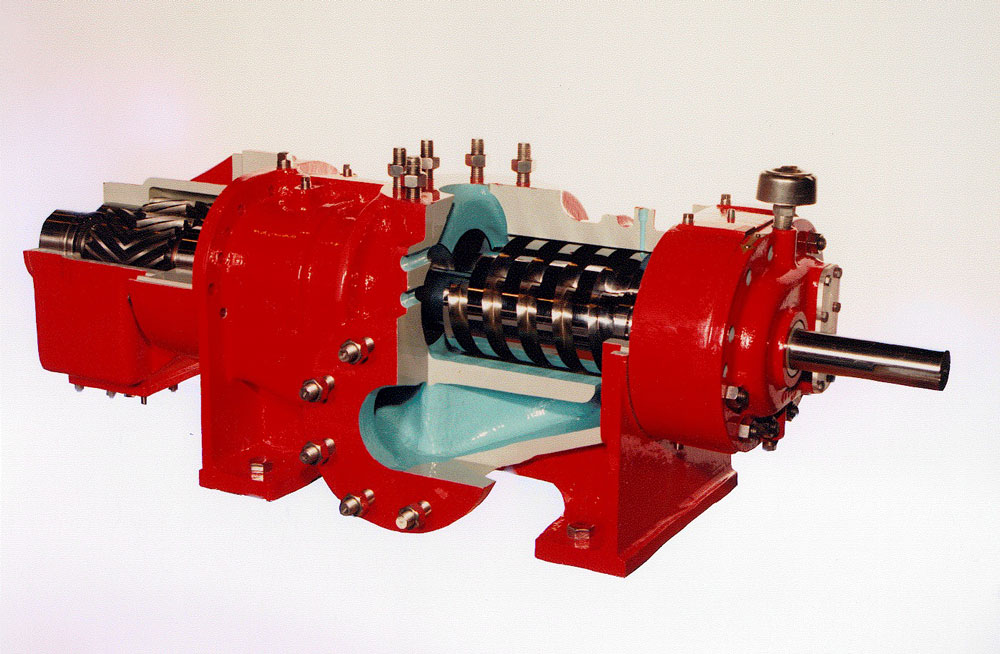
Twin-screw positive displacement pumps provide performance solutions for many chemical batch processing applications. Frequently, twin-screw pumps are the “last resort” because they can solve many pumping challenges, but the technology is not widely known. The twin-screw pump itself can be more expensive compared to a centrifugal pump. However, when comparing the total cost of ownership (TCO) for a system optimized for a twin-screw pump, the twin-screw pump quickly becomes an attractive option. Twin-screw pumps should be considered in any application where the process may involve risk of cavitation, some gas or vapor content, variations in flow, temperature, pressure, liquid characteristics or viscosity. Twin-screw performance excels in chemical process and transfer applications that experience one or more of these variations, as well as any operating conditions that may be difficult or push the limits of other, more common pumps.
Twin-screw designs in chemical processing applications are capable of flow rates up to 3,000 cubic meters per hour (m3/h), differential pressures that exceed 100 bar, product temperatures up to 400 C (752 F), and product viscosities from less than 1 centipoise (cP) up to 1,000,000 centipoise (cP), making them a robust piece of machinery. They can handle a variety of process conditions that exist in the chemical manufacturing and processing industry, such as dry run, self-priming, wide capacity range, flushing, cleaning and flow control.
Variable frequency drives (VFD) are a strong supporting technology for twin-screw pumps. Using a VFD today allows users to leverage the full flexibility of the twin-screw pump, since the pump capacity depends on speed and is not affected much by the differential pressure. Using a VFD allows users to utilize the full performance range from 10% up to 100% of the design speed and capacity range.
When evaluating TCO during startup, operation, maintenance and shutdown, a twin-screw pump may be the most economical solution.
The ABCs of Two-Screw Technology
Twin-screw pumps are capable of handling multiple liquids or products over extended viscosity ranges during batch processing. They can also contend with a wide range of liquid characteristics—such as lubricating, nonlubricating, corrosive and abrasive liquids—in addition to liquids containing entrained gas.
A centrifugal pump’s impeller creates an area of low pressure at the impeller’s eye. When pumping a fluid containing entrained gas, the gas will separate and collect at this point. This phenomenon, known as vapor locking, happens when gases at the eye restrict liquid flow through the impeller. The only way to correct vapor locking is to remove the gas. This involves stopping the pump, removing the air from the system and repriming the pump. Twin-screw and rotary positive displacement pumps are volumetric machines and not limited in this aspect. Entrained gas entering the pumping cavity is displaced with the fluid discharged from the pump as the pump discharge is isolated from pump suction.
A second benefit offered by twin-screw pumps is energy efficiency. Twin-screw and other rotary positive displacement pumps’ volumetric efficiency increases as the viscosity increases. This is due to the internal clearances becoming more effective in sealing the pumping cavity. Due to their design, centrifugal pumps will experience a loss of capacity and efficiency as viscosity increases. Internal friction losses in a centrifugal pump will increase as the viscosity increases, resulting in reduced capacity, head development and efficiency. Centrifugal pump capacity will also vary as the system pressure changes, resulting in the need for additional controls such as control valves and variable speed drives.
