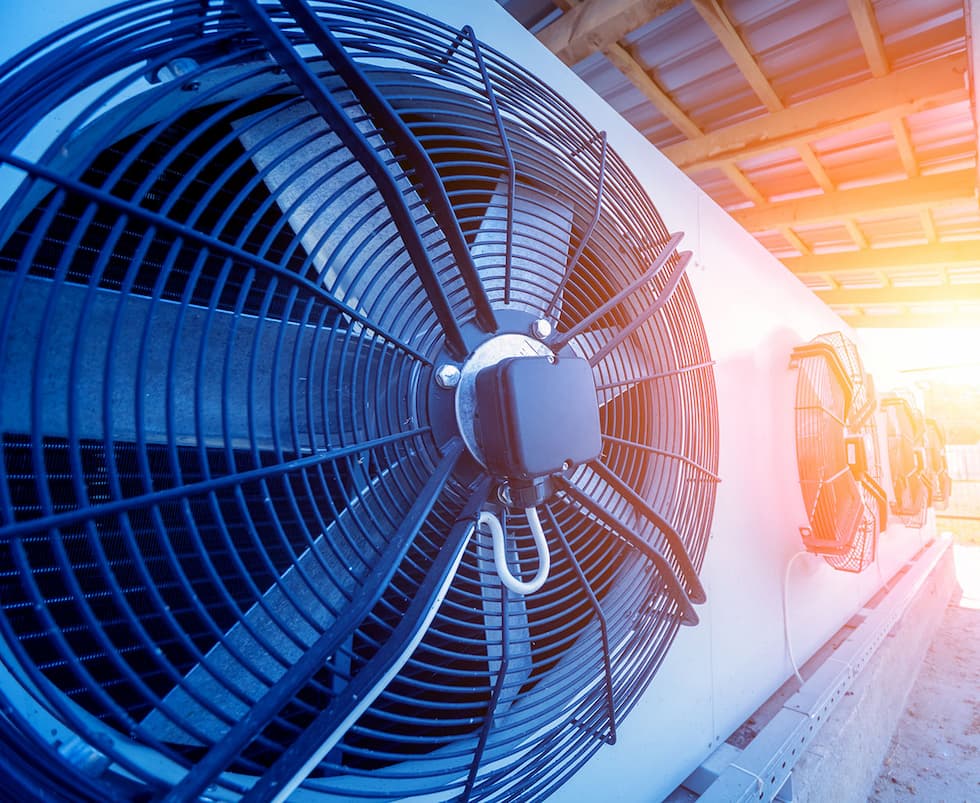
Sponsored Content
Modern heating, ventilation and air conditioning (HVAC) systems depend heavily on flow and energy measurement technology. Commercial and industrial facility owners seek to deploy advanced flow metering solutions, which enable them to achieve optimal levels of hydronic cooling and heating, even under the most challenging conditions. The reliability and efficiency of pumps in chilled/hot water systems can have a significant impact on building operating costs and performance.
Commercial and industrial businesses spend a large percentage of their building costs on creating cold and hot water and distributing it around their facility. It is not surprising there is an increased focus on determining the correct amount of this resource required to meet the needs of the business.
Building owners/operators navigating the uncertainties of the coronavirus pandemic are also focused on the role hydronic-based HVAC systems play in the comfort and safety of their facility. These systems are required to perform effectively and reliably on a 24/7 basis—regardless of fluctuating load demand due to changing occupancy levels.
A chilled water system acts as a centralized cooling system that provides cooling for an entire building or even multiple buildings. At the heart of the system, a chiller removes heat from water by means of a refrigeration cycle. The chilled water loop consists of pipes and centrifugal pumps that push the dense liquid through the chiller and into lines in various areas of the facility. Similar to a chilled water system, the heating system cycles boilers in and out of service and maintains proper temperature inside the hot water loop.
Pumps are also used to push condenser water to roof-top evaporators where it extracts heat from refrigerant. Unless this process is efficient and dependable, there is the potential for catastrophic failures in chiller systems.
