Editor's Note: This is the fifth in a series of five articles based on the Hydraulic Institute's new Positive Displacement (PD) Pumps: Fundamentals, Design and Applications e-Learning course. To read the previous article, click here.
Last month, we introduced Module 4 of the course, which focused on reciprocating pumps. In this issue, we will focus on metering pumps. Module 5 is fact-filled, basic training for people working with metering pumps. It takes a student from the clear points of what distinguishes a pump as a controlled volume metering pump to how these pumps were always more akin to instruments.
Metering Pump Market Overview
When Robert Sheen invented the metering pump in the 1930s, the core of his invention was a method of controlled volume that was inherent to the pump. The metering pump did not depend on a bypass valve after the discharge; speed changes to the pump by replacing belts, pulleys or motors; changes to the pump size to limit the amount of chemical dosed to a specific application of boiler feed or cooling tower chemicals; or the operator diluting the chemicals to match the pump's application rate. The means of controlled volume easily limited the pump's actual output while providing dependable accuracy and reducing performance monitoring and labor time in the chemical feed industry.
Since the original controlled volume pump, the terms metering pump, controlled volume metering pump and dosing pump have emerged as popular synonyms for this category. During the past 75 years, there have also probably been more inventions related to metering pumps than any other pump type. These inventions have typically related to producing a controlled limitation of flow rather than improving flow inducement. Electronics and robotics have most recently advanced controlled volume metering pumps. The level of the pump's self-contained flow management and automatic capacity correction will be further advanced in the decade ahead.
All of this innovation in the metering pump market is due to the many industries with needs for repeatedly sustainable accuracy in chemical dosing. In the various applications for metering pumps, process pressures can range from atmospheric pressure up to 50,000 psig (3500 Bar). Pump capacities per head vary from 10 milliliters per hour up to 5,000 gallons per hour. To meet this wide range of requirements, several types of metering pumps have evolved for each application. Figure 1 summarizes the various drives, control methods and liquid end combinations designed to handle the full scope of applications.
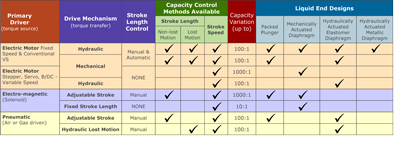
Accuracy on three levels has become the primary benefit of this type of pump in the delivery of additives to automated processes, as well as those with the simple mission of maintaining accurate constant flow. Different versions and forms of metering pumps have sustainable, accurate capacity control inherent to the pumps themselves, which is distinguishable from pumps installed with speed control motors and pumps in systems with control valves to divert or limit flow to the injection point.
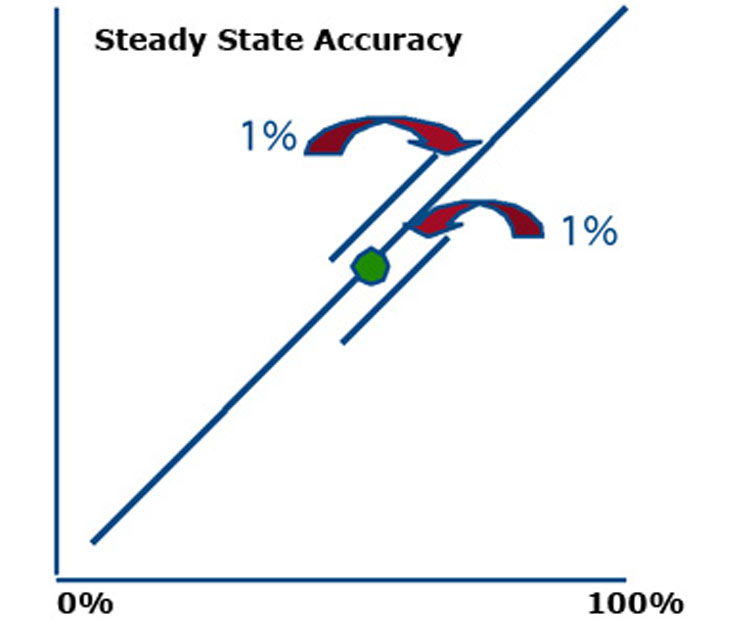
Metering Pump Drive Systems
Controlled volume pumps have never been greatly impacted by changes in system conditions, and the newest technologies in metering pumps automatically adjust to keep the output accurate to the set point, even when discharge pressure changes. At the same time, recent innovations have made it easier for the operator to set metering pumps to the desired discharge rate with minimum or no need to calculate between capacity change due to stroke length setting versus capacity.
Many controlled volume pumps today incorporate both stroke length and stroke frequency/speed in order to provide the user with up to 100 to 1 capacity variation. Today's electronics enable wider speed variation and extreme accuracy, eliminate the need to vary the stroke length and avoid the hydraulic difficulties inherent to running pumps at less than full stroke length.
