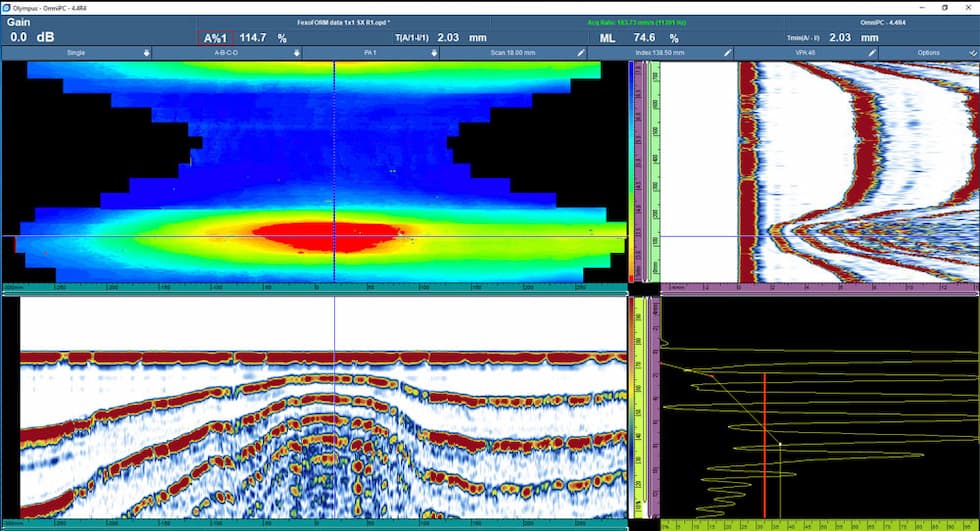
In refineries and chemical production facilities, routine inspection of extensive process piping networks is a necessary part of plant maintenance. Many of these pipelines transport abrasive and corrosive liquids, making them highly susceptible to material thinning. However, even conduits for water and steam are vulnerable to internal wear.
Flow-Accelerated Corrosion vs. Erosion Corrosion
Flow-accelerated corrosion (FAC) occurs in metal pipes (usually carbon steel) that transport flowing water. The flow wears away or dissolves the oxide layer on the inside and the metal underneath oxidizes again once exposed. A cycle of dissolution and oxidation occurs, corroding the inside of the pipe at a rate dependent on the flow velocity.
Erosion is pipe wall thinning exacerbated by the stress produced by corrosive and/or abrasive liquid flowing in the pipe at a high velocity. Mechanical wear is usually more severe in points where the flow intensifies, such as a curve or elbow.
Efficient Inspection Method for In-Service Processing Pipes
The sheer number of pipes to be tested means that inspectors require a method that optimizes the time and costs of FAC and erosion preventive maintenance. With respect to cost and time, nondestructive testing (NDT) methods that enable the inspector to verify the piping while in service are the best options. That said, with radiology testing (RT), if done on-site, the area needs to be evacuated to limit personnel’s exposure to radiation. Additionally, if the part needs to be sent to the bunker, the pipe must be emptied, removed and sent off-site, resulting in expensive downtime.
Conventional single-element ultrasonic testing (UT) is considered too slow and inefficient, mainly because of the limited coverage. However, phased array UT, which uses multielement probes, has the potential to save time. What complicates things are the complex geometries involved, such as pipe elbows. Process piping networks feature numerous elbows that make standard large, rigid phased array (PA) probes ineffective and inefficient for this application. Unable to adapt to the changes in surface shape, these rigid probes cannot be used to inspect the concave on the intrados or the convex on the extrados of the pipe elbow. They are also limited to a specific pipe diameter, so they cannot cover the wide range of pipe diameters that need to be inspected.
An inspector using a rigid PA probe to inspect pipes is forced to revert to the conventional UT technique and manually spot check each pipe elbow with a small-footprint transducer. This is a long process that entails drawing a grid on the elbow and verifying it box by box (Image 1). As well as being slow and tedious, this conventional UT method precludes inspectors from all the advantages that phased array technology offers.
Advantages of PA Technology for Pipe Elbow Inspection
PA technology has been used in the last decade for corrosion inspection on pipelines and process piping. It offers such advantages as high-resolution data and quality imaging and coverage. Inspectors using PA often experience an improvement in productivity since analyzing the results is relatively easy. High-quality imaging, including color-coded C-scans, helps minimize the impact of operator skill on the results and increases the probability of detection (POD).
To resolve the inherent issues of pipe elbow inspection, a flexible ultrasonic phased array probe and scanner for pipe elbows can be used (Image 2). Using a flexible probe and scanner solution can provide high-resolution thickness mapping of the entire pipe elbow, making it easier for inspectors to make an accurate diagnosis.
With the precise information provided by the phased array mapping data, inspectors can evaluate the pipe elbow’s remaining operational life and determine the repair or maintenance requirements. Such a phased array solution is comprised of three components: a flexible phased array probe (for a wide range of pipe diameters), local-immersion water wedges, and a scanner that provides stability and positioning information in relation to the part’s surface.
Flexible PA Scanner Performance on Cladded Pipe Elbow
Using the flexible scanner, a complete scan of a cladded pipe elbow can be completed on-site in a short time. The inspector can perform the pipe elbow scan while the line is still in operation, reducing downtime and operational costs. It also mitigates the safety issues related to removing the elbow from the processing line and sending it to the radiography bunker.
Example 1: Cladded pipe elbow
A test performed to cover 100% of a 16-inch outside diameter (OD) (406.4-millimeter [mm]), 23-mm thick carbon steel pipe elbow specimen with an internal layer of welded nickel cladding was completed in 35 minutes, including preparation time.
A second test was performed on a sample that was taken out of production (Image 3) to demonstrate the clarity and precision of the results. Cutting the section in half lengthwise enabled a view of the cladding weld passes as well as the corrosion pitting occurring at a junction between two weld patterns.
The resolution provided by the phased array probe and scanner was 1 by 2 mm, with a beam aperture of four elements.
The C-scan and B-scan displays on the data acquisition instrument show how the high-resolution imaging provided by phased array technology can make interpreting and diagnosing easy for inspectors (Image 4).
The pitting corrosion and lack of fusion of the cladding are easier to identify. The junction where weld cladding passes meet can be flagged as susceptible to pitting, especially when there is a lack of fusion between the cladding and the base material. This knowledge enables the inspector to better estimate the remaining life of the pipe elbow and optimize the inspection schedule.
Example 2: Carbon steel pipe elbow
Another test was conducted on an 8.625-inch OD (219-mm), 7-mm thick, carbon steel pipe elbow. With a resolution of 1 by 1 mm using a beam aperture of three elements, the flexible phased array solution took only four minutes to scan the entire elbow.
Though the time savings are significant, the other advantage of PA is imaging. The scan results show severe wall loss. The different views (C-, B-, D- and A-scans) display the location of the erosion and its progression. The minimum measured thickness is close to 2 mm, which demonstrates the near-surface resolution that can be achieved (Image 5).
Advantages of Flexible PA Scanners
Using a flexible PA scanner, processing pipe inspectors can perform high-resolution thickness mapping of pipe elbows and save time while doing it. The imaging capabilities provided by PA help inspectors check cladded pipe for corrosion pitting and delamination on-site without needing to take the pipe out of service.
The solution enables diagnosis of wall thinning caused by FAC or erosion. It is also flexible in terms of adapting to a broader range of pipe diameters, as its design includes a series of local-immersion water wedges that the user selects to fit the pipe diameter. This solution is cost-effective and can help inspectors make improvements in productivity.