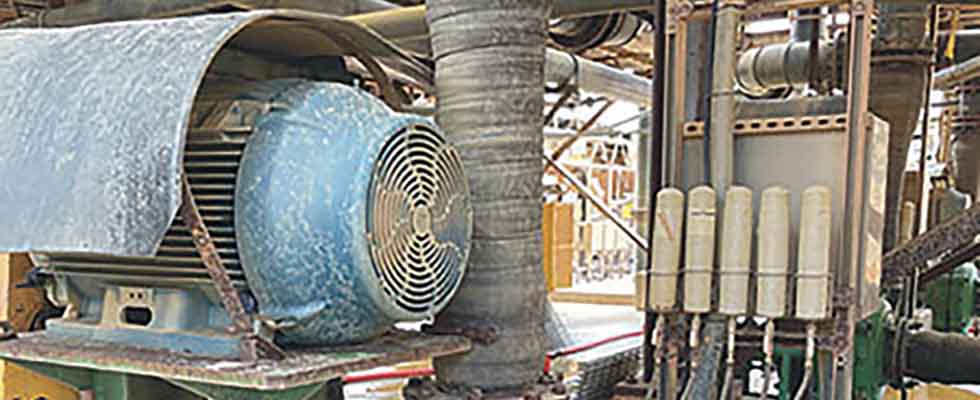
In industrial pumps, bearings play a crucial yet underappreciated role in any one pump’s reliability and uptime. With significant attention given to impeller design, motor efficiency and seal performance, the supporting bearings can be the “forgotten man” on which the entire pump operation resides.
Pump bearing failure almost always has wide-ranging downstream consequences beyond the cost of the bearing component itself. Unplanned downtime, an idle workforce, missed production goals, higher maintenance costs and, in extreme cases, grave safety concerns can all be the result of a single failed pump bearing.
Decades of engineering data suggest that nearly 80% of bearing failures are directly linked to lubrication issues. Extreme environmental challenges in pump system applications such as heavy contamination, vibration and varying loads make proper lubrication a necessity for long-lasting operation.
Lubrication Challenges
Pumps present challenges for bearing lubrication. Found in some of the toughest operating conditions, slurry pumps in mining operations, pumps in wastewater applications and chemical process pumps combine heavy particulate with moisture contamination and harsh chemicals, creating a perfect storm for pumps that have compromised seal integrity and inadequate or incompatible lubrication.
Traditional approaches to bearing lubrication rely on manual greasing according to time-based schedules. A repeatable, calendar-based “three shots of grease per inch of shaft” approach to preventative maintenance is merely adequate and can negatively impact operational uptime for several reasons:
- Workforce limitations: As experienced maintenance personnel continue to leave the workforce, the knowledge gap around proper lubrication grows. Over 70% of bearings in the U.S. are manually lubricated and maintained by a team that is increasingly younger, with less experience and less knowledge of mechanical maintenance best practices.
- Inconsistent application: Manual lubrication that follows a calendar-based schedule, rather than an automated system tailored to specific applications and operating conditions, can result in bearings being under-lubricated (accelerating wear) or over-lubricated (causing increased temperatures and possible seal damage).
- Contamination introduction: Each manual lubrication cycle represents an opportunity for contaminants to enter the bearing housing, particularly in harsh environments common to pump applications.
- Accessibility challenges: Pump bearings are often located behind guarding, in basements, across ponds and in other hard-to-reach locations that cannot be safely accessed while equipment is running, forcing a choice between timely lubrication and interrupted production.
Early attempts to address these issues introduced automatic, single-point lubricators—devices that dispensed lubricant according to a predetermined schedule. First-generation solutions proved unreliable. Inconsistent dispense rates due to ambient temperature variations and poor pressure generation resulted in an increase of bearing failures, rather than improving reliability, revealing a significant weakness: a failure to proactively communicate operational changes and respond accordingly.
The Evolution of Intelligent Lubrication
The latest advancement in bearing lubrication technology represents a paradigm shift from merely automated lubrication to truly intelligent lubrication. These systems combine precision electromechanical dispensing with connectivity capabilities that integrate with broader condition monitoring platforms.
