Increase reliability and reduce emissions through pump selection.
ITT Goulds Pumps
06/25/2018
Editor’s Note: Here, Ed Kupp, global product manager, ANSI Pumps, with ITT Goulds Pumps Inc., provides an update to explain how the technology has changed since this article first ran in 1993 in Pumps & Systems. You can read the original 1993 article in full below.
In 1961, the first American Voluntary Standards (AVS) chemical pump was introduced. Since that time, it has gone on to become a highly popular process pump with more than 1 million installations worldwide. The pump has experienced various upgrades since its original release.
When the original article was published in December 1993, upgrades had just been made to the pump, such as increasing the oil sump, making labyrinth seals standard and using a sight glass to monitor oil level. A low-flow version had also been recently introduced. The benefits of all of these upgrades to users are discussed in detail in the article.
Here is a brief overview of changes to the pump since then:
- In 1994, a new seal chamber design provided the best seal environment for single mechanical seals on services with or without solids, air or vapors.
- In 2004, the high-temperature, high-pressure model line offers longer service life and safety features in extreme thermal services.
- 2015 saw the launch of a monitoring device that works as a fitness tracker for pumps and other rotating equipment. This standard feature empowers anyone to safely monitor equipment from a distance using a smartphone or tablet through Bluetooth transmission.
- In 2016, a variable speed pump control solution was launched.
- Finally, in 2017, the 3 x 4-17 pump size was introduced for chemical process applications where net positive suction head available (NPSHa) is low, resulting in 1,800 rotations per minute (rpm) hydraulics at higher heads and lower flows.
Here is the original article published in December 1993.
Today, chemical manufacturers and users are faced with global competition and pending environmental restrictions that threaten to reduce profitability. The need to reduce overall operating costs has driven pump users at chemical plants to focus on improving reliability and eliminating or reducing fugitive emissions.
Sealed Pumps
The mechanically sealed chemical process pump, which meets American Society of Mechanical Engineers/American National Standards Institute (ASME/ANSI) B73.1M standards, is the workhorse of the chemical processing industries. It will continue to be used on a wide range of process applications—such as liquids containing significant amounts of solids (sodium chlorate, alum, sodium carbonate, chemical wastewater), light slurries (silver nitrate and acetone slurries), viscous liquids (above 150 centipoise [cP], including black liquor and titanium dioxide), and stringy materials where sealless pumps may not be economical to use. In addition to its ability to handle tough services, the flexibility of the design—along with improved low-emission mechanical seals—continues to make ANSI pumps the standard in this field.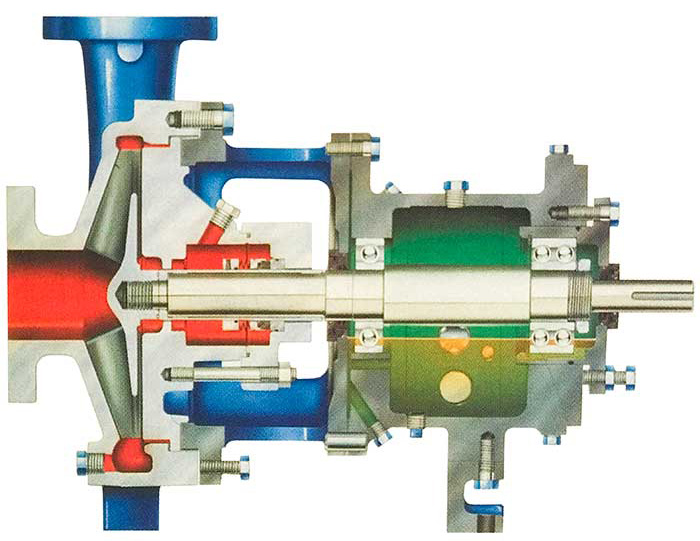
- Enclosed impellers are prone to plugging and premature wear in the above services due to small wear surface area. (Performance and efficiency cannot be renewed without replacing wear rings.)
- Open or semi-open impellers are reliable in these services and are standard for ANSI pumps. (Simple external impeller adjustments allow easy maintenance of performance and efficiency, and there are no wear rings to replace, yielding long-term energy savings.)
- The small internal passageways in sealless pumps are subject to plugging while handling liquids with only small amounts (5 percent) of solids. Viscosity handling is also limited.
