Last of Two Parts
03/14/2016
Part 1 of this series (Pumps & Systems, February 2016, read it here) examined the process elements of a piping system, as well as the flow rate, prior to troubleshooting the cause of pump cavitation. This column will use the piping system's data previously discussed and determine the cavitation's cause and other challenges within the system. In the example system (see Figure 1), results show that the differential pressure across the pump is only 63 pounds per square inch (psi), far less than the 69.2 psi in the validated results. The difference can be attributed to pump cavitation. The reduction in discharge pressure caused the level control valve to open farther to maintain the desired level in pressure vessel PX-PV-122.
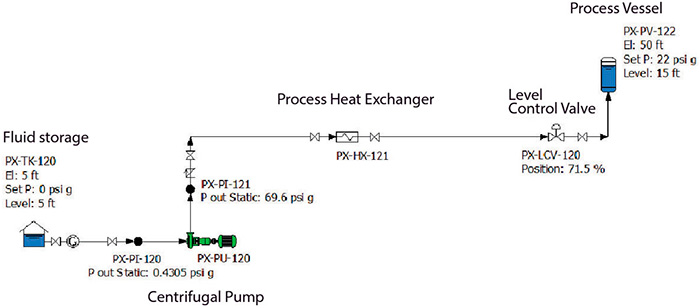

See more Pump System Improvement articles by Ray Hardee here.