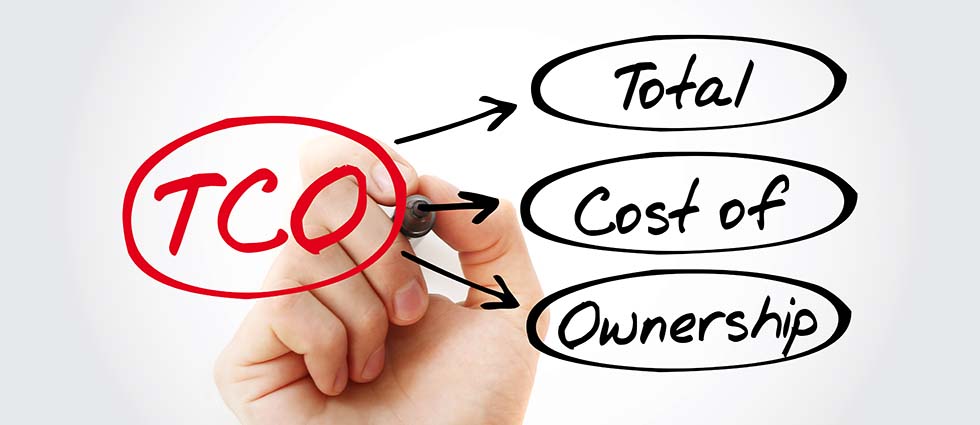
Building a new facility or refinery is no small feat. Often, the new space will include anywhere from 500 to 3,000 pumps, with input from multiple stakeholders, including equipment users, design consultants and engineering procurement and construction (EPC) contractors. These stakeholders provide their input on the pump design parameters such as fluid type, chemical composition temperature, and the size/quantity of particles present.
With multiple stakeholders involved in specifying design parameters and an inherent desire to ensure that equipment is capable for the job, it can be common for margins of safety to be applied and compounded. Centrifugal pumps are designed to operate optimally at one operating point. Stacking of safety/error margins of a few percentage points can result in pumps that are sized incorrectly, delivering poor efficiency and experiencing premature failure.
Aligning the process operating point close to the pump’s best efficiency point (BEP) when selecting centrifugal pumps ensures reliability and minimal wear over time. At the BEP, the pump operates at peak efficiency, as flow passes through the pump with the smallest amount of turbulence. In layman’s terms, the closer a pump runs to its BEP, the longer it will last and the better it will perform.
Centrifugal pumps that operate closer to BEP will provide optimal value over time. As the operating point moves away from BEP, a decrease in life can occur from areas such as casing and impeller wear, seal failures and bearing failures. In addition, higher flow rates can increase the net positive suction head required (NPSHr), which can lead to impeller damage and reduced head generation. Looking through this lens makes it clear that care needs to be put into achieving the correct pump flow and head requirements when initially designing systems and specifying pumps.
Another factor affecting the pump life cycle is when site process requirements are changed. Many plants, such as oil refineries and power stations, have been around for decades, and installing new machines, such as boilers, can change the pump requirements. When any of the plant’s processes are adjusted, this inherently impacts how the pumps need to operate.
Lastly, things happen. Systems can break, and the common path ahead is to repair. Unfortunately, while pump users can identify how to repair equipment, there can be a lack of pump design experience to determine the appropriate design enhancements that can increase pump reliability and reduce the frequency of repairs. This is where having an expert who can do a root cause analysis, suggest courses of action and then improve the pump comes into play.
When considering the potential issues mentioned above—upfront margins of error, out-of-date designs due to updated process requirements, and inevitable breakages—there are essentially three courses of action. These courses are to keep repairing the equipment, replace it with brand-new equipment or carry out a life cycle cost design enhancement (upgrade) to the existing equipment.
While simple repairs are the cheapest option, they do not solve the pump’s issues. Think of it as replacing the brake pads on a vehicle with a warped rotor. While this provides a temporary fix, the rotor issues will inevitably wear the brake pads down in a short period of time. When there are issues inherent to the pump, simple part repairs will lead to the same result over time.
In some cases, it makes sense for an operation to purchase, design and install brand-new pumping systems. However, due to the lesser cost and time involved, life cycle cost design enhancements are often the attractive option. These enhancements can immediately improve pump reliability and efficiency and generate cost savings over time when done correctly.
When discussing life cycle cost design enhancements with different organizations, the initial step is to identify bad actor pumps and specifics about the pumping operation. What are they designed for? Where are they operating? How often do they fail? With this important information in mind, the pump can be evaluated, allowing the equipment design experts to determine which upgrade is needed.Generally, there are three different types of upgrades that can be done to improve total cost of ownership (TCO) and the overall design of the pump: material, mechanical and hydraulic.
Material Upgrades
Sometimes, the material of a pump is not suitable for the purpose it is designed to serve. Or, even more common, the facility’s needs may change over time, making the existing pump ineffective. When this is the case, a material upgrade is the best option.
Material upgrades can accommodate several issues, such as shaft failures, erosion and corrosion damage and excessive wear. By changing the base materials of construction or applying coating technologies, material upgrades can eliminate or considerably reduce wear.
Mechanical Upgrades
As mentioned, a common reason for pump inefficiency is changing demands over time. When the mechanics of a pump are no longer optimized for the pump’s purpose, mechanical upgrades can help.
Mechanical upgrades can cover a wide variety of issues, including shaft, bearing and seal failures, as well as excessive wear. Examples of mechanical upgrades include:
- redesigning a shaft to increase rotor rigidity and integrity
- bearing upgrades to increase load capacity and oil cleanliness through filtration technology
- sealing upgrades such as changing a packed gland to a mechanical seal to reduce leakage and improve safety
This is where design and execution experience is important. Choosing a partner that has both the technical understanding of the pump’s design and the experience of redesigning will help ensure that the newly designed pump fits the required specifications for its application. When considering an upgrade, ask if you trust this partner to design a new pump. If not, they are likely not the right fit.
Hydraulic Upgrades
Hydraulic upgrades also address the root cause of poor reliability—commonly the BEP—where the pump is designed to operate in terms of flow and head. Hydraulic upgrades can solve many pump reliability issues including erosion damage, excessive wear, cavitation damage, insufficient flow/head and the aforementioned failures.
The most common hydraulic upgrades address the major issue of the pump’s output moving away from the BEP. When this occurs, energy efficiency can decrease and pump reliability issues are generally evident. From hydraulic re-rates or a complete drop-in solution to the latest in design standards, adjustments can be made to the design and BEP of the equipment within the bounds of the current space envelope.
Imagine the ability to improve the pump’s BEP and realize the savings this can yield in maintenance and energy costs without touching the surrounding pipework or the foundation. With hydraulic upgrades, this is a reality. There is no one-size-fits-all approach that can automatically improve the reliability, efficiency and life cycle costs. Each pump and application has its own attributes, requiring a deep dive into the root cause of the reliability problems.However, once completing this root cause analysis, one effective solution is a life cycle cost design enhancement, including material, mechanical and hydraulic upgrades.
Dealing with pump reliability issues can be a considerable challenge for plant managers and engineers but it does not have to be that way. By applying analysis techniques and life cycle cost design enhancements, users can lower TCO over time and future-proof plant operations.