In my opinion, the system curve is the single most important component of the pump selection process. After all, the system curve determines the operating point on a pump’s performance curve. Other aspects, such as materials of construction and special features, can be reviewed after the hydraulic selection. The system curve is even more important when an application requires multiple pumps operating in parallel. Multiple pumps present a challenge to a system designer. If a system is designed for three pumps to operate at their best efficiency points (BEPs) when running in parallel, chances are that one or two pump operations will result in an operating point well to the right of BEP. If a three-pump system is designed for two pumps to run at BEP, the third pump will likely push all three to the left of BEP. As the number of pumps increase, it becomes even more difficult.
Wastewater Force Main
A good example is the wastewater force main. Seldom does any combination run at BEP. Fortunately, a combination of variable speed and across-the-line control can keep multiple clear water pumps at or near BEP. Unfortunately, this technique can be problematic with wastewater pumps because lower inlet velocities can lead to ragging at the vane entries. The Parallel Pump Performance Analyzer—which can be found under the “Pump Evaluation, Selection & Testing Tools” page at www.PumpEd101.com—is designed to evaluate both across-the-line and variable-frequency operation. It allows users to select a pump that will operate at BEP when several are running and view their operating points when all or fewer are running. It also shows the effect of variable frequency drive (VFD) operation with single and multiple pumps. It is designed for use with up to eight identical pumps. Figure 1 is a screen shot of the data entry tab. The required data include the number of pumps operating in parallel; the flow, head and hydraulic efficiency points for one pump; and the flows and heads necessary to generate a system curve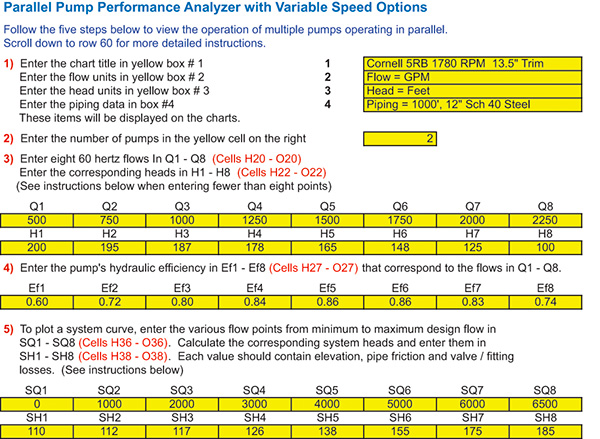
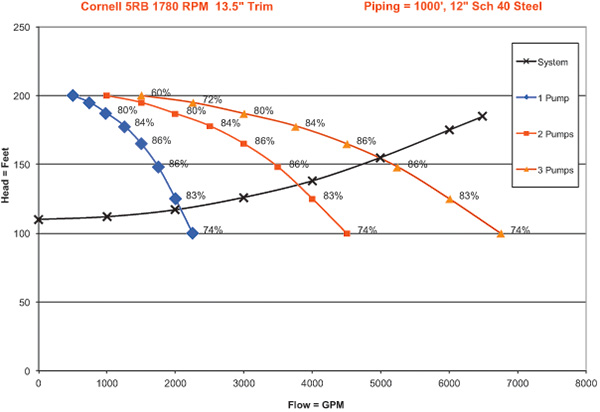
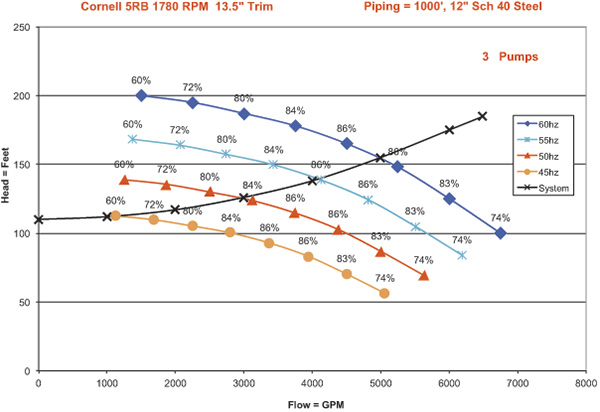
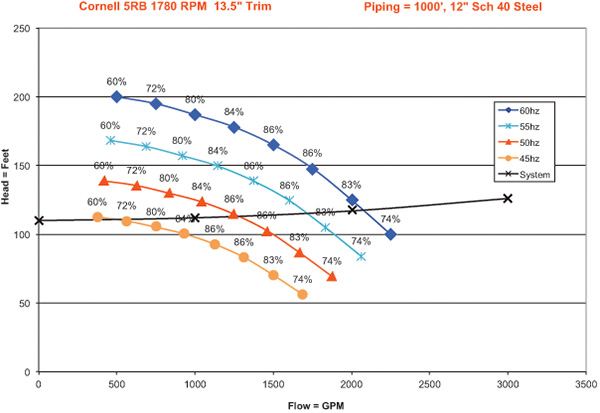