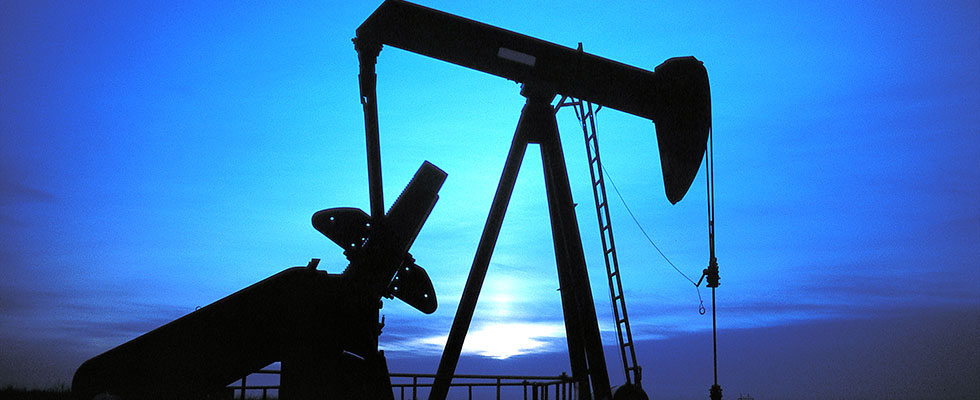
Pumps are a vital tool for operations in the oil and gas industry. This is especially true when it comes to the movement of oil and water throughout the system to handle the desired product supplied downstream as well as the unwanted product produced by oil and gas wells. Proper maintenance and protection of pumps is key not only for efficiency in power consumption, but also for the revenue lost when a pump goes down and backs up the system.
Starting at the well head on a traditional oil well, the most common pump used in artificial lift is the beam pump, also known as a pumpjack. This pump style uses a rod attached to a beam and cam system to rise and fall several feet, catching liquids in the well bore and moving them into a check valve-type system. From this system, fluid is pulled up through a hole and out to treating and storage nearby. Another common type of pump seen in artificial lift are submersible pumps, which are dropped far down into the well bore. High-pressure (mobile) pumps are another type used for the fracturing, stimulating and cementing stages of the well bore to create faster and greater amounts of product capture.
Once the liquids have been moved through separation, they end up in various tanks on-site. Some of these tanks are dedicated to oil; others are used to store waste, most of which is produced water, also known as saltwater.
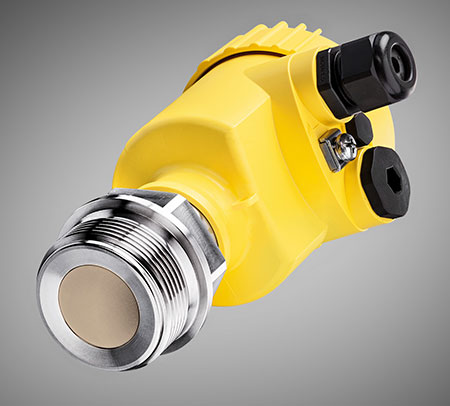
Depending on the system design, oil may be either picked up by tank trucks or pushed further downstream to a larger central gathering system for further processing. It is then sent on to bulk storage before going to the pipeline and thus to the refineries.
This process is similar for the produced water. It may be hauled out or pumped via a pipe to a saltwater disposal facility (SWD), which uses high-pressure pumps to inject the water into a disposal well reaching deep underground.
Generally, two types of pumps are used in these applications once the liquids have reached the first stage of gathering: centrifugal and positive displacement (PD) pumps.
Centrifugal pumps use the centrifugal force of a motor-driven impeller to pull the fluid in through the inlet side and out through the outlet side. They are more commonly seen in oil transfer applications as they can move at a high flow rate at lower pressures.
A general disadvantage to centrifugal pumps can be loss of prime due to low level or empty tanks. This condition can lead to cavitation and heat buildup, which can degrade the pump’s impeller, bearings and other components. Eventually, the damage produces poor performance at best and catastrophic failure over time.
