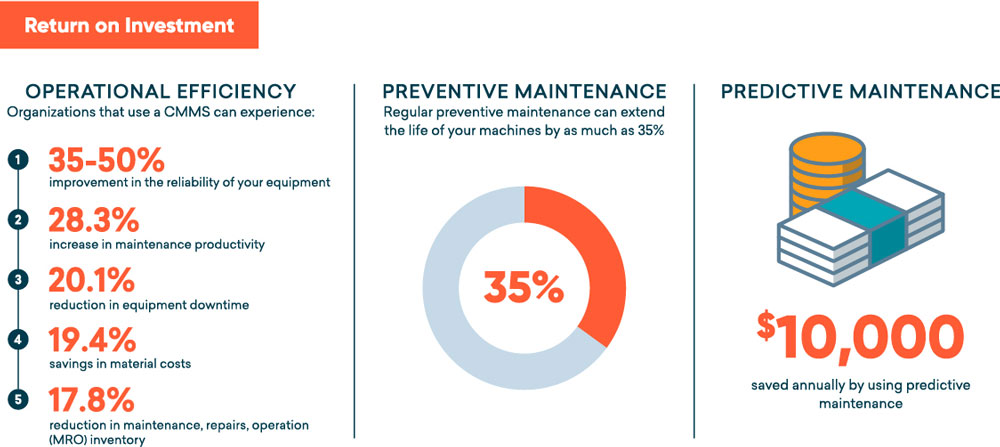
Although many in the industry may still see it as a cost, a computerized maintenance management system (CMMS) is an investment opportunity that offers organizations a solid return on investment (ROI). If organizations only look at the expense of a CMMS, it can be viewed as a large number, which may be a hard pill for the uninformed to swallow.
Instead of focusing on the price tag, manufacturers must focus on the investment and value from a well-implemented maintenance solution.
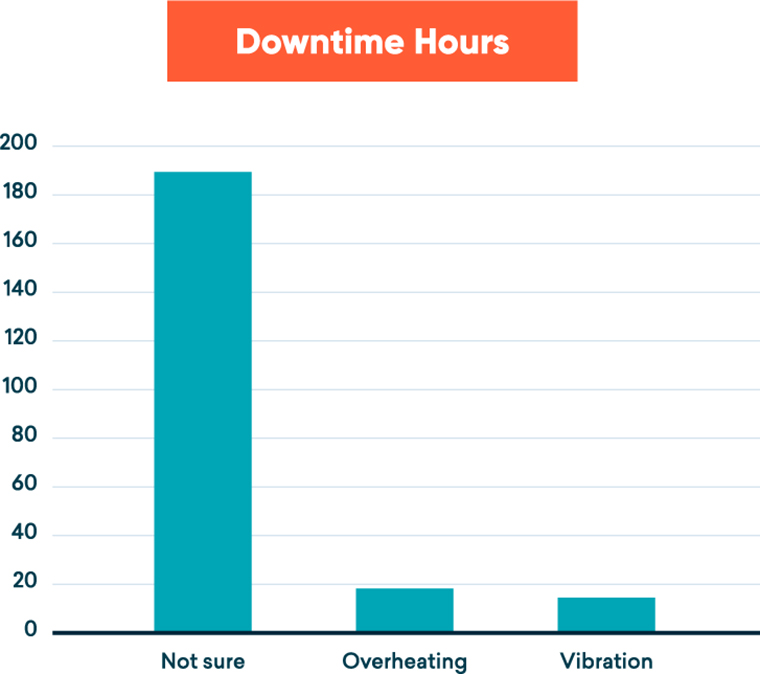
A CMMS can help save time and enable organizations to operate more efficiently. There are obvious benefits, such as controlling standard costs around assets, labor and spare parts. But it can also help reduce unforeseen costs including those that are regulatory-related or prematurely failing assets and more. There are also less obvious benefits: A well-run maintenance department can improve morale within the team, support frictionless organization growth and improve safety. All of this can lead to improved profitability and exceed the amount spent to acquire a CMMS solution. So, as organizations improve their pump and system maintenance operations, operational costs go down and profit improves. This article will cover the obvious—and not so obvious—benefits of a CMMS and why a well-implemented CMMS should be at the heart of a safer work environment and better-quality products.
Quality Is Key
Managing and ultimately improving maintenance operations requires the use of quality data. “You cannot fix what you cannot measure,” is a mantra many in the industry follow.
