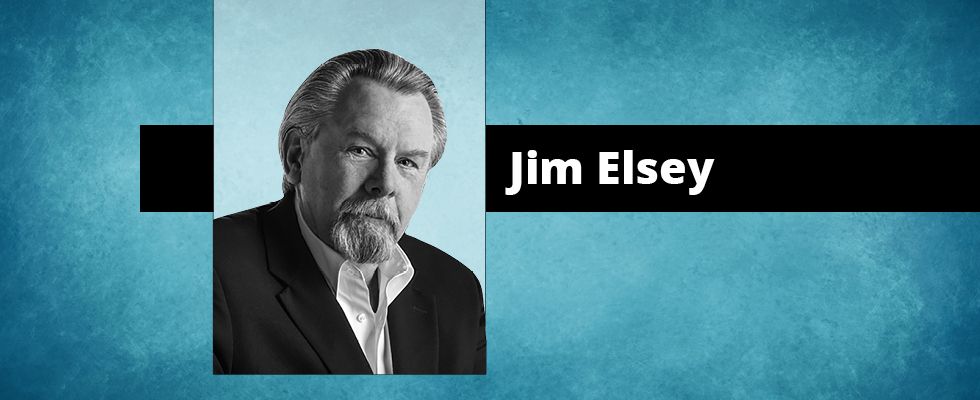
Correction:
Before we get to this month’s column, I wish to correct a misleading statement from my December 2019 column that was pointed out by an astute reader. In that article, I stated that for the total pressure tally in a pump system that the pump suction pressure must be added to the pump discharge pressure to determine if the flange pressure ratings will be exceeded or not. This is a misleading choice of words to describe the condition. A more accurate way of stating the problem is that the suction pressure plus the pump’s maximum developed pressure is equal to the total pressure. Once I reviewed the change, I decided to add more clarification as follows: Developed pressure is the differential pressure across the pump, but don’t just look solely at the condition point—you must also consider the worst case (maximum pressure), which likely will be at the shut-off point. In summary: The mistake is that many people only consider the pump developed/differential pressure and erroneously omit the suction pressure in the total system pressure calculation. It is easy to forget this factor and then exceed the pump and/or piping system pressure ratings. Read the whole article here.
Given a set of fluid properties and the required hydraulic condition point for a specific pump system, the next 12 people you ask will select six different pumps and some will be poor choices. The decision-making process for the best pump selection should be based on facts and data, knowledge and experience. The decision should not be based on supposition and limited to the local available product selection.
Decision Factors in Pump Selection
Sometimes pump selection is a crazy game of “whack a mole”—if you pick one thing here, it affects something else over there and then, just as you satisfy that one thing, another issue will defiantly appear, and so on. In my pump fundamentals classes I anecdotally equate this conundrum as: “It’s like having French speaking feral cats drunk on red wine trying to herd Russian speaking ADHD squirrels (that are off of their meds) into a cardboard box on a Monday at midnight … during a lightning storm.”
Price
The frequently argued—and often erroneous—decision point that we all will concede is the pump price (initial cost). Of course, the decision point of lowest price assumes that the pump is correctly fitted, sized and constructed of the proper materials. Additionally, it assumes that all of the associated costs for the pump purchase, installation, operation and maintenance are factored in—or are they? Did you consider the cost to operate and maintain the pump over the next five to 10 years and beyond?
All other pump selection factors are assumed to be satisfactorily addressed. Perhaps there is a pump specification and all the proposed pumps meet the minimum specification? A really good idea would be to have an evaluation spreadsheet with the weighted decision criteria addressed and factored in the formula.
If you don’t have a pump specification, and/or you are experiencing poor reliability with your past pump choices, then I would recommend you look at some additional factors discussed in this article.
Relationship to BEP
The easiest and most frequent question is: How close is the pump operating point to the best efficiency point (BEP)? We all know that the BEP point of head and flow is where the pump was designed to run, and we assume it must be a good place. In the absence of any other data, this is a safe bet most of the time. The bad news is that you may have difficulty finding a pump that is designed for your specific hydraulic point (or range). And, if you do find one, it may be geometrically challenging (think shaft orientation, footprint, piping and base configurations), cost prohibitive or require an unacceptably long delivery. You may also need to compromise because of additional considerations such as duty cycle and other questions (like where is the system curve intersecting the pump curve?) will come into play.
Explore, calculate and confirm if the system curve is really intersecting the pump curve at the BEP point of the pump. A common mistake in real-life applications is that the system owner believes the system curve is in one place, but in reality, it is somewhere else. See my August 2019 column “Wishing and Hoping” for reference. If the intersection point is not in a good place, the result will be poor efficiency, which directly translates to high energy costs, reduced reliability and increased maintenance expenses.
Just because the system curve does not intersect the pump curve at or near BEP is not a singular reason to reject that pump. Look at the pump curve and the allowable safe operating region. Many pumps have a broad and acceptable operating range that is generally free from deleterious pump issues like high radial thrust, suction/discharge recirculation cavitation, minimum flow or low efficiency issues.
NPSHr/a & NPSH Margin
NPSH is a concern because the pump requires a certain level of fluid energy on the suction side to operate properly.
NPSH margin = NPSHa ÷ NPSHr
Net positive suction head required = NPSHr
Net positive suction head available = NPSHa
Equation 1
I have pontificated about NPSH margin for most of my career. I lecture about it, I teach about it, I joke about it, I have written over a dozen articles about it, I consult with clients about it, and I always find it is one of the most misunderstood subjects in the world—second only to the rules (laws) for the game of cricket.