Twin-screw pumps offer a low net positive suction head requirement (NPSHr). This allows users to pump different liquids with one pump design. A twin-screw pump offers low NPSH because it reduces the resistance to the flow of the liquid entering the pumping chambers; with higher resistance to flow, higher pressure drops are generated, which can increase the likelihood of cavitation.
Specific design features of a twin-screw pump that reduce a liquid’s resistance to flow include:
- divided flow paths that split the incoming fluid to opposing ends of the case
- lower axial speeds within the pumping chamber that are a function of the pump rotational speed and selected screw pitches
- the avoidance of fluid acceleration
A typical batch process may involve a change in the characteristics of the product and components of the pumped material as the batch process progresses. Each type of product requires a range of pressures and temperatures during batch processing to initiate the appropriate chemical reactions. The reactions typically require a pump that can circulate the product from the reactor vessel through a heat exchanger and then back to the vessel. As such, the pump must be able to handle the full range of product viscosities as it changes from the reactant’s characteristics to the final product, and also be capable of emptying the reactor after each batch.
Low NPSHr and run-dry capabilities become important at this stage because any product left in the reactor is not available for further use. Pumping out the reactor with a low liquid level and emptying it with gas slugs, plus the ability for the pump to run dry, can increase plant efficiency and profitability. A twin-screw pump’s mechanical seal support and internal clearances maintained by rigid timing gears allow it to handle this process requirement. This makes the twin-screw pump capable of pumping the low-viscosity fluids involved in solvent or caustic cleaning cycles in addition to the higher viscosity final products created in the reactor.
Additional Design Considerations
Twin-screw pump designs offer optional jacketing for the pump body and stuffing box housings, adding additional operational flexibility during startup, shutdown, cleaning cycles and upset conditions. Screw profiles and pitches can be customized to meet specific operating requirements, delivering application-specific efficiency. Stuffing boxes can also be customized to provide multiple industry standard seal plans. Many models include a rotor design that offers a back pull-out feature to aid inspection and maintenance. This eliminates the need to disturb piping or the driver.
Special hard coatings such as ceramic, chrome, nickel and cobalt-based materials can also be used to add wear resistance to critical pumping surfaces such as the body bore and screws. The pump’s casing can be manufactured from any machinable alloy, depending on the application’s need for corrosion protection. Pumps have been manufactured using materials including cast iron, ductile iron, white iron, Ni-resist, steel, low-temp steel, stainless steel, duplex stainless steel and Hastelloy.
Flow Control & Energy Recuperation
Twin-screw pumps move fluid inside closed chambers formed by the screws. Consequently, the pump capacity depends directly and mainly on pump speed. Pump speed control will allow users to optimize the process control. Flow control is a function of the pump speed. As long as the pump outlet pressure is higher than the inlet pressure, it operates as a pump and adds energy to the flow, consuming energy.
When the inlet pressure, however, is higher than the outlet pressure, the pump acts as a hydraulic motor and recuperates the hydraulic energy provided by the process. It acts as a power recuperating throttle or it is an energy recuperating flow or pressure control valve (ERCV). Twin-screw machines can extract hydraulic energy from the process fluid and feed it back into the power grid.
Robust Capability
Understanding the requirements of each application is the key in sizing and designing these heavy-duty robust pumps. The design concept must include conditions experienced during startup, operation (full range), maintenance and shutdown. System designers should work together with the pump manufacturer to fully understand the process so that maximum benefits are achieved.
Each application is different, which may alter the design of the twin-screw pump to allow for options such as special clearances, special coatings, flange ratings, mechanical seal arrangements, suction and discharge nozzle locations, instrumentation and other components. This high grade of customization allows the twin-screw pump to operate in specific process conditions in every production facility.
According to American Petroleum Institute (API) 676, twin-screw pumps are noncontacting pumps. This is correct, however, there are two variations of noncontacting. For all low-viscosity, dry-run or gas-handling applications, the fully mechanical noncontacting design is recommended. This pump design and can handle virtually all process fluids without rotor-liner contact.
If the process fluid allows a lubricating support between rotors and liner (like in gears or three-screw pumps, etc.), the twin-screw pumps can be optimized for higher efficiency by reducing the radial clearances of the screws and using the hydrodynamic support film to avoid metal-to-metal contact. Hybrid solutions can accept some gas or flushing fluids at lower pressures (clean-in-place, self-priming) while still maintaining a high efficiency.
Because twin-screw pumps can handle the full performance range required and they can be manufactured in high temperatures, corrosion-resistant and abrasion-resistant designs, these pumps perform well in batch processing applications. Specific chemical processing applications that can benefit from the use of twin-screw pumps include the manufacturing of polymer adhesives, polymer sealing solutions, polymer cements, structural foams and pelletized polymers that are used to create products such as carpet threads and backing, pen grips, knobs, packaging, personal care products, automotive components and more.