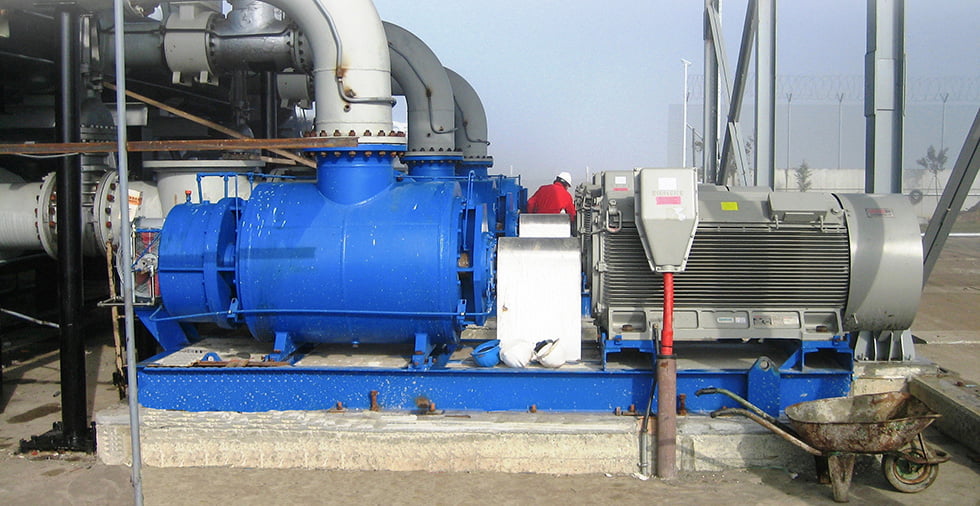
Part I of this article, in the October 2019 issue of Pumps & Systems, described cautions, reviews and inspections for three main components (piping and valves; foundation, alignment and rotation; and lubrication) that should be conducted before startup to ensure the issues that can arise with pumping systems are identified and eliminated. What follows is Part II, which reviews additional information on how to prevent delays and ensure the successful startup of rotary pumps.
Startup Spares Prevent Delays
With care and planning, startups will generally go smoothly. But, it is prudent to have key spare parts in case they are needed quickly after some unanticipated problem, minor damage or need to disassemble equipment.
For rotary pumps, this would be a set of shaft seals, gaskets, O-rings and bearings, frequently available as a minor repair kit.
For other rotating equipment, spare bearings, grease and oil seals and gaskets should be on hand to avoid delay in startup. More extensive spares will depend on availability from the vendor, criticality of pump operation, plant practice and perhaps other issues specific to the installation. If the startup goes well and the spares are not used, it keep them on hand for future service.
Additional Resources
Be sure electric power, steam, cooling water, hot oil, instrumentation power or air, or any other auxiliary resources are ready before start. The same for having adequate pressure and temperature gauges for observations during startup.
A method of speed indication such as a tachometer is recommended if the drive is not a fixed speed one. If the pump will handle hot liquid, preheat the pump so it is not exposed to thermal shock when the hot liquid reaches an ambient temperature pump. Rotary pumps may be more sensitive to thermal shock due to the close running clearances.
The recommended warm up rate is 2 F to 4 F (1.1 C to 2.2 C) per minute. During the warmup, confirm the temperature differential between the top and bottom of the pump is less than 17 C or 30 F. Allow the pump to stabilize for two hours at the process fluid temperature.
Last Minute
It is good practice to fill as much of the inlet piping system as possible with the liquid to be pumped using the procedure provided by the manufacturer. This will assist in priming and will reduce the risk of pump damage during an otherwise dry start. A rotary pump will prime quicker if internal pumping elements are at least wetted. Priming is nothing more than pumping air from the inlet system to the discharge system. The ability of a rotary positive displacement (PD) pump to act as an air compressor is related to having some liquid present internally.
Pump shaft seals should never operate dry. Premature or immediate seal failure is the inevitable result. Hand rotating the pump a few times after priming helps ensure that liquid is present at the shaft sealing mechanism. It also allows a final check for rubs/binding.
If the pump has a seal chamber access plug, remove it, fill the chamber with liquid and reinstall the plug.
Have phone numbers of key vendor service departments on hand, along with fire and medical emergency service. When handling flammable liquids, both pollution and fire hazards are present.
Have an adequate supply of liquid in the pump inlet system. Confirm where pump discharge flow will be going to be sure the discharge system is ready.
Before final startup, ensure valves are open or closed as required. Pump inlet and discharge valves are normally left fully open. Manual pump bypass valves are also normally left open on startup. An air bleed valve in the discharge piping at a high point near the pump will significantly improve the pump’s ability to self prime. The valve is open during startup until liquid flows. Know where this flow is directed to avoid inadvertent discharge to atmosphere or spillage.
Loud or erratic noise at startup is an indication of inadequate pump inlet pressure (cavitation), or air being drawn into the pump inlet system. This is frequently accompanied by increases in or excessive vibration. If mild, troubleshoot. If severe, shut down the pump and find the problem.
Conclusion
Remember, each system has unique features and requirements, some of which may interact with each other or with other aspects of plant operation.
Be sure to thoroughly review the technical manuals, drawings and instructions from the pump and all other equipment to learn their specific requirements. While this is the easiest step, it is most commonly overlooked.