Energy savings of 30 percent was realized after installation of five compact pumps, control/monitoring units and motors.
KSB AG
01/28/2019
For art galleries and museums, a priority must be creating and maintaining the perfect environmental conditions to ensure the fabric of their artwork is not compromised. For many buildings of historical and architectural significance in Venice, respecting such a status while managing the humidity, air quality and temperature is both expensive and a major challenge. Venetians have modernized building services infrastructure while honoring the past.
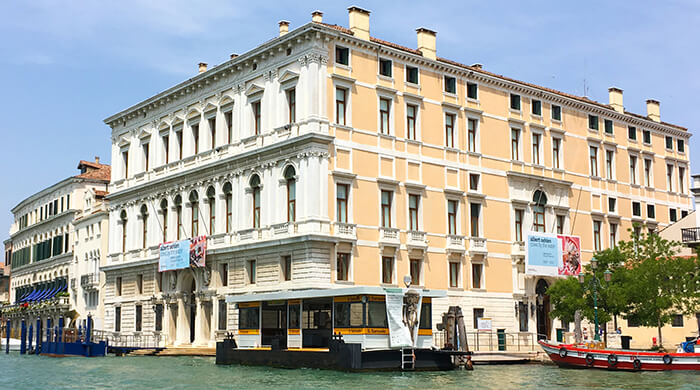
Culture Meets Sustainability
In 2016, following a careful analysis of the past energy consumption, an extensive renovation project was implemented. This involved the renewal of parts of environmental services infrastructure to optimize energy consumption, while at the same time delivering the sensitive conditions required for housing valuable works of art. The essential components needed to achieve energy savings were replacement of hot and cold water pumps, valves, strainers and compensators, all of which were sourced from the supplier by the project contractors Siram SPA. The main goal of the project was to update the hot and cold water systems for the two heating and cooling circuits in the building.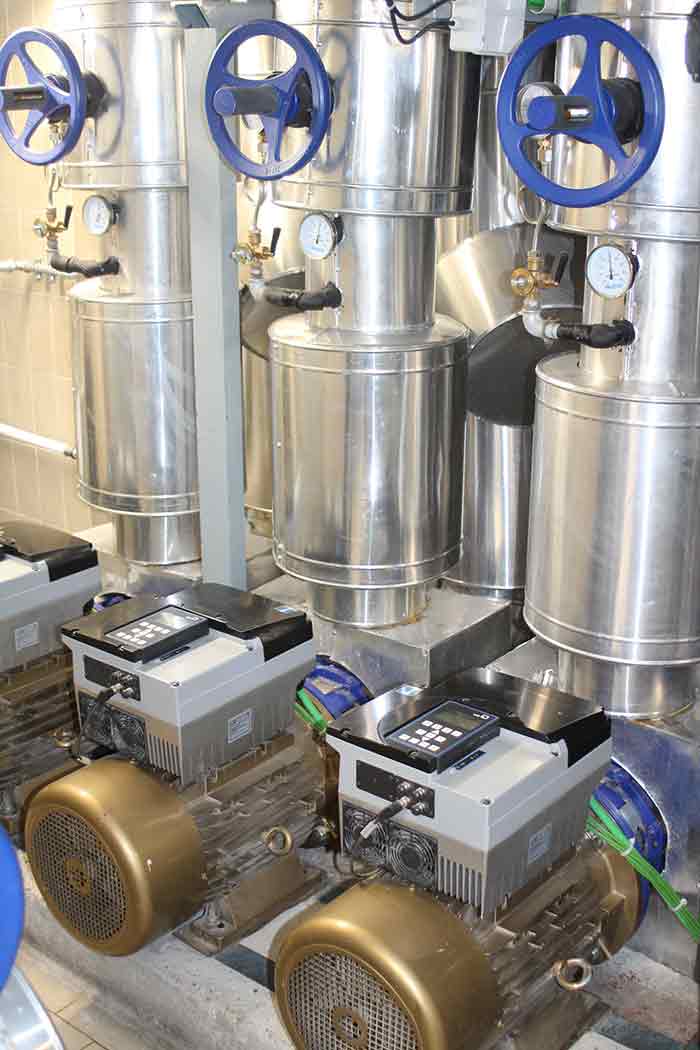
Making Pumps Pay
