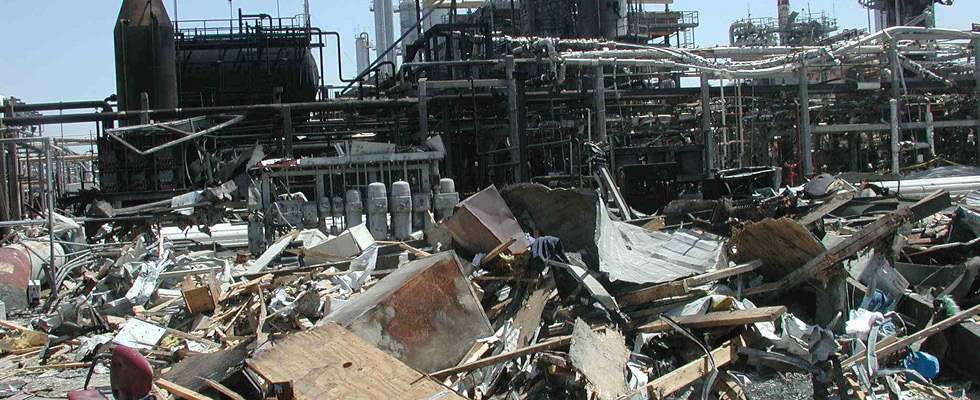
On March 23, 2005, the BP Texas City Refinery experienced one of the most devastating industrial accidents in U.S. history. The explosion claimed the lives of 15 workers, injured more than 180 others and caused significant facility damage. This event continues to serve as a somber reminder of the importance of operational safety and equipment reliability.
The incident occurred during the startup of the raffinate splitter tower in the isomerization unit. Due to a combination of instrumentation issues and procedural oversights, the tower was unintentionally overfilled with liquid hydrocarbons. As the liquid expanded, it was routed to a blowdown drum and stack system—an outdated configuration that had not been phased out. The release of flammable vapor into the atmosphere was subsequently ignited by a nearby idling vehicle, leading to the catastrophic explosion.
The explosion destroyed the blowdown drum and stack, sending a powerful shock wave across the refinery. Nearby trailers housing workers were directly impacted, contributing to the high fatality count. Many of the injured sustained serious burns and trauma. Emergency response was further hindered by poor site planning and limited access to critical shutoff valves. The long-term effects on worker families, the community and the industry’s public trust were substantial.
Investigations into the disaster highlighted a range of contributing factors, including organizational and safety culture shortcomings, equipment age and maintenance challenges. From a sealing technology standpoint, additional attention must be given to the role of gaskets and flange joint integrity in environments exposed to temperature cycling and mechanical stress.
According to findings from the U.S. Chemical Safety Board (CSB), some gaskets within the system had deteriorated due to prolonged exposure to extreme conditions. Over time, such exposure can lead to gasket relaxation, creep or extrusion—each of which can reduce the sealing effectiveness and potentially lead to vapor leakage.
Technologies like flange springs, which help maintain consistent gasket stress by compensating for bolt relaxation and thermal changes, could provide an additional safeguard in high-risk environments. While not a guaranteed solution to prevent such incidents, they represent a proactive step in creating more resilient sealing systems. Proper use of flange springs, when combined with appropriate gasket selection, enhances joint integrity and reliability.
The proximity of temporary office trailers to hazardous process areas and the presence of ignition sources further compounded the severity of the event. These issues, when combined with mechanical vulnerabilities, underscored the multifaceted nature of industrial risk.
From a sealing perspective, the Texas City incident emphasizes several critical best practices:
- Understand the application: Gasket material selection should be grounded in actual process conditions, not generalized specifications.
- Implement flange management programs: Regular inspection of bolt loads, gasket condition and joint integrity is vital.
- Ensure proper training and documentation: Flange assembly should follow defined procedures, and personnel should be properly trained.
- Consider engineering redundancies: Additional safety features, such as flange springs or backup containment, should be considered.
The Fluid Sealing Association is dedicated to helping facilities improve safety, reliability and compliance through the proper use of sealing devices. For more information, please visit fluidsealing.com. Together, we can take steps to ensure that tragedies like Texas City remain part of our past—not our future.
We invite your suggestions for article topics as well as questions on sealing issues so we can better respond to the needs of the industry. Please direct your suggestions and questions to sealingsensequestions@fluidsealing.com.
For more Sealing Sense articles, visit pumpsandsystems.com/tags/sealing-sense.