There is no magic involved on the suction side of the pump. It is simple and basic science because the pump is not capable of reaching out and pulling the fluid into the pump. The pump does not have arms or hands, additionally the fluid has no tensile strength, so the effort would be futile anyway.
The suction system (the portion of the system upstream of the pump suction flange) must supply the energy required to supply the fluid to the pump. It is the inherent and implicit responsibility of the system designer to conceive, calculate and construct the suction system to provide sufficient NPSHa (energy) to the pump. Fast forward to the present day for your system and the designer is long gone, consequently someone (you?) must do the NPSHa calculation and make sure the pump does not require more NPSHr than the system can provide. As a matter of fact, there needs to be a positive amount of margin. The margin in many cases needs to be a minimum of 1.2 to 1.6 just to overcome and meet the deficit that is created by the 3 percent head drop of the pump that is the parasitic loss from the NPSHr test evolution. The margin may need to be even higher than 1.6 for the pump to accomplish full performance capabilities. Refer to ANSI standard 9.6.1-2012 for definitions, guidelines and standards.
Note that over time, the system NPSHa will likely decrease and the NPSHr will increase. This means the system’s NPSH margin you had on day one may disappear by year three.
If you don’t have sufficient margin, the pump will cavitate and die. Pump graveyards are overcrowded with middle-aged pumps that died for this reason.
Maximum Impeller Diameter
Most petroleum industry customers will not accept a pump that is selected at maximum impeller diameter (aka, “full wheel”). There are many reasons for this decision beside the fact that API 610–11 (2010) specifications will be invoked (see section 6.1.4). Some simple reasons are that the end user may wish to change the process slightly and wants performance margin for the current pump to be able to deliver another 5 percent head increase.
Not to be confused with the stated purpose of API 610 specifications, the customer may also want the ability to increase future pump performance to accommodate a system design change or adjust to other factors like system age (increased friction). Other reasons may be that it is a new and complex system design and the engineer/designer is looking for some design tolerance factors (wiggle room). In the past, many pumps were erroneously oversized for this reason. Oversized pumps will frequently lead to premature pump failure.
Pump Operating Speed
For the exact same hydraulic condition point of head and flow, science will tell you that a faster pump is typically more efficient than a slower pump, and the faster pump will be smaller than a slower pump. Of course, a physically smaller pump is also less costly (initially) than a larger pump because at the bottom of the profit and loss sheet a pump has a specific cost per pound of material. Less material and a smaller footprint both equate to lower cost.
I am “old school” and not always a big fan of the smaller and faster pump. I believe that pump reliability increases by exponential factors as they slow down (typically a cube function proportional to speed). Also slower pumps weigh more and that added weight (think mass) assists with vibration dampening, mitigation of temperature and pressure transients, reduction of flange loading and moments (torque) effects and the reduction of shaft deflection and NPSHr.
I will concede that as the required energy level goes up for the application the more you will likely want and need to accept a faster pump. See my full column on this subject in the Pumps & Systems August 2017 issue.
Fluid Properties
Fluid properties, or as I like to refer to them, the “fluid personality,” can make all the difference in the success or failure of an application. If you live in a world that only pumps clean, ambient temperature water, you can skip this part and live happily ever after. However, for those of us that pump dirty and nasty liquids and hot acids and bases, super cold liquids that really want to be gases, highly viscous fluids, and then just for fun mix in some non-Newtonian fluids—you really need to be aware.
Viscosity, Temperature Percentage of Solids
In my opinion, if the fluid has a viscosity above 30 centipoise, the pump performance must be corrected (centrifugal pumps). Most pump selection software programs will rightfully correct for viscosity at an even significantly lower level.
If there are solids in the fluid, you need to calculate and minimize the impeller tip speed, material selections need to be wear resistant, and horsepower (hp) calculations will require adjustment. For most pumps, a liquid temperature above 350 F, and surely by 500 F, requires the proper means to mitigate the effects of the heat, the rate of temperature change and the negative effects on alignment, nozzle loading, bearing life and mechanical seal integrity.
Duty Cycle
I mentioned duty cycle earlier in the article. The short definition of duty cycle is to define how often the pump will start and how long does it operate once it starts. If a 1-hp submersible sump pump moving ambient temperature water is only going to start up once a month and run for 5 minutes or less, you don’t need to be as finicky with the pump selection like you do when it is a 250- to 10,000-hp pump running 24/7. The sump pump’s main criteria is that it does need to be reliable.
Pump Boundaries & Considerations
Pumps—like all equipment—have boundaries and limitations that also have consequences as you approach and/or exceed them. All of the factors cannot be covered in one article, but this list hits some of the most common factors.
- Temperature
- Horsepower—brake horsepower (BHP) per 100 revolutions per minute (rpm) shaft limits
- Specific gravity—manifests as BHP
- Viscosity—manifests as BHP
- Speed—rotor dynamics, bearing and inertia limitations from the impeller(s)
- Suction pressure—combines with differential pressure for total pressure and becomes flange and casing limits
- pH, acid or base of the fluid—metallurgical or materials issues
- Rheology—amount of solids, type of slurry and if the fluid is Newtonian or non-Newtonion
- Specific speed and suction specific speed
- One stage or multiple stages—developed head per stage limits
- Series or parallel
- Base and foundation designs
- Type of drivers and couplings
- Variable speed
- Severity of service, duty cycles, operation periodicity
- Availability of parts, repairs, service and technical assistance