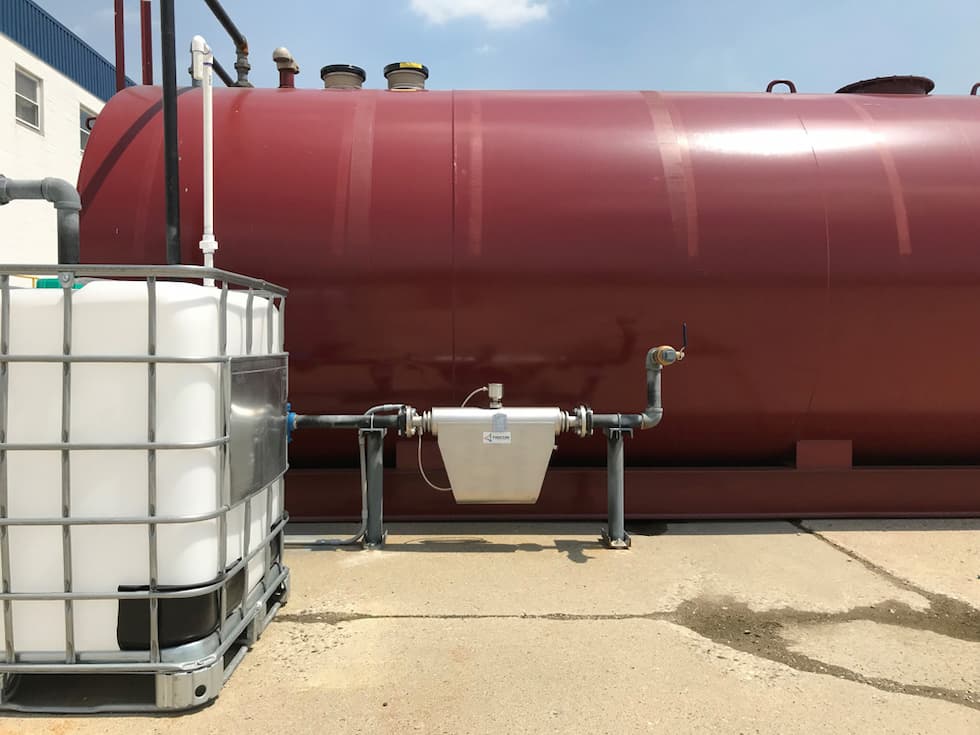
Growing applications of plastic in industrial and consumer markets results in industrial waste. Approximately 80% of the hundreds of millions of tons of plastics used in the United States annually end up in a landfill. Another 15% is incinerated and just 5% is recycled. As industrial waste increases across the world, it also increases global pollution that endangers drinking water and air. Understanding the importance of reducing industrial waste, some manufacturers are turning waste into clean fuels. More specifically, they are turning plastic waste materials into commercially viable byproducts.
In this process, one plastic waste processor converted the recaptured plastic waste stream into high-end, clean, American Society for Testing and Materials (ASTM)-qualified chemicals, fuels and solvents. Offering a sustainable alternative to traditional processes of dealing with plastic waste, this process can develop various green byproducts, such as premium gas, premium diesel, jet fuel, kerosene and other additives. One specific byproduct is a clean, cycled, low sulfur, high lubricity fuel that can be used in off-road diesel and fuel oil engines. Included in the system that recycles all this plastic is a machine that can handle 50 tons of waste per day, equating to 12,000 gallons of liquid fuel per day or 4 million gallons of liquid fuel annually (depending on feedstock quality and run capability).
Flow Meters Monitor Coolant in Condenser Heat Exchange
To ensure accurate conversion of plastics to fuel in the system, flow meters are an essential component in two critical and distinct processes in the waste conversion system: monitoring the flow of coolant during distillation and accurately metering the fuels being dispensed from facility holding tanks into users’ tanks.
The first flow measurement application involves monitoring water temperatures in a heat transfer system vital to condensing hot hydrocarbon-rich gases into liquid fuels. This critical step involves changes in temperature and highly combustible materials and must be closely monitored to ensure safety and optimum performance of the conversion process. While different technology can monitor flow, the challenge was finding the right solution to operate at up to 450 F fluid temperature, handle low viscosity fluids (cooling water), produce flow data with accuracy and fit in tight spaces. Turbine meters offered the best solution in monitoring flow of the heat transfer medium on both sides of the process.
Turbine flow meters were installed in two areas of the cooling system: the cold side and the hot side. Because temperature was not a factor on the cold side, the turbine meter was fitted with a meter-mounted, hall-effect sensor that sends flow data to a remote smart device that converts the pulse output to an analog signal to be read by the programmable logic controller (PLC). The smart converter is Bluetooth-enabled, which allows operators to scale the 4 to 20 milliamps (mA) output to the flow range of the process. This streamlines startup because technicians can define the flow parameters through a mobile app.
The hot side of the condensation system was also fitted with a turbine flow meter, but this time it was fitted with a high-temperature sensor. This sensor consists
of a local high temperature carrier frequency pickup wired to a remote signal amplifier that is installed five feet from the flow meter to protect the electronics from the heat. The digital frequency output signal from the amplifier is converted to 4-20 mA analog signal using the same smart converter and transmitted to the PLC.
Flow Meters Ensure Accurate Fuel Transfers
Accurately monitoring the custody transfer of diesel and gasoline from outdoor storage tanks to tanker trucks required a different flow measurement solution. For this, the plastics recycling manufacturer needed a highly accurate flow monitoring system that interfaced with its plant network to facilitate custody transfer and billing to its users. Because the tanks and meters are outdoors, the flow meter needed to maintain accuracy in the face of changing temperatures and fuel densities and reliably work in Michigan’s harsh weather. Further, the fuel transfer required a high transfer rate and carry C1D1 Ex Certification.
Coriolis mass flow meters met the system’s required maximum flow rate of 200 gallons per minute (gpm) and offered high accuracy, sufficient for custody transfer. Two Coriolis meters were connected to each other on a two-node, multi-drop Modbus network. An ethernet gateway converts data from the two-meter Modbus network to the PLC network’s Ethernet-TCP communications protocol. PLC logic and reporting software allows operators to easily track flow rate, total, temperature and specific gravity of the fuel dispensed to waiting tankers. Meter-mounted transmitters display a batch total for quick and easy comparison to truck-mounted meters. Once verified, the batch total is processed, and the user is automatically billed for onboarded fuel. The batch total is then remotely reset by the PLC and is ready for the next fuel transfer.
The integration of the gateway allows for simplified troubleshooting of the custody transfer meters. Managers can monitor meter performance from their local network computers, enabling them to video call factory technicians and get immediate assistance to diagnose, troubleshoot and advise on parameter changes. This saves travel time and cost and helps keep operations online.
As this was a beta plastics-to-fuels conversion system, not all aspects of how to control this process were defined upfront. A demo program enabled the facility to try several flow meters so it could see which equipment and configuration provided the best fit. A collaborative approach between the flow meter manufacturer and plastics waste processor saved years of research and development costs and allowed operations to go online quickly. The accuracy of flow meters helped the plastics-to-fuel processor determine that its process is not only self-sustaining but profitable—a fact that opens up even greater possibilities.