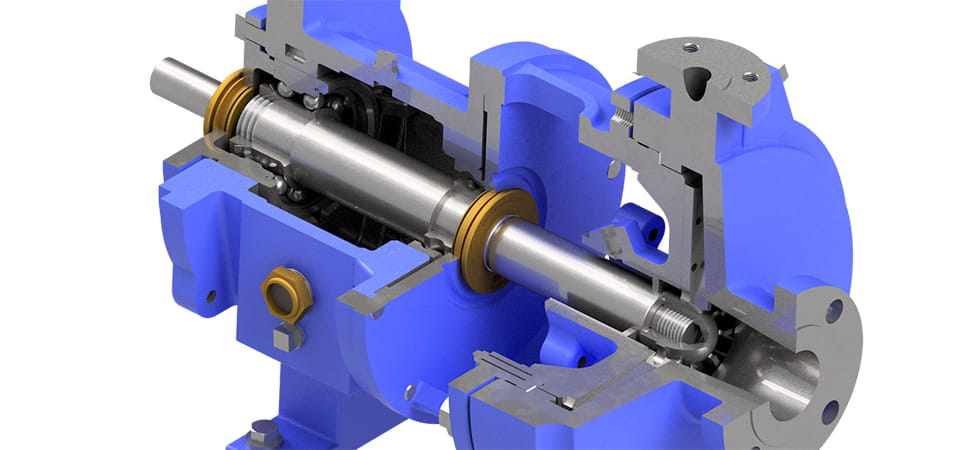
The number one cause of industrial equipment failure is lubrication contamination. When kept clean and dry, lubricants can provide years of wear protection. The struggle to achieve months or even weeks of service life between oil changes is because of contamination ingress.
Is there visible dirt and water in the oil? Are there elevated water and particle contamination trends in the oil analysis? Is bearing failure occurring often? If dirty oil did not go into the machine, the most common pathway is a failed oil seal. A well-designed and properly specified oil seal or bearing isolator solves this contamination problem in the toughest applications.
All bearing isolators are not created equal. Making tweaks to the isolator’s design and selecting technology designed for the equipment type can improve overall performance.
Design Tweaks
A simpler approach can improve bearing lubrication protection. Understanding how a bearing system works allows the bearing isolator to be incrementally improved. This system’s approach examines the bearing housing environment from an energy balance perspective.
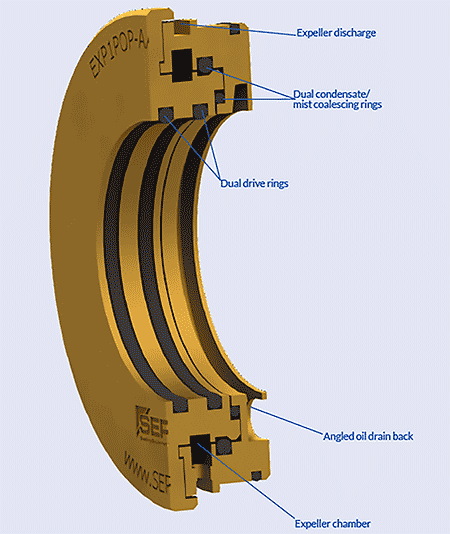
Many traditional bearing isolators are excellent at preventing contamination during operation. They use centrifugal force during rotation to expel any contaminants that may enter. However, during shutdown, ingress may occur because of energy balance.
A typical bearing housing interacts with the environment by always trying to be in equilibrium with its surroundings. During operation, the housing vents to the atmosphere because it is at a higher temperature and pressure than the atmospheric side. After shutdown, the housing’s internal temperature cools. Since cool air is denser than warm air, the bearing housing consumes the air inside and begins to create a vacuum. As a result, air enters from outside until reaching equilibrium. Moisture and dust travel in with this air, contaminating the lubricant if an effective oil seal is not installed.
To prevent this contamination during static conditions, some bearing isolators have a design tweak that keeps contaminants within the isolator and breaks down their energy. The moisture and dust enter the isolator, and the energy is broken down as they are forced through an axial throttling gap then a longer radial gap (Image 1). The contaminants are captured within the internal condensate trap and allowed to drain out through a small static weep hole at the six o’clock position of the bearing isolator. They never reach the lubricant, even during shutdown.
Equipment-Specific Technology
To fully protect lubricants, a bearing isolator with a specialized design may be needed for some equipment. Most rotating drives will function well with a standard bearing isolator (Image 2). For example, many pump and motor arrangements will succeed with the standard technology. However, if the application is critical or specialized, a design specific to the equipment may be needed.
