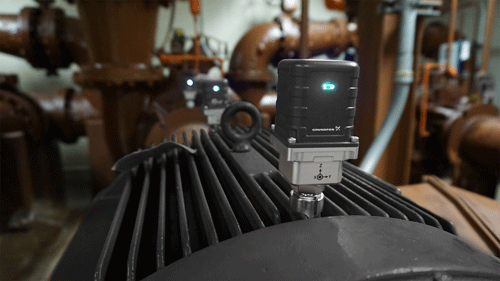
Many aspects of our lives today rely heavily on the continuous operation of some type of machine. From the cars we drive, the ways we communicate, the food we eat and the water going to and from our homes, machines are at the heart of manufacturing or processing our everyday resources.
Pumping equipment accounts for 10% of the world’s energy consumption. When considering other pieces of rotating equipment that run water and wastewater systems such as blowers, compressors, fans and chillers, that number becomes much higher. Each machine is engineered with an optimal point of operation to achieve its highest level of efficiency based on its characteristics such as dimensions, weight, material type and motor type/ratings.
A large percentage of equipment installed today is being operated inefficiently and some is even on the brink of failure. Many factors can alter how close or far away from that design point the equipment will operate at, including vibration, temperature and normal wear and tear. These variables can often be kept in a normal range by following proper installation and maintenance procedures according to the manufacturer’s recommendations found in manuals and training material.
However, damage can also occur naturally as materials break down throughout continuous operation. Whether it be human error, defective components or standard wear and tear, the fact is that rotating equipment will eventually be prone to failure and require intervention from the maintenance crew.
When looking at the operating budget for any municipality, some of the largest line items are allocated to maintenance, repairs and energy costs. The costs for these three alone can account for up to 40% (or more) of a utility’s total spending throughout a given fiscal year. Before the use of advanced sensors and digital services, there was not a good way to reduce those costs. Service crews were, and many still are, tasked with putting out fires as they came up due to being short staffed and having no clear line of sight to the condition of their rotating equipment until the point of failure was reached. Managers also struggle to acquire experienced operators which can have a negative impact on the efficiency of their workflow. These factors make it challenging to catch up on a long backlog of work orders.
What if a user could predict when pumps, blowers and other critical assets were about to fail? With the resources that are available today, utilities can easily optimize their uptime, lower operating costs and stay ahead on daily tasks. Advances in technology over the past 10 to 15 years with electronic sensors, cloud computing and artificial intelligence (AI) have given equipment owners a way to identify small abnormalities in the operating conditions of their rotating equipment before reaching point of failure. Predictive maintenance and service schedules can be based on up-to-date condition data from critical equipment, and plant operators, even nonexperts, can take remedial action before minor issues develop into major disruptions. Here is a quick look at more benefits:
- plan maintenance ahead of time
- experience fewer breakdowns that could lead to downtime or even environmental concerns
- lower maintenance costs and avoid expensive equipment replacement
- receive actionable insights to boost overall efficiency
- reduce energy costs
- gain competitive advantages
How It Works
Advanced wireless sensors can be installed in a noninvasive manner to existing rotating equipment in less than a day. These sensors can be mounted on dry-installed machines such as pumps, blowers, fans or any other rotating equipment within a process. These battery-powered devices collect vital information around the clock while the machines operate and send it to a software system where it is input into machine learning algorithms for analysis. Advanced systems can detect and identify many common machine malfunctions including:
- cavitation
- resonance
- bearing wear
- misalignment
- vibrations
Operators can access the user interface for an instant bill of health for a particular product, allowing them to make data-backed decisions on when maintenance or replacement may be required. The process is achieved in three steps:
Connect:
The sensors can collect the data (tri-axial vibration, surface temp, magnetic flux) from the rotating assets, streaming this information on a continuous basis to some type of software system (web-based, local).
Diagnose:
The diagnostic software system applies machine learning algorithms to the
data sets collected, identifying actionable insights.
Improve:
Insights are presented on the user interface for review at any time along with real-time alert notifications when critical events are detected, providing the visibility needed to address machine-related issues.
Results
Once installed, most of these systems are self-sufficient. The sensors are low maintenance and typically just need to have batteries replaced every couple of years. Most manufacturers maintain the software and can install firmware updates over the air so it is hands-free for the users. On average, utilities can see up to:
- 30% lower maintenance costs
- 20% reduction in energy consumption
- 75% fewer breakdowns
- 45% more uptime