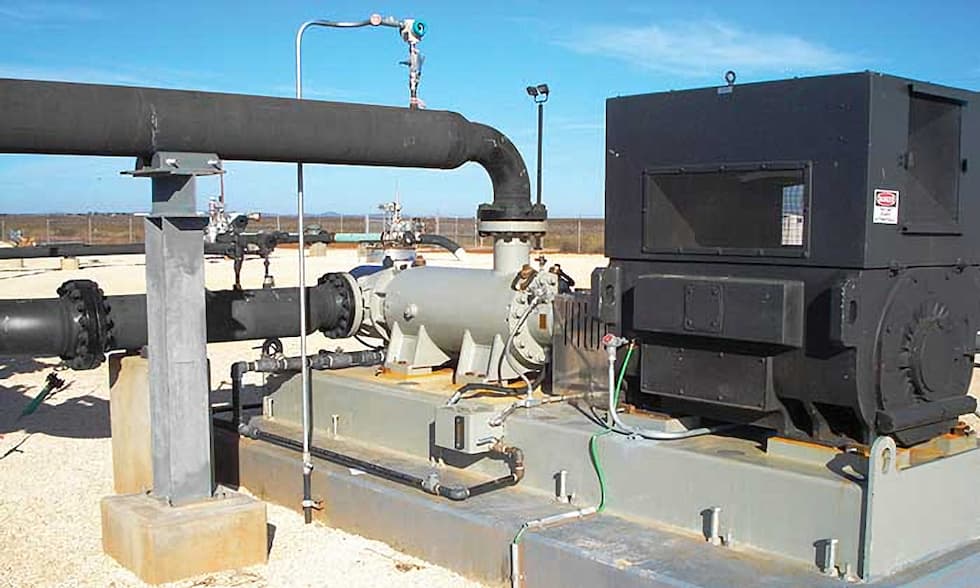
Moving heavy crude oil through pipelines can be difficult and expensive. The largest single contributor to operating expenditures (opex) for pipeline operators is the cost of energy, specifically the energy to drive pumps. For highly viscous and dense materials, like heavy oil and bitumen, the selection of energy-efficient pump technology is especially critical for controlling costs, affording savings of 20% to 50% in power consumption.
An understanding of the impact of viscosity on pumping performance becomes more important as the global demand for new crude oil production grows. McKinsey & Company, a global management firm, estimates that during the next two decades, exploration and production companies will need to add 38 million barrels per day of new crude production to meet demand.
With this growing demand comes increasing reliance on heavy crude oil. More than half of the world's recoverable crude oil is 22 degrees American Petroleum Institute (API) gravity or lower, with viscosities in the range of 50 to over 1000 centistokes (cSt) depending on API gravity, temperature and chemical composition. Over 80% of the globe’s technically recoverable heavy oil and natural bitumen is concentrated in the Western Hemisphere, including large deposits in Venezuela and Canada as well as California, Alaska and Utah.
Attempts to Mitigate High Viscosity
Pipeline operators have explored a variety of approaches to mitigate the effects of high viscosity. A pilot facility in northern Alberta was built to pump raw, heavy tar-like bitumen in a heated state through an insulated and buried long-distance pipeline to decrease viscosity. Other methods include partial upgrading of the oil prior to it entering the pipeline through hydrocracking, hydrotreating or hydrorefining. This approach requires the building of upstream facilities. More commonly, a diluent is added to a viscous fluid to reduce the effective viscosity. Diluents can be hydrocarbons (condensate, gasoline, kerosene or naphtha). However, the diluent itself is a significant opex cost (even if it is later recovered from the transported fluid), and the facilities to transport, store, blend and remove/recycle the diluent further add to costs. Preparation of oil-in-water emulsions requires the addition of 30% to 35% water and a small amount of surfactant.
The most effective method of handling high viscosity, with financial benefit, is the use of suitable pumping technology.
Centrifugal Pumps in High Viscosity Uses
Centrifugal pumps are ubiquitous in pipeline operations, but they are designed for liquids with relatively low viscosity (greater than API 45 degrees) such as water, refined hydrocarbons and light crude oil. On these low viscosity fluids, centrifugal pumps can be operated cost effectively, achieving efficiencies in the mid-80% or better. However, even a slight increase in viscosity degrades the performance of centrifugal pumps due to friction loss. Viscosity is the measure of a fluid’s resistance to shear when energy is applied. The pumping action generates high liquid shear, as the fluid is thrown off the impeller by centrifugal force. The higher the viscosity, the greater the resistance, and the harder the centrifugal pump needs to work—requiring more horsepower and, therefore, consuming more energy.
