As power generation plants age, flexible and efficient operational systems are even more critical to meet changing electrical power demands. Plants require continuous production with minimal risk of disruption. As a result, power generation stakeholders are developing online condition maintenance strategies and procedures to prevent failures, ensure optimized maintenance schedules and avoid economic and environmental consequences. A single plant can have several thousand critical and noncritical assets, such as turbines, electric motors and pumps. These assets are vital to reliable, efficient operation and act as leading indicators of a plant’s effectiveness. Fortunately, online condition monitoring and predictive maintenance can reduce rotating equipment and motor failures. The most effective plans combine two elements. They include online condition-monitoring strategies—such as trending factors like leading triggers and alarms that are designed to address degradation—coupled with traditional practices to condition monitoring. Plans that focus on vibration and excessive temperature—the leading causes of equipment failure—can minimize damage and shorten plant downtime.
What Is Condition Monitoring?
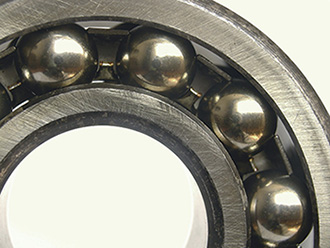
Automated & Manual Condition Monitoring
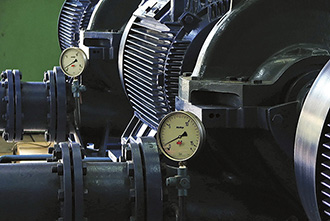
Choosing a Condition-Monitoring System
Before choosing a condition-monitoring system, end users should consider which machines and failure modes must be monitored. The breadth and number of machines and the types of measurements needed to detect the failures will form a basis for this decision. For example, fusing measurements from different sensor types will provide a more accurate diagnosis. When implementing a large-scale condition-monitoring system, three main technology considerations come into play. The first is data management, which involves an appropriate data structure, database considerations for easily mining data, alarms and an aging strategy. The second is data analytics, which includes application-specific algorithms and higher-level predictive prognostics. It involves both real-time decisions and embedded intelligence closer to the sensor source, as well as at-rest data analytics on servers using aggregated data from multiple machines. As the use of data acquisition and monitoring systems increases, data management and data analytics become more complex, and a third consideration becomes critical—systems management. Remotely managing several monitoring systems helps increase reliability, serviceability and overall solution availability. This software solution makes it possible for end users to visualize and manage data and results, simplifying remote management for large numbers of monitoring systems.Selecting a Vendor for Condition-Monitoring
End users should consider the following criteria when selecting a vendor for a condition-monitoring solution (see Figure 1):- The flexibility of the solution to scale with evolving needs, such as support for new types of algorithms, support for a wide variety of input/output (I/O) and emerging sensors, and the ability to scale to large numbers of systems
- The openness of the platform to enable access to raw engineering measurements and extend the solution to meet maintenance program requirements
- Interoperability with third-party hardware and software packages that allows for integration with existing computerized maintenance management systems (CMMS) and enterprise resource planning (ERP) systems, as well as database historians or process management enterprise software
- The breadth and quality of the company’s product offering, including the ruggedness of hardware and number of available algorithms
- The price of the monitoring hardware and software solution
- The services offered to help facilitate an end-to-end solution from the asset to the IT infrastructure, either directly or through a network of partners
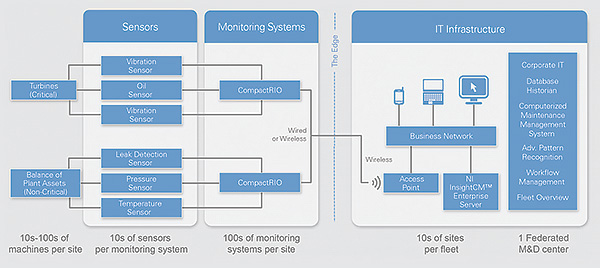