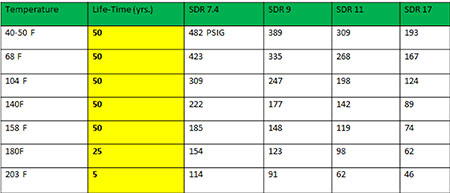
There is a piping material gaining traction in the plumbing and HVAC world. It does not rust, corrode, scale or pit, and it allows pumps to run at their optimum design criteria for the life of the piping system. The material: polypropylene random copolymer for enhanced crystallinity and temperature capability (PP-RCT).
PP-RCT is a corrosion resistant alternative to metallics that can handle more than 100 pounds per square inch gauge (psig) at 180 F, with no degradation in system performance. The life expectancy for various operating conditions can be 50 years with “like new” performance.
This material has been used in these services for decades in Europe, and in the United States for about 15 years. The basic material properties are shown in Image 1.
Here are some advantages that PP-RCT piping systems offer.
Weight
- Steel pipe is approximately 3.5 times heavier than PP-RCT pipe (pounds/feet).
- Large and complex PP-RCT spools can be prefabricated to minimize field welds, yet still be manageable to install in utility rooms.
- PP-RCT is safer and more economical (less manpower required) to install.
Joining Technology
- Requires no welding rod, open flames or solvent cements to join.
- Creates a homogenous joint: welds are as strong or stronger than the pipe itself.
- Welding time is reduced.
- No noxious fumes are created by the welding process, making it ideal for enclosed spaces or buildings that will be applying for Leadership in Energy and Environmental Design (LEED) certification.
Corrosion Resistance
PP-RCT has a high corrosion resistance—systems have a design life of up to 50 years with no corrosion. Corroding metal pipes can introduce particles in the water system, adversely affecting all other system components such as pumps, valves, coils, control components, etc.
Flow Capacity
PP-RCT pipe has a higher Hazen-Williams flow coefficient than new steel pipe. As steel pipe scales and corrodes over time, this gap is increased further.
Insulation
PP-RCT is a naturally insulating material, while metallic pipes are naturally conductive.
In certain applications, the insulation value provided by the pipe wall alone may prove sufficient to avoid condensation or retain the desired water temperature.
Expansion Control
PP-RCT pipes are co-extruded with a fiberglass middle layer that reduces expansion and contraction by
75 percent, making them less susceptible to snaking in installations with high temperature gradients.
Because corrosion affects the internal surface characteristics of carbon steel pipe, and that affects flow and pressure loss, this can influence the pump selection process.
When looking at carbon steel pipe for a hydronics application, it is important to consider the appropriate Hazen-Williams (H-W) coefficient of friction when selecting a system’s pumps. PP-RCT’s H-W factor is 150. That number reflects a smooth surface, and it does not change over time.
Carbon steel flow charts listing particular velocities and pressure (head) loss data for various pipe sizes are based on a certain H-W factor. This factor, for steel and many other kinds of pipe materials, varies over time due to the effects of internal corrosion.
Some charts that refer to new steel have performance data based on an H-W factor of 140. The danger is if the system design criterion is based on new steel data with no consideration for the aging of the steel.
Aging is the pitting, rusting and scaling of the interior pipe surface. In other words, how does corrosion affect the pipe’s ability to provide adequate flow, once a pump has been selected?
Old steel can have an H-W factor of anywhere between 90 and 110, which can have a considerable effect on system pumping performance. The challenge is to determine what the definition of old is, and hope that the system does not get older than for what it was designed.
Some sources define old pipe as 15 years, and list a corresponding H-W of 100 to 110. Other sources may state 20 years and show a factor of 90. Aging of pipes is dependent upon operating pressure and temperature, water chemistry, fluid make-up (water and glycol solutions, for example) and chemical treatment of the system (or lack thereof). Any of these can combine to affect the piping much more quickly than anticipated.
All steel pipe systems will age, and it can be difficult to determine for what age (H-W factor) the system should be designed.
As an example of this selection process, this system has the following requirements:
- flow rate: 500 gallons per minute (gpm)
- pipe size: 6 inch
- point-of-use pressure required: 65 psig (150 feet of head pressure)
- length of pipe: 700 feet
- 90-degree elbows: quantity of 20 (16 equivalent feet/fitting) = 320 feet
- elevation: 50 feet
- total equivalent length of pipe: 1,070 feet
.jpg)
Plot 4 variations of pipe material on a typical pump curve. The variations will include:
- PP-RCT (H-W = 150) with a head loss of 2.4 feet/100 feet
- new steel (H-W = 140) with a head loss of 1.66 feet/100 feet
- old steel (H-W = 100) with a head loss of 3.16 feet/100 feet
- old steel (H-W = 90) with a head loss of 3.88 feet/100 feet
These characteristics result in the following total dynamic head (TDH) for each material:
- PP-RCT: 176 feet
- new steel: 168 feet
- old steel (H-W = 100): 184 feet
- old steel (H-W = 90): 192 feet
All four of these TDHs are plotted on Pump Curve A, along with the vertical line depicting 500 gpm.
