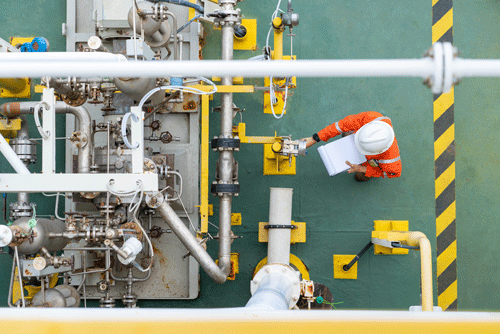
The reliability, availability and trouble-free operation of pumps is always important. Reliability and its requirements should be considered in the pump selection, detail design, installation, commissioning and maintenance of the pump and its associated downstream and upstream. Plant shutdowns due to pump issues have led to production losses worth billions of dollars in lost revenue each year. Additionally, pumps play a major role in the overall safety of facilities. Statistically, there is one fire incident per 1,000 pump failures, and a fire case may cost, on average, more than 1 million dollars. It is easy to see why the cost and commercial conditions of best in class components, seals, bearings, lubrications or technologies for pumps should never prevent their use.
Pump Location & Layout
Pump selection is an important step for the overall reliability and performance of each pumping service. The pump location and its piping are also important to achieve efficient operations and high reliability. A few of the primary goals in selecting a pump’s location are minimizing the length of the suction piping, while satisfying the piping flexibility requirements, as well as minimizing piping loads on pump nozzles. Great care should be taken in selecting a pump’s major components, such as its seals, bearings, etc., to achieve overall reliability, efficient operations and efficiency.
Reliability & Maintenance
Reliability and pump maintenance should not be looked at as isolated topics. Condition monitoring, effective root cause analysis (RCA) of previous failures on similar pumps, time-to-time inspections, overhauls, repairs performed, part replacements and operational procedures should be considered in conjunction with the selection pump’s components. Sometimes improvement plans, such as those to use better lubrication methods or upgraded seals, should be employed to achieve a greater reliability.
Root Cause Analysis
RCA of previous failures and operational problems in similar pumps (or the same pumps in the same services) has always been important. A well-designed maintenance and reliability plan is usually built around descriptions and data of previous failures of similar or the same pumps. In other words, the correct way to prevent a previous failure would be to determine policies, provisions, requirements, needed improvements, etc., when creating a plan to prevent problems. Such data, based on correct RCAs, can also be used for pump specifications and pump selection, renovation/upgrading plans for pumps, proper commissioning and operation supports.
Time-Based Maintenance vs. Condition-Based Maintenance
Preventive maintenance (or time-based maintenance) is still used for pumps in many plants. As a rough indication, more than 75% of maintenance on pumps is still defined based on old-fashioned, time-based maintenance rather than condition-based concepts and modern predictive-maintenance principles. This is not cost-effective, nor efficient; however, transitioning to condition-based maintenance is not itself a simple task. So, this is an area which needs more attention.
Pump Manufacturers vs. Maintenance Work
Another area of concern is the dependence on pump manufacturers for reliability, maintenance and operational support. The fact that a pump manufacturer has manufactured and delivered many pumps—even with so-called successful operating references—does not mean that the manufacturer is the best source for high-quality reliability and maintenance work. Many pump manufacturers do not take responsibility after their guarantee periods and are not often quick in responding to issues. Pump manufacturers position themselves for successful bidding and getting the contract/offer. They should then manufacture the pumps and deliver them to site with successful supports for installation, commissioning and startup. Some manufacturers are capable of this type of long-term maintenance/operation support; however, some others are not capable of such long-term efforts. For example, I have explained to many different pump manufacturer representatives that two days of production loss of a critical plant due to unscheduled shutdown of its pumps may cost more than the pumps themselves. There is too much risk in not using the best available and most reliable technologies in pumps. A few days of delay in technical queries is simply not acceptable.
It is difficult to create a list of general guidelines for reliability, maintenance and operational support. For large/medium size operation companies, an internal technical specialist group may work better than a manufacturer/vendor support team. For long-term operation, the use of a relatively small, mobile team that works full-time for different plants of a large operator could be a good option. Sometimes pump specialist teams at each plant cannot be justified. Of course, for each plant, there might be certain busy times, such as the first year after startup or the six months around a major overhaul. In those busy times, the previously mentioned mobile team might be stationed within the plant.
In any plant or facility, some maintenance work should be completed by an in-house team and other work be subcontracted to vendors, manufacturers and subcontractors. How to manage this depends on many factors, such as plant size, plant details, pump details, location, expected reliability, maintenance policies, etc. In the same way, correct mixture of residential and mobile teams should be formulated case-by-case.
How to Evaluate Maintenance Work
The primary goal in selecting a modern reliability and maintenance program, such as those based on advanced condition-monitoring concepts, is to reduce the overall cost of the operation and maintenance over a long-term period. Then, if a new maintenance policy was introduced to a plant or facility, a measure of success could be the reduction of the combined cost of operation and maintenance. Such a reduction may take time to achieve (around three to five years). For instance, when a modern condition-based maintenance policy is introduced at a major overhaul, the performance of this new policy should be assessed and evaluated at the next major overhaul (four to six years later) to see how effective it was in reducing the overall cost, including lost production due to unscheduled shutdowns.
How Many Spare Parts Are Needed?
An important maintenance decision is directly related to the optimum inventory of spare parts at the plant. Recently there has been a trend to have a smaller number and value of spare parts. For reference, many years ago, the cost value of spare parts was about 6% to 7.5% of the price of the whole pump. These days, this cost ratio (cost of spare parts to initial equipment price) has dropped below 5% in many plants, even under 3.5% for some others. There were old-fashioned maintenance policies, which encouraged keeping an entire spare pump (or many parts and pieces) as spares in a warehouse. Again, it is hard to create a general rule, and the list of spare parts to keep on hand depends on many factors, such as how fast the manufacturer can prepare and deliver spare parts, the
market situation, plant policies, maintenance routines, previous experiences and many more. Still, large inventories of spare parts are ordered and kept in warehouses by many operators after different evaluations and risk assessments. A superior option is to install a standby pump (if possible) that is ready for operation, rather than store an entire pump somewhere in a plant’s warehouse.