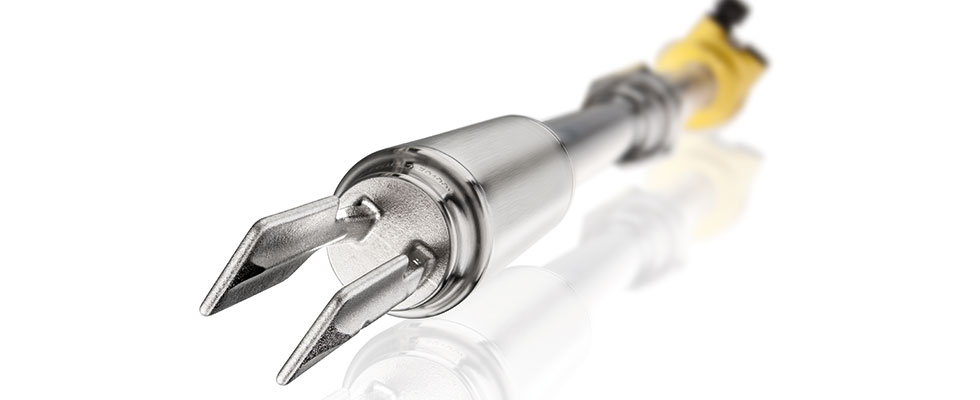
Positive displacement means a fixed volume of liquid is pumped per cycle or stroke. These pumps are more commonly seen on the SWD disposal side. They can generate higher pressures due to the lack of fluid slippage in the pump gears or plungers at lower power consumption than may be required to generate the same pressures with centrifugal pumps. This lower power consumption translates to monetary savings over centrifugal pumps. In these applications, higher pressure is more important than higher flow rates, giving PD pumps another advantage.
A disadvantage that positive displacement pumps share with centrifugal pumps is the likelihood to become damaged if the unit pumps dry.
This is because of the tight tolerances inherent to their design and the heat and friction that can be generated when they are running dry.
Fortunately, there are newer pump technologies and designs of existing technologies that can compensate for adverse conditions. Some pumps may even have built-in monitoring to shut the pump down before catastrophic failure can occur. Despite this progress in pump technology, there are countless older systems still in the field, and many pumps sold today still do not incorporate newer technologies and refinements.
With older pump technology still prevalent in the field, many producers and contract disposal locations use low-cost external methods of pump protection for their high-cost systems.
Tank level monitoring is one way to monitor if a tank is being emptied to a point where a dry pump condition can occur. Continuous level measurement these days has been moving away from mechanical-style float systems to guided wave radars (GWR) or pulse radars to monitor levels in the tank. Incorporating a scaled signal such as a 4-20 milliampere (mA) output to a local programmable logic controller (PLC) can accomplish this task, as can Modbus and HART protocols.
By using the same scaled system from the transmitter as loaded in the PLC, the PLC can be programmed to also act as a pump shutdown at a predetermined level in the tank. Additionally, a second lower-level setting can be used to act as a backup alarm.
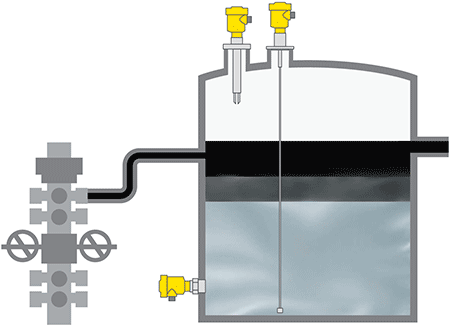
Tank level monitoring can also be accomplished with pressure-based transmitters. In vented tanks, a single pressure transmitter is installed at a point where it will trigger above the height of the outlet pipe. It uses the head pressure of the fluid in the tank as a scaled output to the PLC in the same way as the radar transmitters. Head pressure will be higher on a water tank at a given height compared to an oil tank due to differences in density; this is an important piece of information to know when setting up the scaled output. This can be accomplished at the transmitter or in the PLC. It is also important to use the correct pressure range transmitter (not to oversize or undersize the range) and to know how much mixed fluids will be in the tank, as these lead to diminished accuracy.
The aforementioned options are not the only methods that are currently being used to protect a pump in the oil and gas industry. However, there is now less of an incentive to use products which can seize up and fail due to their mechanical nature and the environment they are subjected to. Since the cost of more solid-state devices has come down over the years, generally due to the volumes being supplied these days, many producers have moved away from mechanical systems due to their reliability issues. In any case, it is important for the user to evaluate what makes the most sense for their system and to choose the solution that is best for their needs.