Unlike their predecessors, modern intelligent lubrication systems offer several key advantages for pump system optimization:
- Consistent delivery regardless of environmental conditions: Electromechanical systems can provide reliable, consistent grease delivery in temperatures from -40 F to 140 F (-40 C to 60 C), unlike gas pressure systems, which are affected by ambient temperatures.
- Remote monitoring capabilities: Wireless connectivity allows maintenance teams to verify lubrication status remotely, reducing physical inspection requirements and limiting exposure to hazardous environments.
- Precise volume control: Digital control with regularly scheduled grease export means the bearing is regularly fed precise amounts of grease based on engineering-backed suggestions that account for environmental and application factors. Cloud-enabled, intelligent lubrication means a maintenance team can remotely purge grease, change grease release quantity and adjust the schedule from their phones or computers.
- Blockage detection: Advanced systems can detect when grease paths become blocked, alerting maintenance teams before bearing damage occurs.
- Integration with comprehensive condition monitoring: When lubrication data is combined with vibration and temperature monitoring, patterns emerge that provide early indications of developing problems.
Case Study: Slurry Pumps in Frac Sand Production
A recent installation at one of the largest frac sand producers in Texas demonstrates the impact of intelligent lubrication on pump system reliability. Producing over 3 million tons of frac sand per year and loading 15,000 tons per day, this facility uses centrifugal slurry pumps to move material throughout the production process.
Prior to implementing an intelligent lubrication solution, the facility employed a full-time staff member dedicated solely to the manual greasing of pump bearings. Despite best efforts, the employee could not keep up with the demand to protect the bearings from high levels of water and corrosive material ingress. The consequence was severe—slurry pumps were failing every two weeks due to contamination, costing approximately $120,000 in materials, labor and lost production per failure.
After evaluating the options, plant management chose an intelligent, automated lubrication system and installed 34 lubricator units on 11 critical pumps. These units were configured to deliver precise amounts of lubricant at optimized intervals, with connectivity to a condition monitoring platform that provided remote visibility into lubricator status and easy inventory management.
Since installation over a year ago, the facility has not experienced a single pump failure, an unmitigated success compared to the previous failure rate of two weeks. The financial impact was substantial, with documented annual savings of $1,731,440 in materials, unplanned downtime and labor costs. This success eliminated dedicated manual greasing efforts, improved on-site safety and prompted plans to expand the system to all pump bearings throughout the facility.
The Optimization Perspective
While the primary benefits of increased reliability, decreased downtime and increased on-site safety are self-evident and powerful, there are secondary benefits as well.
- Energy efficiency: Pumps are nearly always directly coupled to alternating current (AC) motors and are often part of a “fleet” of pumps. Properly lubricated bearings reduce friction, directly impacting the energy consumption of pumping systems. By minimizing the resistance motors must overcome, optimal lubrication contributes to overall system efficiency. For slurry pump applications where motors are often oversized to handle difficult starting conditions and variable loads, these efficiency gains translate to meaningful energy cost savings over time, particularly in operations with multiple pump installations running continuously.
- Extended component life: Optimal lubrication extends the practical lifetime of not just the bearings, but all related components such as seals, shafts and housings. In abrasive slurry applications, this significantly reduces the total cost of ownership for specific pumping equipment.
- Predictive maintenance enablement: Intelligent lubrication systems provide data that serves as a critical input to predictive maintenance strategies. When lubrication status is known with certainty, abnormal vibration or temperature readings become more meaningful, allowing for accurate prediction of developing issues.
As industrial operations continue to face challenges with reduced workforces, rising costs and heightened reliability expectations, intelligent lubrication represents not just an incremental improvement but a fundamental shift in how bearing health is managed in critical pump applications.
Looking ahead, it is likely there will be further integration between lubrication systems and broader industrial Internet of Things (IIoT) platforms, with artificial intelligence playing a key role in analyzing patterns across lubrication consumption, vibration characteristics and operational parameters to provide increasingly sophisticated predictive maintenance capabilities.