The diaphragm pumps at the Maple Lodge Sewage Treatment Works in the UK required maintenance that was time-consuming and expensive.
05/24/2016
Thames Water is the United Kingdom's largest water and sewerage company, supplying nearly 9 million people with drinking water and providing wastewater services to 15 million customers. The utility's service area covers 5,000 square miles across London and the Thames Valley. On an average day, Thames Water treats more than 4 billion liters of wastewater, or about 1.06 billion gallons. The Maple Lodge Sewage Treatment Works in Maple Cross, Hertfordshire, near Rickmansworth northwest of London, serves nearly 500,000 residents and businesses and receives up to 300,000 cubic meters of wastewater per day. At maximum capacity, the plant can generate enough renewable energy to power the equivalent of 9,000 homes.
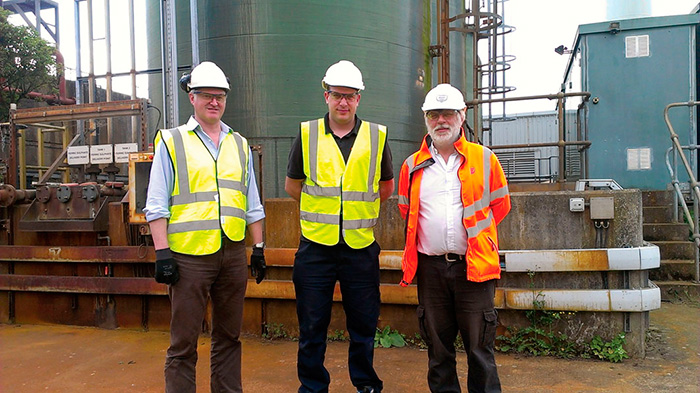
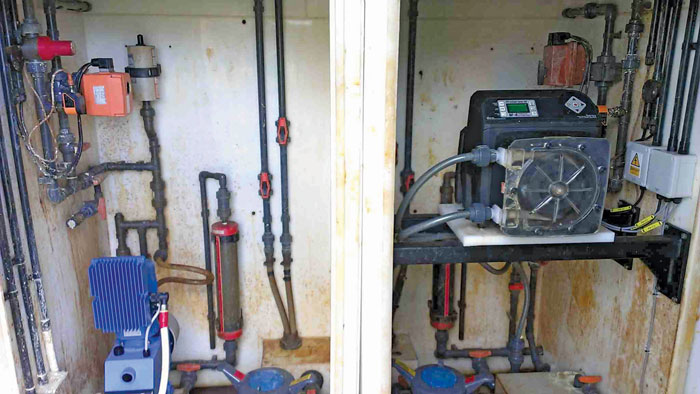