Take downtime, for example, where the quality of data, and the resulting metrics, analytics and reporting, will be a key aid in making operational improvements and understanding the root causes. Organizations should attempt to avoid the classic “garbage in/garbage out” situation.
Most CMMS software will show reports of where downtime is coming from, including problem code, cause code, etc. An example is shown in Image 1.
A CMMS should provide ample opportunity to fill in work order fields to tell a more precise, comprehensive story. While some maintenance techs and administrators may take shortcuts and not fill in the fields or use “not sure” as a catchall, this is a critical omission. Taking the time to fill out these fields will offer a better picture of the downtime’s cause.
The report in Image 2 is clearer on what the sources of downtime are and provides an opportunity to mitigate those issues to help promote more uptime.
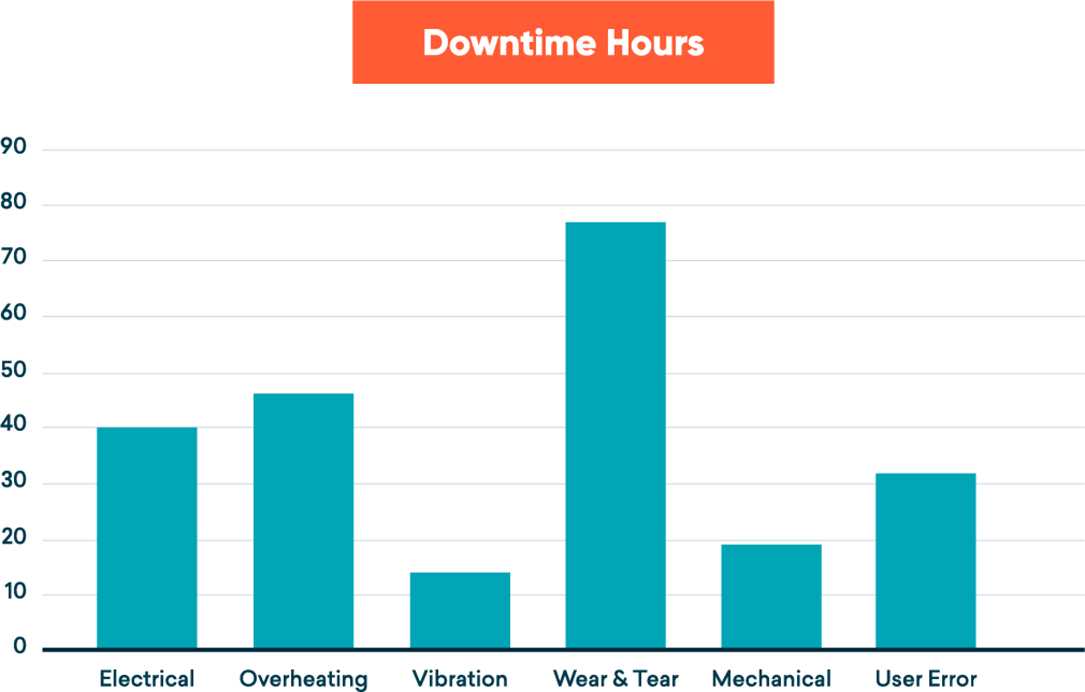
Granularity Matters
Investing in a CMMS to optimize maintenance operations must be done smartly and strategically. If done poorly, the implementation of a CMMS will not provide the granularity needed for superior operational and financial improvements. For example, having hundreds of thousands of work orders in the CMMS, but only a few assets in the system, means 99% of the orders are not associated with any specific assets. It is essential to build a proper and granular asset hierarchy so work orders can be created down to the specific asset or location.
A solid CMMS will have the ability to create a hierarchy starting at the highest level of the organization, then break down assets into regions, sites (geographically isolated campuses), buildings, production lines, specific assets, sub-assets or similar. It is critical to prioritize the initial setup of the overall organization hierarchy (including adding essential assets), which can then add additional assets over time. It is important to associate these work orders to the proper asset or location to manage work orders more efficiently and provide better analysis, which can provide better “math,” identifying where companies can make efficiency optimizations.
Quantity Matters
The longer an organization uses a CMMS, the more data points can accumulate to inform analysis and predict trends.
As more work orders and other data comes into the system, it can become easier to spot trends.
