01/22/2014
This article is part of our ongoing series on the history of pumps.
In 2008, I wrote a two-part article on waterhammer and how it can damage pumps and piping systems. It is the result of a change in flow momentum and is often caused by the quick closing of a downstream valve. The resulting shock wave can cause significant damage to the system. In one application, however, waterhammer is a positive event. In this application, a quickly closing valve allows waterhammer to supply the energy required to pump water.
The hydraulic ram was invented in 1796 by Joseph Montgolfier, co-inventor of the hot air balloon, and was awarded a British patent in 1816. By the 1820s, it was in widespread use in Europe and the U.S. During that period, it was considered one of the most significant inventions in the history of civilization.
Rams have been designed to pump more than 50,000 gallons per day (gpd) and produce discharge heads of 300 feet and higher. Typical rams available today range from 700 to 1,800 gpd for a 1-inch model to 1,000 to 10,000 gpd for a 3-inch model. Much larger models are also available. For end users who appreciate simplicity, the hydraulic ram is an eloquent machine, and its design has changed little since its invention. It uses the low pressure provided by a short length of downhill pipe and converts it to a much higher delivery pressure.
Figure 1 is a drawing of the original machine. Its operation is extremely simple. Water enters the ram from the inlet or drive pipe, flows through it and discharges through the upturned end on the left. Inside the horizontal body of the ram is an iron ball. The flowing water accelerates the iron ball which, in turn, moves with increasing velocity toward the discharge. Since the ball is too large to exit the discharge, it seats itself and acts as a quick closing valve. This produces a waterhammer effect that sends a high-pressure shock wave back toward the inlet. A portion of this high-pressure water enters the air chamber through a check valve and then makes its way into the discharge pipe.
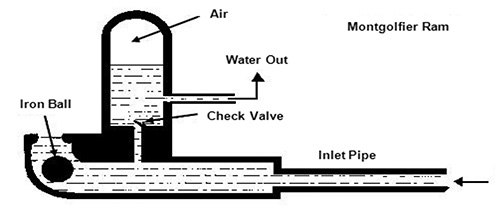
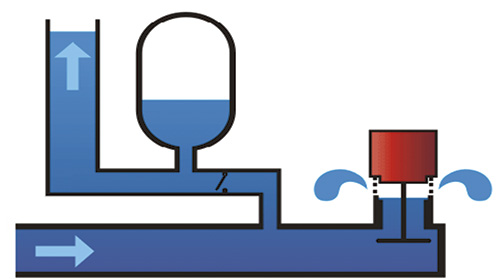