Rotary PD Pumps in High Viscosity
For a half-century, oil companies and pipeline operators have sought alternatives to centrifugal pumps when moving high viscosity oil. Positive displacement (PD) pumps, known as volumetric pumps, employ a different working principle than centrifugal pumps, reducing the impact of friction loss and thereby increasing efficiency when pumping highly viscous fluids. PD pumps have a displacement per one pumping cycle; that cycle may be reciprocation or rotation. An advantage of PD pumps is they move constant volumes of liquid during each operating cycle, allowing them to maintain a relatively constant flow rate, even as pressure changes. The capabilities allow pipeline operators to precisely and consistently control flow by controlling the pump speed, independent of the fluid pressure.
The flow rate of a PD pump increases as the fluid viscosity increases (i.e. back flow decreases. Unlike other types of pumps, most PD pumps are self-priming, and some can create high vacuum conditions.
Three-Screw Pumps
PD pumps fall into two categories: reciprocating pumps and rotary pumps. One type of rotary PD pump—three spindle screw pumps—is typically favored for high viscosity pipeline applications. Hundreds of three-screw pumps have been installed in Venezuela and western Canada, with early installations each recording more than 54,000 hours of operation. The pumping elements consist of three moving parts: the power rotor (main screw) and two symmetrically opposed idler rotors, all operating within close-fitting housing bores. The incoming process fluid is conveyed by the rotating power rotor by means of the cavity formed with the intermeshing idler rotors. From suction to discharge, the fluid is transferred by means of a series of constantly forming and reforming chambers until it reaches the casing outlet. Unlike centrifugal pumps and some types of PD pumps, three-screw pumps are self-priming, and they require only one mechanical seal, which reduces maintenance costs.
Centrifugal vs. PD Pumps
Despite the known impact of viscous fluids on centrifugal pump efficiency, little literature exists measuring and comparing the economics of applying different pump types to the pipeline pumping of viscous oil. A common configuration of BB3 size centrifugal pump in pipeline services, an 8 x 10-13 with five stages and a rotary PD three-screw pump designed for pipeline service were tested. The two systems were evaluated against a range of fluid viscosities from 10 cSt (20 cSt in the case of the PD pump due to operation limits), to 500 cSt, to determine the effect of increasing viscosity on efficiency, power and, hence, energy opex.
The rated point chosen represents an averaging of a popular rating for BB3 pipeline pump installations: 2,500 feet (762 meters), 3,300 gallons per minute (gpm) (750 cubic meters per hour [m3/h]). The specific gravity of the fluid was set to 0.9. This results in a differential pressure requirement of 976 pounds per square inch (psi) (67.3 bar). In each case, the duty point (head, flow and specific gravity [SG]) was held constant and the speed was varied to achieve the rated point. For the BB3 centrifugal pump, maximum diameter impellers were used to achieve the best possible efficiency. API 610 test tolerances were used. The viscosity correction method for the BB3 centrifugal pump was American National Standards Institute/Hydraulic Institute (ANSI/HI) 9.6.7 2015.
The performance results for different viscosities are shown in Image 1.
The shapes of the efficiency curves differ significantly. The BB3 centrifugal pump efficiency declines with increasing viscosity, from mid-80% to mid-60%. The three-screw pump efficiency increases to reach a maximum at around 50 cSt and then declines slowly. This is due to the interplay of two different mechanisms within the pump: the backflow (which decreases with higher fluid viscosity) and the frictional losses (which slowly increase with higher fluid viscosity).
Payback Period is a Single Year With energy costs representing the largest single opex expenditure, this significant difference in pump efficiency has a huge impact on pipeline operators’ bottom line. Image 2 shows how the annual electric power costs would differ when running the pumps 8,000 hours per year. The extent of the savings of using three-screw pumps on highly viscous oil varies depending on the local cost of electrical power. The costs shown are calculated using typical 2020 costs per kilowatt-hour (kWh) for industrial power users, expressed in U.S. dollars: $0.067 in the U.S., $0.117 in Brazil and $0.206 in Germany. For pipelines highly viscous and dense materials like heavy oil and bitumen, investment in three-screw pumping technology has a positive return on investment. These pumps, which operate reliably for 25 to 30 years, can produce annual savings in electrical power that exceeds the purchase costs. As the global demand for oil drives growth in the extraction of heavy oil, pipeline operators need to consider which combination of crude oil viscosity modification and pumping technology will keep their opex most manageable.