The first controlled volume metering pumps incorporated an electric motor with a belt and pulley drive. The drive types commonly used today include standard AC motors. Solenoid drive systems are probably the most popular today due to competitive pricing. AC and DC variable speed motors are used in conjunction with stroke length control in some types. Pneumatic and hydraulic power sources are found in specialty applications like natural gas and agriculture. Advanced electric motors, taken from the robotic and computer industry (i.e., stepper motors), have recently eliminated the need for stroke length control, simplifying setup and operation.
In the original metering pump, capacity was changed by adjusting the stroke length of the piston, which was located on the outside of the pump. Figure 3 is essentially the same concept, but represents a technology introduced about 30 years after the first metering pump. In this concept, the stroke length adjustment function was moved to an internal, oil bathed gear system. This drive type is readily available today.
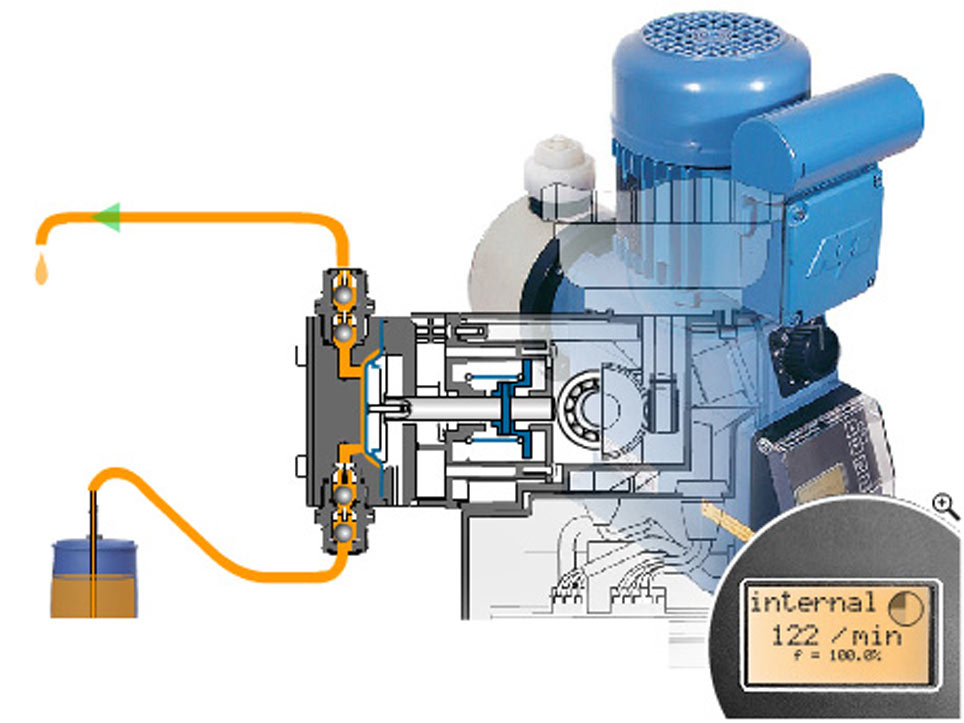
The choice of drive system is important to the application as it relates to durability, accuracy, automation levels, maintenance availability and cost. From the simplest timed triggering of a solenoid to electric motor driven drives as depicted above, all incorporate some capacity change. While speed was initially a secondary control method introduced to extend the turndown ratios from the 2 to 1 or 3 to 1 limits and up to 10 to 1, speed was immediately seen as a preferred capacity control in some applications. Speed brought problems for relative accuracy.
The Value of a Metering Pump
Within the applications best served by dosing or metering pumps, economics should be considered to select the best value for a particular application. Unlike most other pumps, cost of ownership or life cycle cost of dosing pumps is usually not heavily influenced by power consumption and repair costs. A more likely case can often be made for savings in the cost of chemicals metered due to high level accuracy or the quality of a final product.
Users choosing metering pumps are often attracted to the simple convenience of a pump with a compact package and a built-in capacity adjustment. Factors such as steady state accuracy (see Figure 2), repeatability and linearity represent even greater value in the majority of applications where dosing pumps are found today. Today's controlled volume pump accuracy can dispense the desired amount of liquid during extended periods of time, even as the process requires the pump's discharge rate to be changed. The capacity ranges as much as 1,000 to 1 in some styles of these pumps.
While convenience of flow rate adjustment can cause an engineer to initially consider variable capacity pump systems, the value diminishes quickly if the operator cannot depend on the pump repeatedly metering the same or planned variance of chemicals at the predetermined settings necessary to the process. The costs of compensating for variable capacity pumping systems that have low accuracy rates can be extremely high in the form of extra components in the system or poor quality results in the process (see Figure 4).

Conclusion
Matching the right liquid end to the right drive mechanism is how this class of pumps provides operators with precise delivery of liquids. The metering pump has evolved from the original packed plunger heads to diaphragm liquid ends that incorporate sensors as a means of monitoring operation and accuracy.
Pumps & Systems, June 2009