How one company accomplished a complete overhaul of four pumps at water treatment facility.
Henkel Corporation
11/27/2017
Nearly every business, industry, municipality, school and home has and uses pumps. They pump everything from drinking water and wastewater in cities and towns to heavy aggregate solutions in mines, quarries, power plants, and in oil and gas fields. As common as pumps are, when normally functioning they are often overlooked until they need attention. This usually shows itself in a few ways:
- increasing bearing noise
- sudden increase in vibration
- pumping output dropping 25 to 50 percent, which shows up as an increase on the electric bill
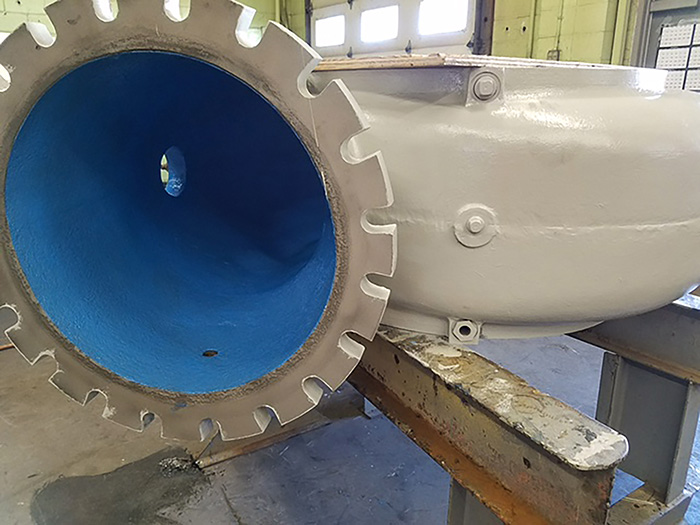
Examining Cost to Repair Pumps vs. Cost to Replace
Recently, the regional Water Pollution Control Authority in Waterbury, Connecticut, reached the point where major mid-life service was required on all four of their Allis Chalmers Model NSYV 250 Influent pumps. The pumps had been in service for 19 years and were showing signs that major service would be required in the near future. The City of Waterbury employed the professional engineering services of Tighe and Bond to develop proposals and assist in managing the project for the sequential overhaul of the pumps, motors, drive shafts and discharge check valves over a 12-month span. The technical and price evaluation resulted in the project award to New England Pump and Valve Company (NEPV)..jpg)
- the provider’s resources (technical, financial, and workforce) to complete the work as proposed
- the relationships within complementary industries required in order to complete
- the work
- their professional reputation
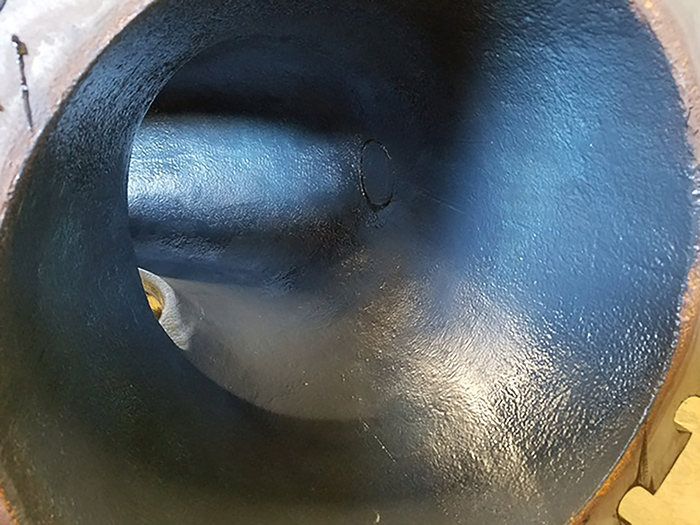
- Performance testing (pre- and post-overhaul) that included pump and motor energy consumption and efficiency
- Vibration testing (pre- and post-overhaul) that is critical to optimizing pump and motor function and life. This also validated the dynamic balancing of the pump, motor and driveshaft
- Inspection and completion reporting for all major components including the pump, motor, driveshaft and check valve
- Pump casing: Sandblasting of both interior and exterior. The interior of the volute was then coated with ceramic coatings.
- Impeller improvement: The original impeller was still within spec and in good condition. It was sandblasted and coated with ceramic coatings. The impeller assembly (impeller, key, shaft, and nut) was made using thread lockers for proper fit. This technique prevents movement and potential vibration sources, and to insure no corrosion occurs in between the threads should future work on the pump be required.
- Pump system overhaul: Replacement of parts including bearings, seals, split mechanical seal, wear rings and shaft sleeve. Moderate shaft wear grooving was welded, machined and dynamically balanced with the impeller. All tolerances were restored to factory specifications and the exterior surfaces coated with a two-part epoxy.
Conclusion
So what did the test results show in this rebuild? An average efficiency improvement of 6 percent, and significant improvements in both pump head/flow and maximum flow rates. The targeted 2 percent energy reduction for this 250 horsepower (hp) motor-driven pump was exceeded, and these results are in line with prior studies by federal, state/local and industry groups. This is expected to expand as the work on the three remaining pumps is completed. The key to the success of this project and the efficiencies gained in the equipment performance are tied to the expertise of the service provider and their ability to properly select, prep and apply the correct ceramic coatings to meet the need. Rigorous oversight and documentation of the project by the design team ensured that the project goals were measured and achieved. So when faced with what may appear at first to be a negative situation, seek out the right solution coupled with the correct solution providers and it is likely the outcome will be a positive one.
To read other Efficiency Matters articles, go here.