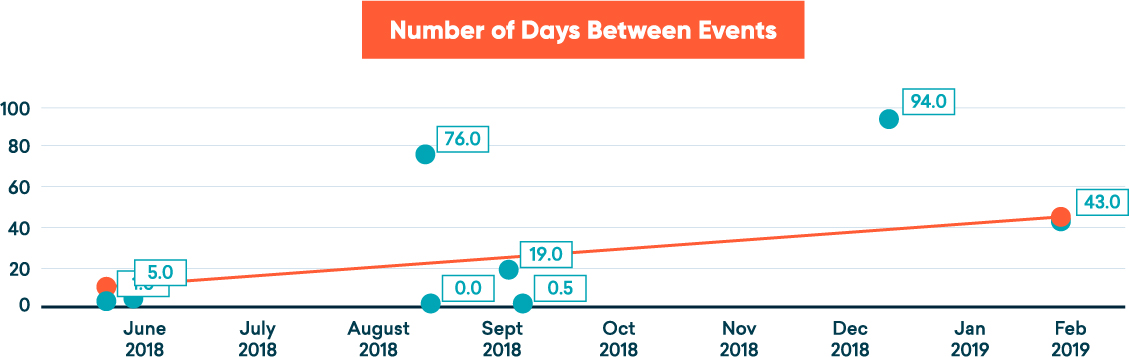
Increasing the quality and quantity of data does not have to take years—small time periods can be analyzed as long as there is a decent amount of data present within that time period. The longer a CMMS is used, the better the quality of data will be shown, creating more accurate “math” to help make decisions.
Different Math for Different People
A CMMS will typically produce many reports, metrics, key performance indicators (KPIs) and other analytics. The math might be viewed differently depending on the role in the organization. Here are some examples.
Maintenance technician
The technicians are the operational lifeblood of a manufacturing organization. They need to know the answers to operational questions such as:
- How many work orders are on my plate?
- Do I have the parts in stock that I will need?
- Am I on target for my goals?
The math will be less financially focused and will allow maintenance personnel to do their jobs efficiently and accurately.
Maintenance manager
Maintenance managers live in the operational and financial worlds. One minute they are assisting a technician on a production asset, the next they are presenting a budget update to the finance department. These managers need reports and analytics to show how they are doing operationally and financially. Questions managers may need answered include:
- How is my preventive work orders/corrective work orders ratio?
- Where is my downtime coming from?
- How well is my team’s workload balanced?
- Is my team completing its work on time?
- Are we hitting our safety goals?
This analysis can be viewed in different manners, from KPIs on a dashboard to detailed reports, down to specific assets or high-level summary charts.
IT manager
Since today’s CMMS software is cloud-based, typically information technology (IT) has a smaller role in the search and installation process. Gone are the days of having servers, networks and people to manage on-premise software implementations. Now, organizations need quality internet access and related IT support. Cloud-based software has a lower total cost of ownership (TCO) due to lower upfront expense, and the reduced amount of IT hardware and people needed to run the technology. It will also have additional benefits like lower energy consumption. There are technical advantages as well: A CMMS can be used anywhere and anytime it is needed with real-time mobile access and access to the latest version. All of this can lead to easier IT management and reduced expenses.
Chief financial officer (CFO)
Professionals on the financial side will need to see how the cost-related aspects of operations are performing. A well-implemented CMMS should show a variety of analyses proving the maintenance team is achieving a lower overall budget, increased productivity, better management of parts and impact of supply-chain. There are other adjacent areas as well, such as regulatory and compliance adherence. Additionally, a CFO can access more detailed analysis around specific special projects and determine which assets might be costing too much.
Turbo-Charge the Math
CMMS software can be complemented by lean initiatives such as 5S, Six Sigma, Total Productive Maintenance (TPM) and similar. TPM—more specifically the autonomous maintenance pillar—empowers production-line operators to perform basic inspections, cleanings and preventive maintenance (PM) tasks when they start their shift. Catching little problems early prevents big problems from ever happening—a great way to improve “math.” A CMMS is capable of managing these TPM processes.
Offset the Investment
Investing in a CMMS can pay off—faster if aided through professional services such as implementation consulting, training, data migration and a help desk. A maintenance team can use its CMMS like any other tool in its arsenal, aiding efficiency efforts.
Overlaying the costs to the numbers above, the math is clear. CMMS software can offset the original investment and help make a more competitive, efficient and profitable organization.
As organizations improve their pump and system maintenance operations, costs go down and profit improves with a well-implemented CMMS is at the heart of this mission. Creating a preventive maintenance culture and streamlining work orders can lead to more efficient operations. Additionally, safety concerns and business and environmental risks may decrease.
Streamlining operations for efficiency is a continuous improvement process and a CMMS should be a part of this journey, as well as a quality, well-executed implementation. This progress is contagious, and the math will show improved, efficient and more profitable operations.