The facility upgrades required a temporary system to divert flow and avoid interruptions during the work.
Xylem, Godwin, Flygt
09/23/2016
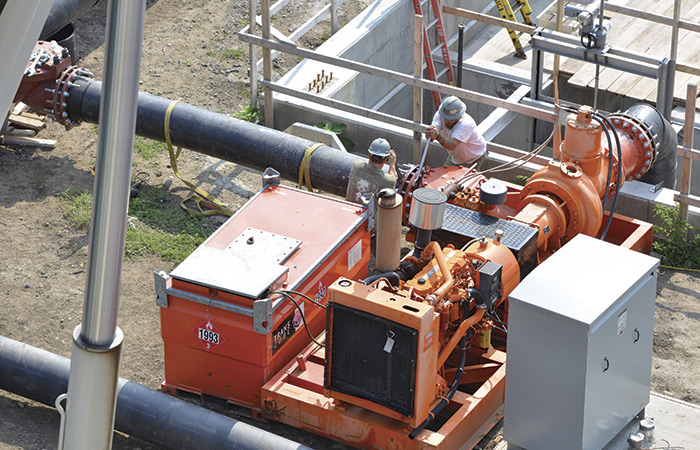
A Unique Pump Solution
The bypass would need to handle 88 million gallons per day (mgd) of flow, and the initial plans from BCI had called for 12 pumps at each site. Once additional assessments were made, the pump technology provider recommended that each plant use three 16-inch, high-volume, medium-head, solids-handling dewatering pumps with automatic self-priming systems. At the North plant, three additional axial-flow dewatering pumps were added, while the South plant used two of the axial-flow pumps. The axial-flow pump that was incorporated into these two plants “isn’t traditionally used in wastewater treatment plants,” according to one pump supplier representative. “It’s usually used for freshwater or flood control, so it’s not the norm. We’ve used these pumps in similar applications and have had great success.”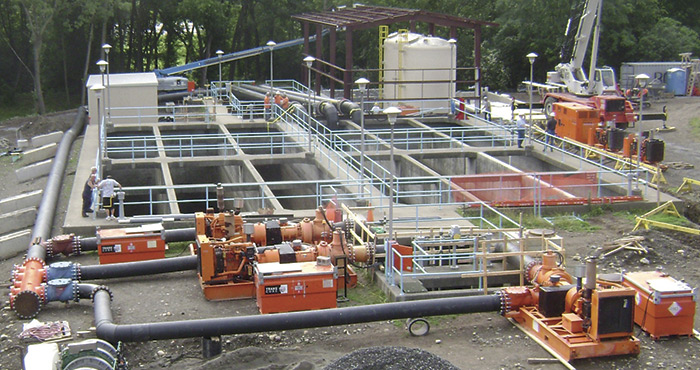