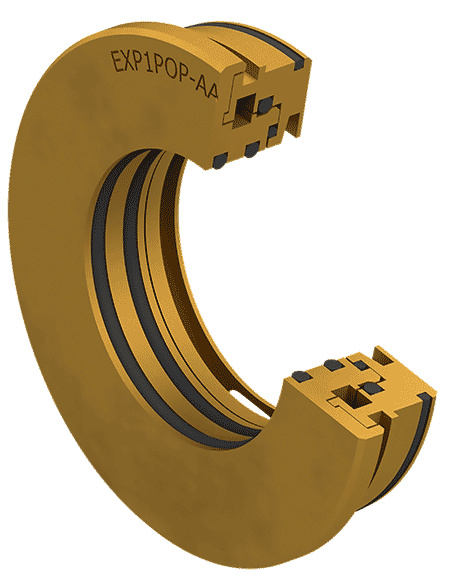
Gearboxes
Many gearboxes operate beneath the equipment they drive. If any leakage occurs, the lubricant within the gearbox is at greater risk of contamination from whatever drops on it. For this reason, reliability and maintenance teams may need a more robust seal for their gearboxes.
In addition to this risk of easy contamination, gearboxes have several different lubrication methods, including flooded or bath, splash and forced or spray mist. Regardless of the technique, the lubricant must remain free of water, dust and other contaminants. Selecting an oil seal designed specifically for gearboxes may improve the cleanliness of the lubrication system. Part of this technology’s design includes a shelter for a lip seal to provide a positive seal without contacting equipment and causing wear.
Pillow blocks
Pillow block housings are on a pedestal and mounted to a surface to support a rotating shaft that is parallel to the surface. They are used in many applications and industries including:
- belt drives connecting motors and pumps
- longer shafts connecting motors to gearboxes
- paper machines
Pillow block bearing manufacturers typically include labyrinth (LOR/LER) rings to seal the bearings, which may not be effective enough for long-term operation and lubricant life. A replacement bearing isolator will extend the lifetime of the equipment and lubricant. However, these must be mountable within the existing LER/LOR ring grooves.
The fit of pillow block bearings is tight, so clean oil is paramount. Many end users opt to replace the existing seal with a bearing isolator designed for pillow block bearings, especially if the original seal fails prematurely.
Steam turbines
Steam turbines in the power generation industry provide a challenge for sealing technology. These rotating assets operate at extreme temperatures and the steam may coalesce and enter the lubricant. A bearing isolator designed for turbines may require careful selection and installation. It is often in two pieces and requires a tight fit to fully protect the bearings.
Flange-mounted
Flange-mounted bearings help avoid axial load or push on the bearing. A bearing isolator designed for these must be adapted because pressing the stator is not recommended or possible (Image 3).
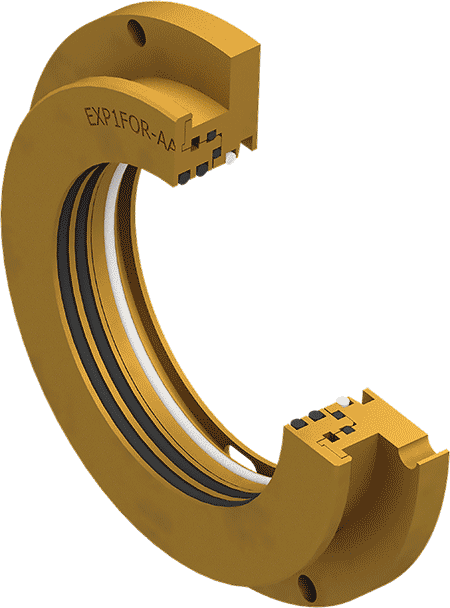
Case Study
One paper mill on the East Coast had three press rolls on a pulp dryer that experienced frequent bearing failures. These failures resulted in labor, roll rebuild and bearing replacement costs. These failures were all on the wet end of the machine. The previous isolators were pressed into the end bell housing. After several manual grease additions, the rotor of the bearing isolator would separate from the stator allowing water ingress and bearing failure.
Roll rebuild and change out were completed about every three months. Annual maintenance costs were estimated at $10,000. Rebuilds cost about $60,000 annually ($30,000 each, usually completed at least twice each year). Bearing replacement costs about $3,500 annually.
In December 2018, a bearing isolator that sealed dynamically and statically replaced the frequently failing design on the press rolls. The new isolator replaced the entire end bell on each machine and was flange mounted. Separation of the seal’s rotor and stator could not occur because it was built as the entire end bell. Even if the bearings were over greased, the rotor could not separate.
Since the installation about two and a half years ago, the bearing isolators have operated successfully, saving about $73,000 annually. This success led to the installation of other bearing isolators in the paper mill in 2020 on thick stock pumps and knot drainers.