Note that 500 gpm plots the pumps at their maximum efficiency.
Upon closer inspection, the data spans two pump sizes.
Here is how this plays out.
On Curve A1, a new steel and PP-RCT is plotted. The new steel plot is below the curve corresponding to a 2-stage (1 reduced stage) pump, so that would be the pump selected for this application.
PP-RCT, however, is above that line, so the next larger pump would be chosen. That would be a 2-stage (two full stages) pump.
Based on the hp/stage portion of the curve, the new steel pump would have:
- 1 full-stage horsepower (hp): 16
- 1 reduced-stage hp: 12
- total hp required: 28
For PP-RCT:
- 2 full stages: 32
- total hp: 32
That would be a 12.5 percent savings in hp. Relating hp to electrical power more than 1,000 hours of operation:
New steel energy savings
- 1 hp = 0.75 kw/hr
- electricity cost (national average): $0.13/kw/hr
- savings based on 4-hp reduction: $390/1,000 hours
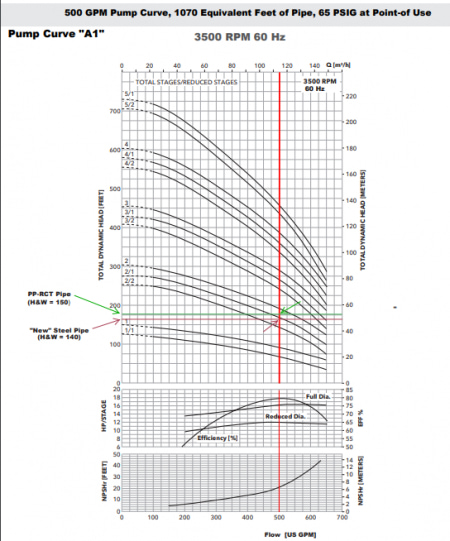
However, users now have to take into consideration aging—or the change in H-W factor—for old steel due to corrosion. Take a look at Curve A2.
Here, the two old steel plots are isolated. Old steel at an H-W of 100, although above the PP-RCT plot, would still indicate the same pump selection as PP-RCT.
That is, a 2 full-stage hp pump with an hp rating of 32. So here, there would be no difference in initial performance between steel pipe and PP-RCT pipe. Note that the new steel pump will no longer suffice, and the aging of the steel has commanded a larger pump.
But what about old steel at an H-W of 90?
Well, a look at that plot indicates that the next larger size pump would be required. This is a 3-stage pump, with one full stage and two reduced stages.
This would be calculated as:
- 1 full-stage hp: 16
- 2 reduced-stage hp: (2 x 12) = 24
- total hp: 40
To accommodate the corrosion of the steel pipe, a larger hp pump must be selected. This is 25 percent larger than the pump required for PP-RCT piping—and almost 43 percent larger than a new steel pump.
The resulting increase in energy costs is:
PP-RCT Energy Savings
- 1 hp = 0.75 kw/hr
- electricity cost (national average): $0.13/kw/hr
- savings based on 8-hp reduction: $780/1,000 hours
What if the pump had been selected for new steel? How would aging of steel piping affect the system performance? Look at Curve A3. As the pipe corrodes, the pump’s performance will follow the pump curve, running along the line to the left. Look at how the pump would operate by looking at where the two old steel plots intersect the 2/1 pump curve (new steel pump).
By following those intersections to the efficiency curve, the efficiency would decline to 73 percent as the steel ages.
Note that the PP-RCT piping system will always run at this 80 percent efficiency level, since there is no corrosion, and therefore, no aging of the pipe to consider.
In tandem with this loss of efficiency, the steel system would be providing a reduced flow rate dropping to 460 gpm as internal corrosion takes effect. Again, a PP-RCT system will provide 500 gpm for its operational life without any losses.
These are the questions to now ask, knowing how corrosion affects a pump system with steel pipe:
- Do I really know how to judge the age of my steel pipe system?
- Can I really calculate how long it will take the system to reach a reduced H-W factor?
- What is that factor?
- Do I select pumps based on an H-W of 90?
Being conservative, and doing as question No. 4 implies, it is now shown how this drives selection to a larger pump.
With PP-RCT, the friction factor is constant at 150. A cost effective and energy efficient pump can be selected and should perform like new for the life of the system.