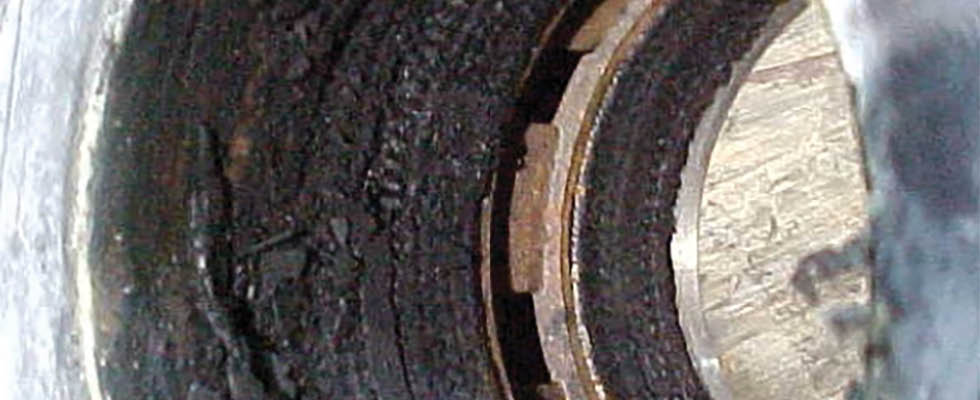
Compression packing serves as a vital component in pumps, ensuring efficient fluid containment and system operation. Over time, however, wear and damage can compromise its effectiveness, leading to leakage and reduced performance. Understanding when it is time to replace compression packing is crucial for maintaining optimal pump functionality and preventing costly downtime. Here are several key indicators to consider.
1. Extreme Leakage
One of the most obvious signs that compression packing needs replacement is when there is excessive leakage from the back of the stuffing box. This leakage is typically characterized by high rates, such as 10 drops per minute or 0.2 gallons per day, amounting to a significant loss of fluid. In practical terms, this equates to approximately 69 gallons per year. Such extreme leakage indicates a severe deterioration of the packing material and warrants immediate attention to avoid further damage to the pump and surrounding equipment.
2. Visible Wear or Damage
Visual inspection plays a crucial role in identifying the condition of compression packing. When the packing becomes worn or damaged, it often exhibits visible signs, such as leaking around the shaft or noticeable deterioration of the packing material. These signs indicate the packing is no longer effectively sealing the pump, resulting in fluid leakage and potential performance issues. Therefore, regular visual inspections are essential for detecting wear and damage early and initiating timely replacement.
3. Noticeable Wear or Damage
If wear or damage is noticeable upon inspection, it serves as a clear indication that the compression packing requires replacement. Ignoring visible signs of wear can lead to further deterioration over time, exacerbating fluid loss and compromising pump performance. Therefore, it is imperative to address any noticeable wear or damage promptly to maintain optimal pump operation and prevent potential equipment failures.
4. Increased Fluid Loss Over Time
Ongoing wear or damage to compression packing can result in a gradual increase in fluid loss from the pump. As the packing material deteriorates, its ability to seal the pump effectively diminishes, leading to greater fluid leakage. Monitoring fluid loss rates can provide valuable insight into the condition of the packing and help determine when replacement is necessary to prevent further fluid loss and maintain pump efficiency.
5. Presence of Solids
The accumulation of solids within the packing can cause damage and compromise its sealing capabilities. Solids may enter the packing due to contaminants in the pumped fluid or improper maintenance. If solids are detected during inspection, it indicates the packing may be compromised and in need of replacement to restore optimal pump performance and prevent potential damage.
6. Damage From Improper Installation
Improper installation of compression packing can result in damage and premature failure. Common installation errors include incorrect packing size, improper tightening or inadequate lubrication. If packing is damaged during installation or does not perform as expected, it should be replaced using
proper installation techniques to ensure effective sealing and prevent further damage to the pump.
7. Mismatched Packing Selection
Selecting the wrong type of compression packing for a specific application can result in leakage and inefficiencies. Different pump applications require different types of packing materials to withstand varying operating conditions and fluid characteristics. If the wrong packing has been selected or if the application requirements have changed, it may be necessary to replace the packing with a suitable alternative to ensure proper sealing and prevent leakage.
Recognizing when it is time to replace compression packing in a pump is essential for maintaining efficient pump operation and preventing costly downtime. By monitoring for signs of wear, damage, fluid loss and other indicators, pump operators can proactively address packing issues and ensure optimal pump performance. Regular inspection, proper maintenance and timely replacement of compression packing are key practices for maximizing pump reliability and longevity.
We invite your suggestions for article topics as well as questions on sealing issues so we can better respond to the needs of the industry. Please direct your suggestions and questions to sealingsensequestions@fluidsealing.com.