposed suitable modifications to each of the three stages. On the spare suction impeller, the modifications included profiling the vane inlet to increase the throat area, enlarging the suction eye diameter and tapering the vane outlet to correct the protrusions shown in Figures 2 and 3. The proposed modifications for the intermediate-stage impellers included the proper profiling of the vane outlet in addition to trimming and “underfiling” the diameters to the appropriate dimensions. With the NPP’s approval, the service center made the modifications and polished the flow passages to improve the hydraulic performance of each spare impeller.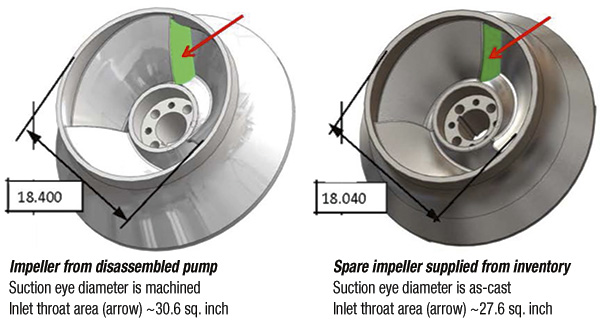
Wear Rings & Bearings
The service center’s in-house engineering team evaluated the wear rings and bearings supplied by the NPP’s store room. Next, the NPP was informed of the component discrepancies and that the dimensions of as-supplied spare parts would not meet sound acceptance criteria.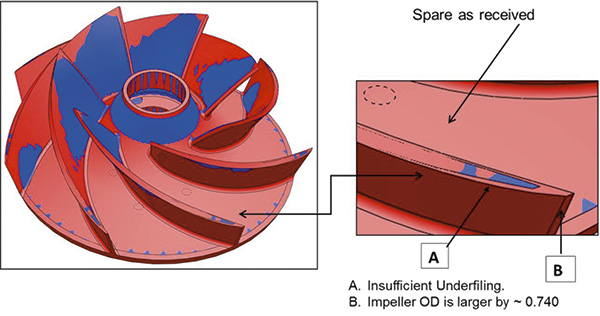
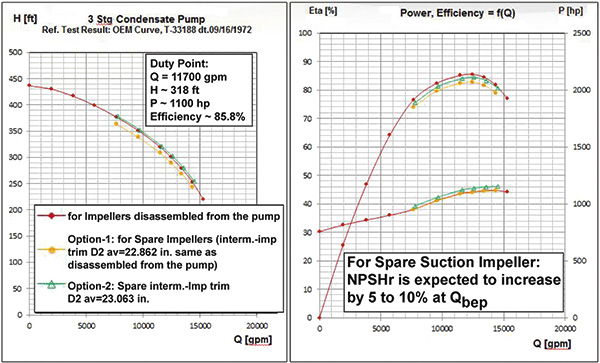
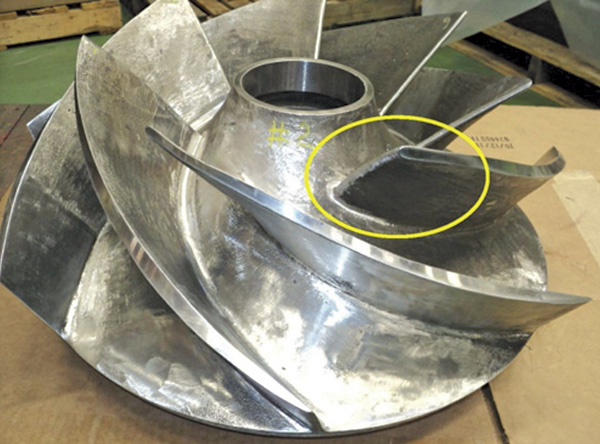
Pump Performance testing
The NPP agreed to have the rebuilt pump tested at the service center’s independent test lab in Chicago. The results of the test are shown in Figure 8. The plots confirmed that pump performance was enhanced and that no increase in power demand would occur. The engineered upgrades improved the pump’s efficiency, which translates into a reduced carbon foot print and energy savings for the NPP’s owners.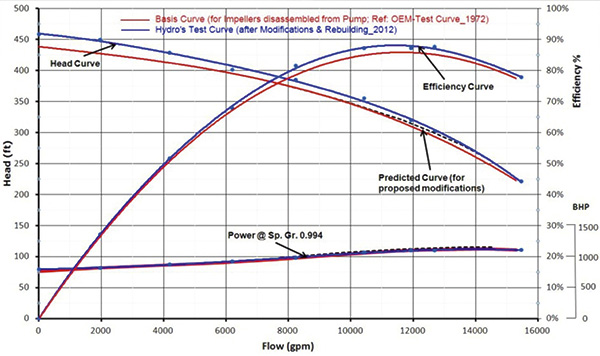
Summarizing the Guidelines
Important guidelines for the procurement of important spare parts can be inferred from the case history presented here:- Purchase wear components with extra stock. Finish-machined parts may not fit in repaired bowls and impellers. When purchasing spare parts, make sure extra stock is available to allow the components to be machined to size. This will provide an optimal fit, which will help reduce the likelihood of problems upon startup and during operation.
- Test hydraulic components prior to re-installing an essential pump. Pump rotor refurbishment will usually present an opportunity to obtain accurate performance data. A test plot will ensure the spare or rebuilt rotor will perform its intended function. Ensuring repeatability of pump performance is especially critical for safety-related pumps.
- Use checks and balances in the inventory-receiving process. Whether replacement parts are ordered from the OEM or a third-party supplier, always have a method of checking the parts to ascertain equivalency of the hydraulic components. It is important to document the various and sundry “attributes of parts and components.” This may be accomplished by cataloging component particulars for the owner entity’s in-house records. If inconsistencies are found, contact the supplier. Ask the supplier to explain and/or rectify discrepancies. When in doubt, work with an experienced and reliable pump service center. Such a service center will have its own engineering group.