The wastewater treatment process requires precise and efficient dosing of a variety of harsh and corrosive chemicals. Diaphragm and peristaltic metering pumps are typically the go-to technologies for this type of application. However, for one water reclamation plant in Cape Coral, Florida, progressive cavity pumps (PCPs) were selected for their precision, efficiency and reliability of its sodium hypochlorite dosing system.
The Challenge
The city of Cape Coral has been recognized as having one of the largest municipal residential irrigation demands in the country. From October 2017 through September 2018, the Florida Annual Reuse Report cited that the city used an average of 27 million gallons of water for irrigation each day, with a maximum daily flow of 44 million gallons per day.
To reduce irrigation’s impact on one of the city’s main sources of drinking water—the mid-Hawthorn Aquifer—the city of Cape Coral has two wastewater facilities that reclaim and reuse treated wastewater for irrigation: Everest Water Reclamation Facility and Southwest Water Reclamation Facility (SWRF). The city also has more than 300 wastewater pump lift stations and numerous freshwater canal pump stations to supplement the irrigation system.
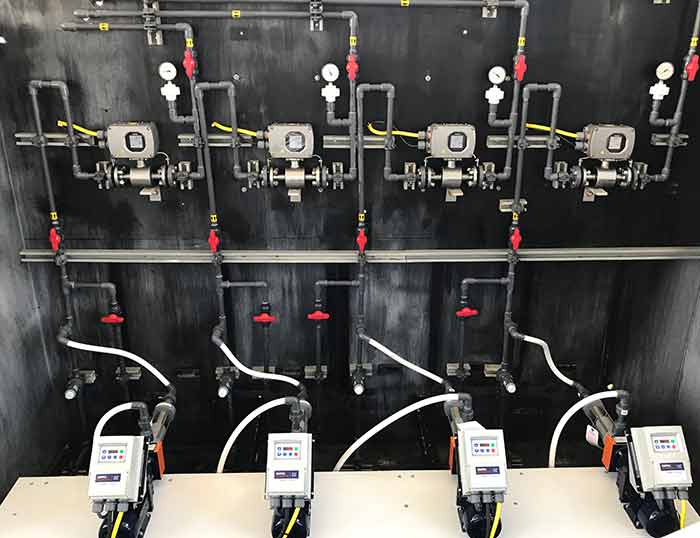
SWRF, which employs about 20 people, pumps an average of about 7 million gallons per day (mgd), with a max of 15 mgd. For many plants in southwest Florida—which experiences extreme heat and humidity for much of the year—algae buildup is a more severe problem than in other geographical regions. Until early 2017, SWRF used motor-driven mechanical diaphragm pumps to dose sodium hypochlorite, which is used to curb the growth of algae and other pathogens in the 110-foot secondary clarifiers and in its automatic backwash filters.
While the diaphragm metering pumps were effective at dosing sodium hypochlorite, they required frequent maintenance, sometimes as often as once a week.
Because the pumps used backflow preventers, pressure regulators, check valves and other fittings, they often experienced leakage and crystallization of the bleach.
The leaks caused damage to the pumps and fittings, and crystallization led to interrupted flow and energy losses. Because of the harsh and corrosive properties of sodium hypochlorite, the weekly maintenance requirements were also posing safety concerns for personnel. “There was a constant battle trying to keep them running,” SWRF maintenance supervisor Joe Holowell said.
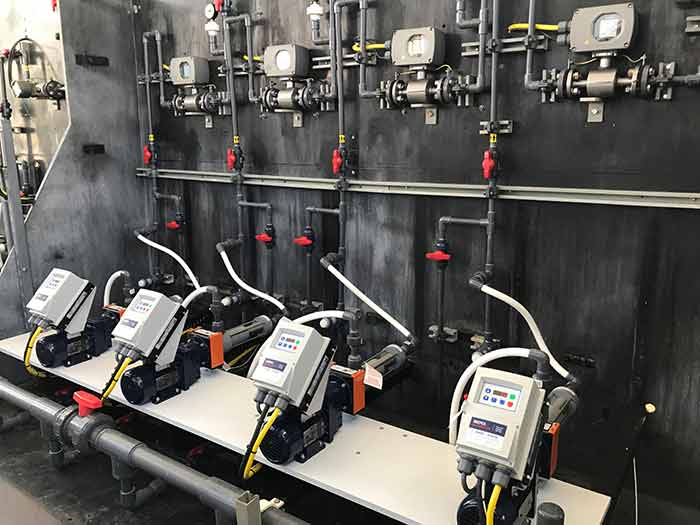
The Solution
Desiring to minimize the maintenance requirements of its chemical metering pumps, the plant turned to a different technology. It was looking for something that would provide laminar flow with low cost of ownership and improved safety. The solution came in the form of PCP technology.