- Design solutions separate the pump end from the drive end to allow sealless pumps to handle these services, but these modifications can be expensive and may not be cost effective.
ANSI Reliability Improvements
To meet emissions regulations and improve reliability, process industries have pushed ANSI pump manufacturers to improve performance. Some manufacturers have formed alliances with users to share technology and improve standard designs. By working together, the theoretical has been combined with the realities of applying pumps on a multitude of services and making them last. These efforts have produced the features listed below that many major ANSI pump manufacturers have incorporated. At a minimum, users should purchase ANSI pumps with features that best meet their application needs. However, most new designs incorporate features systematically to provide reliable products. Compromising designs to save money or add standard plant features—substituting a vendor’s standard labyrinth seal with the plant’s standard oil seal, for example—may not be advisable. New ANSI pump features include the following:- Labyrinth oil seals are designed to prevent premature bearing failure from lubricant contamination or oil loss. These noncontacting seals have replaced Buna-rubber lip seals, whose useful life was three to six months under normal conditions. Materials of construction include carbon-filled Teflon, bronze or stainless steel.
- Increased oil sump capacity provides better heat transfer for more effective oil cooling. Bearings operating at lower temperatures contribute to longer life.
- A rigid frame foot reduces the effect of pipe loads on shaft alignment. Misalignment won’t exceed 0.002 inches under load, and pump and driver alignment are better maintained.
- Bull’s eye sight glasses ensure proper oil level, which is critical to bearing life. Level oilers have often been misused, leading to over- or under-filling sumps, both of which contribute to bearing failure. Sight glasses are also convenient for checking the oil condition visually to determine if a change is necessary. Constant-level oiler manufacturers are just now introducing oilers that eliminate the potential for improper oil level settings while providing a sight glass, combining the best features of both methods.
- Mounting flanges accommodate an optional adapter that simplifies pump/motor shaft alignment, saving the user time and money during installation.
- Condition monitoring bosses on power ends provide consistent measurement points for temperature and vibration sensors. Many users report increased pump life from using predictive maintenance to identify and correct problems early. Taking measurements at the same point aids in proper interpretation of readings and allows personnel to move through the plant more quickly on inspections.
- Engineered large seal chambers, specifically designed for today’s mechanical seals, increase seal life through improved lubrication, cooling, air venting and solids handling. The chambers allow seal manufacturers to engineer and apply more reliable designs, including cartridge seals.
Specialty Pumps for Improved Reliability
Many diversified chemical producers are moving production of commodity chemicals to Asia-Pacific and Latin American regions to take advantage of lower labor and production costs. As a result, chemical production in the United States is being driven toward manufacturing specialty chemicals typically produced in small runs or batches. Examples include methyl isobutyl ketone (MIBK) and parateriary butylphenol (PTBP). Pump applications for these batch-type processes are usually low flow, in the range of 0 to 100 gallons per minute (gpm). Traditionally, users install standard process pumps and throttle the discharge valves to obtain low-flow performance. However, these pumps are not designed to operate continuously in this range. Higher radial loads and increased shaft deflection lead to premature bearing and seal failure. Costly downtime and maintenance expenses result. For low-flow operation, users should specify a pump designed to meet specific service conditions. ANSI pumps designed for low-flow operation are available to increase pump and plant reliability. Improvements come from a casing and impeller designed for low-flow operation. Low-flow designs use concentric volutes and radial vane impellers to reduce radial loads, eliminating hydraulic and mechanical problems from throttled low flows. Some designs reduce radial loads as much as 85 percent compared to end-suction expanding volute pumps in this service. Shaft deflections from high radial loads are minimized, optimizing bearing, mechanical seal and overall pump life. A disadvantage of low-flow ANSI pumps is that they sacrifice some efficiency to reliably handle viscous and solids-containing liquids. Another approach to low-flow, high-head applications is the regenerative turbine pump. This design directs liquid by a passageway so that it circulates in and out of the impeller many times on its way from pump inlet to outlet. Both centrifugal and shearing action work together to efficiently develop relatively high heads at low flows. Regenerative turbines also use concentric volutes and radial vaned impellers to obtain the reliability benefits discussed above. One drawback is that this type of pump utilizes close running clearances to keep efficiency high and it is therefore normally used on clean liquid applications.Sealless Pumps
With the implementation of the Clean Air Act, sealless pumps offer a dynamic solution to controlling emissions. Not only should sealless pumps be strongly considered to control emissions of the 149 volatile organic compounds identified by the U.S. Environmental Protection Agency (EPA), but they also should be viewed as solutions to many difficult applications encountered in CPI plants today. For example, if users are experiencing sealing problems because of the pumped product’s poor lubricity (typical of acidic products in the range of 0 to 3 pH, such as sulfuric or hydrochloric acids), difficulty with product crystallization at seal faces (usually with caustic products in the range of 10 to 14 pH, such as sodium hydroxide and potassium hydroxide) or are frustrated with sophisticated auxiliary piping plans to provide clean, cool flush liquid to mechanical seal faces, sealless pumps may be the answer.Improved Reliability with Mag Drives
It is well recognized that mechanical seals and bearings are the two items that fail most often in pumps. These failures are often directly related to improper application and installation, poor operating practices or lack of maintenance, pipe strain or misalignment. All of these again lead to high bearing loads, shaft deflection, and bearing and seal failure. Magnetic drive pumps have neither a mechanical seal that can fail nor a driven shaft that can be subjected to pipe strain or misalignment. The driven shaft is separated from the drive shaft by a magnetic coupling, eliminating the two major causes of pump failure.Critical Mag Drive Features
Reliable magnetic drive pumps must address two critical concerns:- Proper lubrication of the journal bearings.