Traditionally, buildings have employed constant flow loops that use a bypass to divert cold and hot water back to the conditioning source (chiller, cooling tower, boiler, hot water heater, etc.) when the end uses (air conditioning units, terminal heating units, process equipment, etc.) do not call for water.
Many building systems now pair variable speed drives (VSDs) with pumps to vary the chilled/hot water flow. This approach matches the water flow to the needs of the building without wasting energy or increasing the wear on equipment.
Why Flow Measurement Is Important
Experience has shown that pump assets are crucial to ensuring the correct amount of flow at the correct pressure so as to achieve optimal hydronic cooling and heating within large buildings and facilities. The flow rate of these pumps is typically determined by the maximum flow rate of the chiller or through the maximum flow rate required by the fan coils and air handling units (AHUs).
While it is common to measure differential pressure drop across pumps using pressure transmitters, this technique is prone to clogged impulse lines, diaphragm malfunctions and other potential failures. Flow meter technology provides a more precise and reliable solution and allows operators to detect ongoing erosion in pump efficiency.
Increasing chiller pump efficiency is certainly important, but equally important is the ability to measure the flow of the water throughout the system. If there is insufficient flow and pressure in a chilled water system, there will not be enough cooling, and the building may get hot during periods of high cooling load. If there is too much pressure and flow, then electrical components will be unnecessarily burdened. And, if there is no speed control, then electricity may be wasted due to excess pumping.
Boilers used for facility heating can also be tricky systems. Improper startup and shutdown can severely damage such systems. Again, flow measurement is integral to the process, providing information for the boiler startup and shutdown and verifying that water flow to the air handlers is correct.
In some cases, heating and cooling are required at the same time in an AHU. This calls for the use of flow meters to balance the demands on the entire system and reduce overall energy requirements.
Selecting the Right Flow Meter
When it comes to critical hydronic HVAC equipment, building operators cannot manage what is not measured, so it is important to have precise flow rate information. However, they want to obtain chilled/hot water system flow data in the most economical way possible without sacrificing accuracy.
Ultrasonic transit time flow meters have become a popular choice for HVAC-related applications in recent years. With this technology, ultrasonic waves transmit upstream and downstream through the pipe wall and the liquid flowing in the pipe. By measuring the difference in the travel time and knowing the pipe size, the meter determines the velocity and flow rate.
When an existing inline or insertion flow meter fails and is difficult to replace, or additional metering is needed, the best choice is a noninvasive solution like an ultrasonic clamp-on flow meter. Unlike inline meters with sensors or other components in the flow stream, this type of meter does not contact the dense, fast-moving internal liquid or accompanying debris—improving reliability and allowing for installation without shutting down the operation. Ultrasonic flow meters also eliminate problems related to pressure drop across the system.
Ultrasonic clamp-on flow meters provide other important advantages, such as low deployment cost, elimination of pressure head loss and no moving parts to maintain. The clamp-on design simplifies maintenance and troubleshooting activities throughout the life of the equipment.
How Ultrasonic Technology Is Evolving
As ultrasonic transit time flow meters have gained wider industry acceptance for measuring volumetric flow rates in clean liquids as well as liquids with small amounts of suspended solids or aeration, so, too, has the availability of these innovative devices increased across the global instrumentation market.
The current fluctuating occupancy level in many commercial and industrial facilities demands optimal HVAC system performance to maintain adequate heating and cooling. The days of using differential pressure sensors across chiller pumps to get an idea of the flow rate are largely over, due to the constant recalibration and inaccuracies this older technology requires.
Ensure a Successful Application
Building operators responsible for hydronic HVAC systems are faced with mapping out all the crucial metering points for water and energy usage, as well as measuring flow at both the design rate and minimum rate required for optimal equipment operation. This can easily be accomplished by using the current generation of noninvasive ultrasonic flow technologies.
An accurate flow measurement solution offers significant benefits to commercial and industrial facility managers concerned with the performance and costs associated with their chiller plant and heating system operations—particularly in the current pandemic environment.
Ultrasonic transit time clamp-on flow meters can verify that water is properly distributed through piping loops for the chilled and hot water sides of HVAC units, so that pumps can move water through the system in a way that ensures greater reliability and lower asset life cycle costs.