The two most common types of chemical metering pumps are diaphragm metering and hose pumps. PCPs offer an accurate, laminar, repeatable flow without the ancillary equipment required by some equipment. A PCP’s nonpulsating flow leads to tighter control of the process, with PCPs feeding real-time chemistry to meet the requirements. They do not require suction side check valves, pulsation dampening, or back-pressure, antisiphon or degassing valves. With fewer parts, PCPs have a lower risk of leakage, crystallization and other obstructions.
PCPs also avoid vapor locking. They pass the vapor phase of the sodium hypochlorite and other products with the tendency to off-gas, which can interrupt the chemical feed to the process.
SWRF installed its first PCP in early 2017 and has since installed three more, with two spares available as backup. They are fitted with flow meters and controlled by variable frequency drives (VFDs). Three of these pumps feed sodium hypochlorite to the clarifiers and are set to 6 gallons per hour (gph). The fourth is used at the backwash filters and is set to 10 gph.
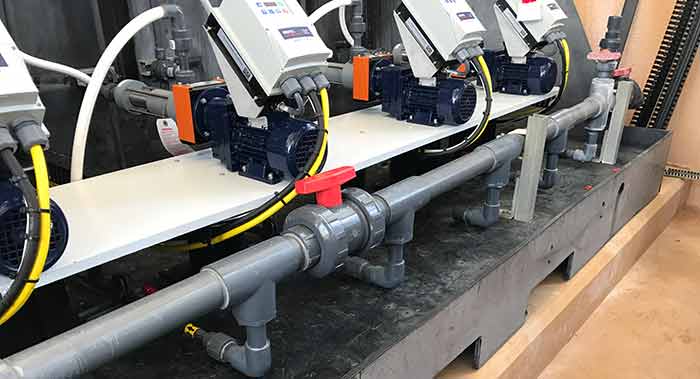
PCPs are often constructed of robust materials that enable them to withstand the harsh and corrosive properties of bleach and other mild to aggressive chemistries.
The sodium hypochlorite pump housing can be constructed of chlorinated polyvinyl chloride (CPVC). The elastomer stator, elastomer joint cover and the elastomer bellows in the mechanical seal can be made from a chemical-resistant material such as rubber and fluoropolymer elastomer. The rotor, coupling rod and mechanical seal work well in titanium. The gear motors work well when finished with two-part epoxy chemical-resistant paint.
The VFDs, which have a National Electrical Manufacturers Association (NEMA) 4X rating, can be plugged into a 120-volt power outlet and use a 4- to 20-milliamp signal for stop, start and speed control of the integrated drive motor, enabling the pumps to seamlessly maintain the correct process requirements for the application.
The Results
Since the installations, Holowell said SWRF’s new PCPs have required virtually no maintenance. Leakage, crystallization and process interruptions have not been issues, leading to energy savings and a significant reduction in maintenance costs and manpower required to keep the operation running.
While SWRF’s diaphragm metering pumps faced frequent problems with crystallization that led to process interruptions and safety concerns, the PCPs run continually with no issues.
The biggest savings, Holowell said, is time and manpower. In the past, many plant managers and operators misunderstood PCPs for chemical metering because of probable misapplication. End users were concerned about dry-run issues, seal failures and difficulties replacing parts.
But the perception is changing.
Robust parts that are configured for the application along with the correct sealing make a difference in the overall performance of PCPs in chemical applications.
For Holowell and his team at SWRF in Cape Coral, PCPs have been a game changer. “We love them,” he said. “We hardly touch them. They just sit up there and purr.”