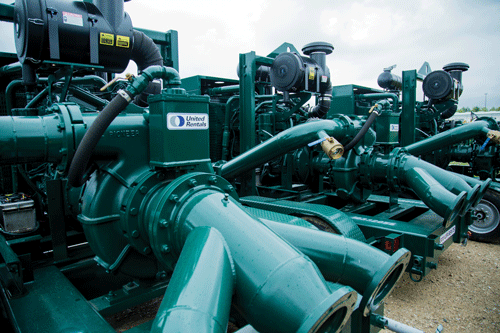
Time is money during a power plant outage. Every hour of production that is reduced or halted due to planned or unplanned maintenance can translate to thousands of dollars in lost revenue. Monitoring the performance of temporary equipment, including pumps and tanks, mitigates the risk that issues with the equipment or the systems it supports could extend the outage and drive the associated costs even higher. While monitoring is essential, manual monitoring is a waste of time and resources. Remote monitoring enabled by advanced telematics offers 24/7 visibility into the performance of temporary equipment and the added advantages of freeing up workers for other outage-related tasks in addition to increasing their safety.
The Value of Remote Equipment Monitoring
With remote monitoring, workers no longer have to travel to and from remote areas of the plant to check temporary equipment or take readings. Wireless sensors coupled with fleet management software allow them to monitor pump and tank readings from a smartphone, tablet or computer. Managers can reallocate hours previously dedicated to manual monitoring, a benefit that holds even more value during today’s skilled-labor shortage. Telemetry is also about safety. A power generation plant is designed to hold permanent equipment, and squeezing in temporary pumps and tanks can make tight spaces even tighter. Remote monitoring keeps workers away from moving machinery, as well as plant areas that may contain hazardous gases or lack sufficient ventilation. For example, in some coal-fired operations, lack of ventilation in tight spaces could put workers at risk of oxygen deprivation. In nuclear power plants, remote monitoring can keep workers out of restricted areas that require special training and permissions to enter.
During a busy shutdown, remote monitoring ensures equipment monitoring gets done. Project managers may ask workers to check pumps or tanks on a designated schedule, but when things get hectic on the plant floor, some of these checks may go unmade. Additionally, telemetry provides insights into critical parameters manual monitoring cannot.
Remote Pump Monitoring
During cooling system maintenance, remote monitoring of pumps is especially critical to help ensure the plant is safe and uninterrupted in operation. Telematics allows for continuous remote monitoring of critical parameters, such as pump speed, pressure, water flow, oil and fuel levels, vibration and engine temperature. It also enables remote control of some of these parameters. Pump telemetry has moved beyond simply monitoring pumps. With some systems today, operators can adjust pump pressure or water flow right from the application dashboard. They can start a pump to adjust the level of cooling water, slow the flow rate or shut down a pump if they see a critical issue happening. That flexibility is important in the changing environment of a planned outage. To further guard against outage delays, remote monitoring solutions can be configured to send alerts if an issue occurs—for instance, if pump pressure falls below or exceeds predetermined thresholds.
Telemetry solutions can also uncover trends or changes in pump operations that could indicate a developing problem. For example, the sensors may pick up a high level of vibration or a steadily increasing engine temperature, which could indicate a seal is malfunctioning. This information allows the outage team to take preventive action, such as making the necessary repairs or replacing the pump before a breakdown occurs.
Tank Monitoring Made Easy
Power plants may bring in temporary holding tanks when a cooling pond or other water source is located too far from the temporary pumps or if the plant needs to store water taken from a permanent tank being de-scaled. Telemetry that tracks water levels in these tanks provides many of the same benefits pump telemetry offers. There is no need to have someone at the tank location keeping watch over water levels. If the level starts rising too high, the system will send an alert so plant operators can take action, such as shutting off the flow or directing it to another tank before there is an overflow that spreads water across a floor filled with equipment and people. If the water levels drop too low, an alert will enable operators to adjust the flow before cooling operations are impacted, potentially avoiding an overheated system that could extend the outage.
Technology Plants Cannot Afford to Skip
Power generating plants cannot afford time-consuming equipment or system failures when performing routine or emergency maintenance. Shutdowns are generally planned for off-peak or shoulder periods, and extending an outage into a peak period could affect an entire region.
To ensure the reliability of energy production, reduce costs and remain competitive, power plants must leverage the latest digital technology, including during maintenance operations. Remote pump and tank monitoring by way of advanced telematics optimizes the productivity of skilled workers and gives plant operators greater visibility into, and therefore greater control over, the equipment and the systems it impacts. It has become a beneficial tool in a power plant’s quest for a streamlined, trouble-free outage.