Modern centrifugal pumps have already achieved a high level of efficiency. When the pumps appear to be consuming more energy than necessary, it is probably due to lack of attention. Any pump can only operate as efficiently as its system—including valves, piping, filters or heat exchangers—allows it to. At the Palazzo Grassi, the performance of these components working as one ultimately affects the controlled environment within the building. Designing and installing a completely new pumping infrastructure for air conditioning and ventilation in a historic building does present a challenge, especially because the buildings were never designed for such equipment. In the case of the Palazzo Grassi, the pump room on the lower ground floor is best described as “compact.” Therefore, the first consideration was finding five suitably sized pumps, two for hot water circuits and three for the cold water circuits that could deliver the water flows and pressures for the system. Then there was the matter of connecting new piping to the existing infrastructure. Finally, there was meeting the user’s requirement for energy efficiency. Fortunately, these three requirements could be satisfied by using compact, close-coupled pumps that are equipped with an advanced control/monitoring unit. Three of the pumps are driven by an energy-efficient motor that meets class IE5 requirements, and two are driven by IE4-class motors. All five pumps are fitted with a modular, self-cooling frequency inverter.Compact, Close-Coupled Pumps
These pumps have proved successful in many applications around the world over several decades and are especially useful where space is at a premium because the pump, the advanced control/monitoring unit and motor are connected in one compact unit, giving it a space-saving design.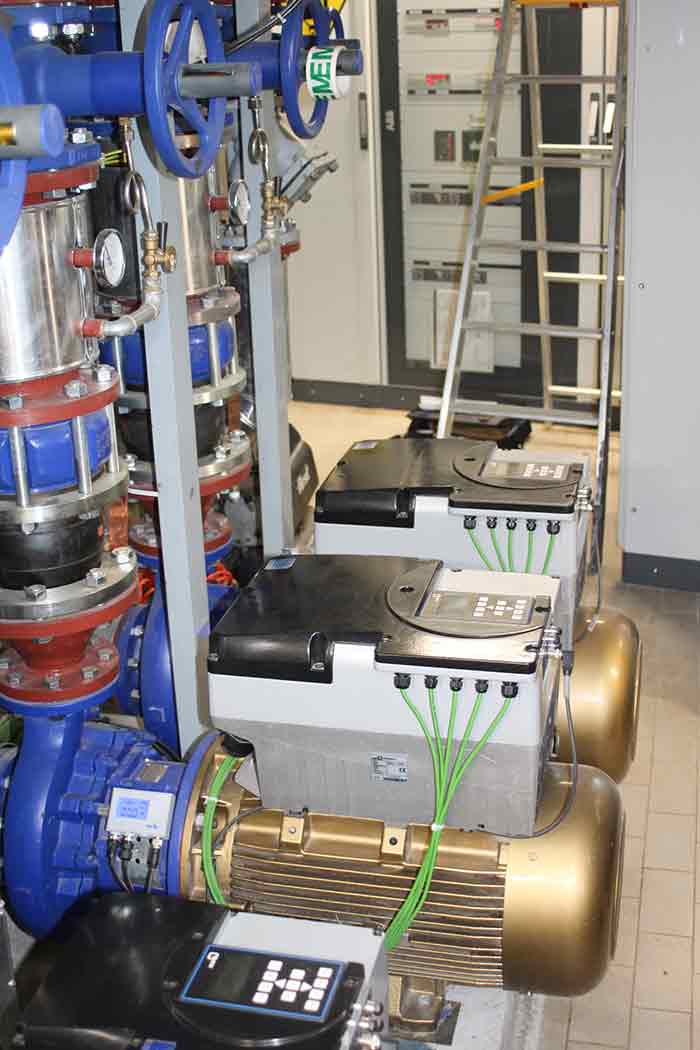
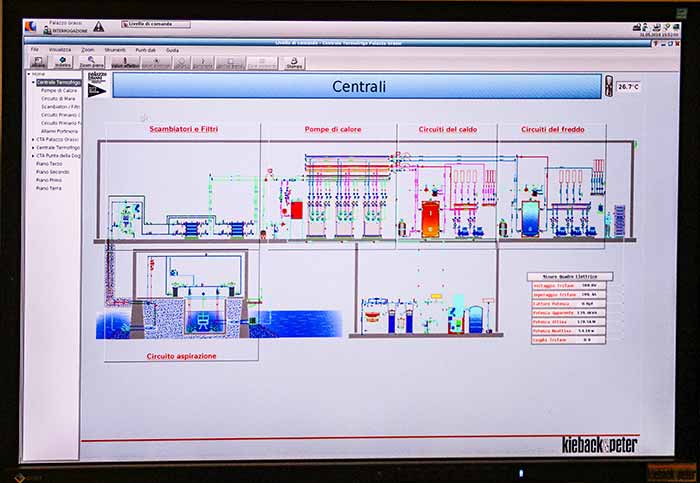