- Removal of heat generated by eddy currents in the recirculation circuit.
- Is the flow continuous or intermittent?
- Upon shutdown, what reaction (if any) will the process fluid have to residual heat? Chemicals like butadiene and formaldehyde may polymerize, leaving deposits inside the drive section and on the bearings.
- Can the process shut down automatically, resulting in the pump operating at shut-off condition?
- Conversely, can the system allow the pump to operate at the extreme right of the pump curve, which can adversely affect NPSHr and cause motor overload or excessive thrust?
- What are the fluid characteristics, including vapor pressure curves, specific heat, viscosity over the process temperature range, and the effects of heating and cooling on the process fluid? Benzene freezes at 42 F (depending on the installation location, address the possibility of exposure to low temperatures), and toluene diisocyanate freezes at 72 F and begins to polymerize at 127 F (again, protect the installation or use jacketing if necessary). Maleic anhydride freezes at 130 F (use heating jackets or temperature control).
- What about the customer’s practical knowledge of the corrosive nature of the chemical? Sometimes the standard corrosion charts don’t give the whole story.
Abrasives
When pumping fluids containing particles, the traditional solution is to use very hard bearings (silicon carbide) operating against a hard or coated journal. The application of sealless pumps should go beyond this seemingly easy approach. Consideration must be given to:- The abrasiveness of the solids.
- The size of the particles.
- The quantity of the particles.
- Whether they can agglomerate.
- What creates the particles (reaction, catalyst, temperature).
Mag Drive Condition Monitoring
Magnetic drive pump reliability is also affected by operating practices. Condition monitoring devices can be applied to shut pumps down before a critical failure. Maintenance can then be performed, or operator errors corrected, before the pump is put back into service. Temperature detection and power monitoring together provide the best basic protection. Temperature detection indicates internal pump problems such as plugged recirculation paths, while power monitoring prevents dry-run failure. Other devices available include low amp relays, leak detection indicators and package control systems.Installation
The effort involved in selecting the right pump for a given CPI application can be nullified by poor installation. As much effort, if not more, should be put into installation design to ensure expected performance is achieved. Important steps include:- Lay out suction piping to provide NPSH available to the pump in excess of NPSH required. A common recommendation: NPSHa > NPSHr + 2 to 5 feet.
- Provide a straight run twice the length of the pipe diameter (2D) to the pump suction flange to prevent added turbulence at the impeller eye, which could lead to premature (incipient) cavitation.
- Install conventional or cartridge mechanical seals according to manufacturer recommendations.
- Meet seal flush requirements by providing an external flush at the necessary pressure and temperature or add auxiliary piping for flushing on the pump.
- Prepare the foundation before grouting the baseplate.
- Select grout that will meet installation requirements.
- Select a baseplate to maximize pump, seal and motor reliability. Many vendors offer baseplates with enhancements such as 0.002 inches/feet flatness, leveling screws, motor alignment screws, continuous drip rims and other features designed to ease installation and alignment and increase pump life.
- Align equipment according to manufacturer specifications.
- Select and install condition monitoring devices for sealless pumps.