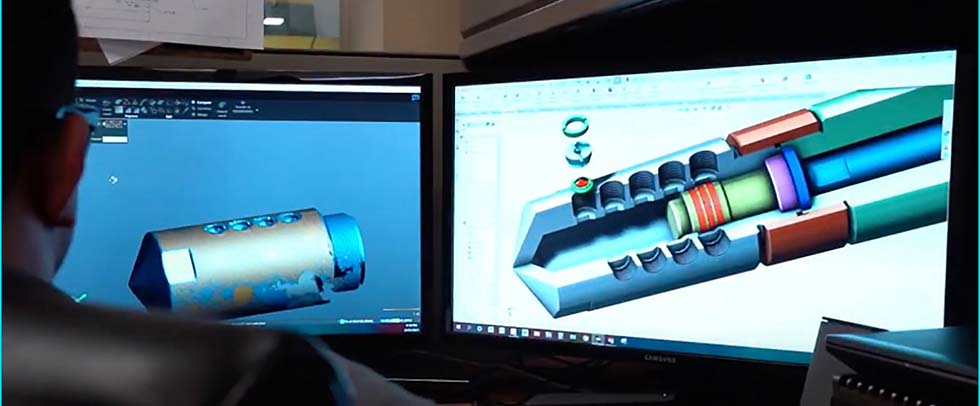
Essential infrastructure service providers, including the power and oil and gas industries, face shifting geopolitical climates, uncertain or inconsistent regulation and competition on a global scale. To maintain financial viability, facilities must navigate the operational challenges of maintaining aging equipment while running a safe and efficient plant.
Plant operators must balance sales and revenue generation against maintenance expenditures in terms of dollars and downtime. This is straightforward at the component level for a single valve or pump, but the degree of difficulty increases exponentially for complex systems such as a liquefied natural gas (LNG) liquefaction train or a combined cycle generation unit.
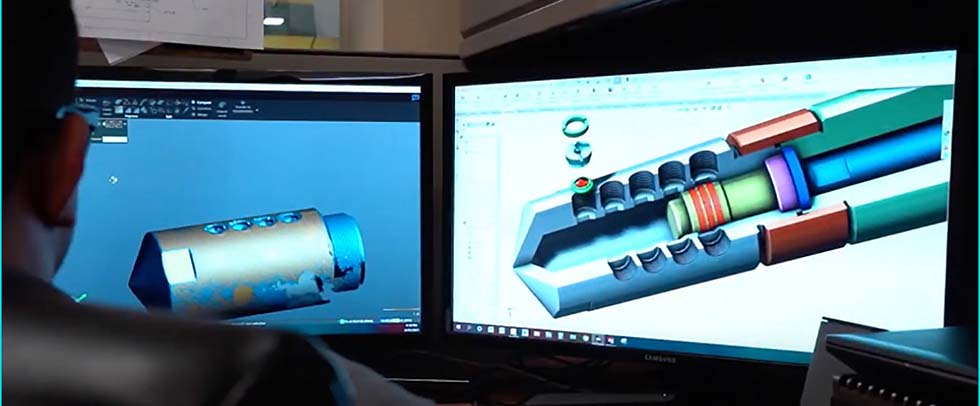
Compounding these challenges is the inescapable factor of age: as of 2017, the average age of the United States power generation fleet is 22 years for natural gas, 36 years for nuclear and 39 years for coal.1 In addition, there has not been a new refinery built with a production capacity greater than 100,000 barrels per day (bb/d) since 1977.2
Preventative maintenance on facility components includes periodic inspection, testing and repair or replacement of worn or damaged parts. There are also unplanned repair and replacement activities that can occur due to sudden component failure. When replacing or repairing worn, damaged or failed parts, the plant manager is confronted with three choices:
- Contact the OEM to repair or replace the part
- Replace the parent component of the damaged or failed part
- Use reverse engineering techniques to perform an aftermarket repair or procure an aftermarket part
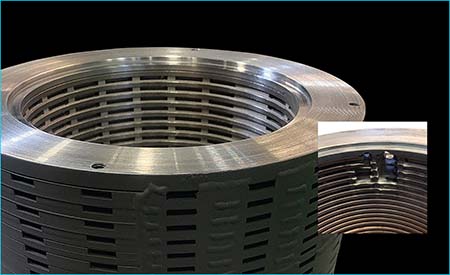
A detailed cost/benefit analysis of these paths forward is beyond the scope of this paper and is dependent on the scenario at hand, with no one-size-fits-all approach. However, in many cases, reverse engineering is a cost-effective option for procurement of long-lead, expensive or obsolete parts.
What Is Reverse Engineering?
Reverse engineering (RE) is defined as “the process of developing technical information sufficient to obtain a replacement for an item by physically examining, measuring, testing existing items, reviewing technical data, or performing engineering analysis.”3 RE has been used throughout history to examine, reproduce and improve on existing technologies.
Today, methods vary from ad-hoc testing and examination to rigorous formal treatment. Methods differ by organization and are documented in standards such as Military Handbook-115 available from the U.S. Army Corps of Engineers or in various technical publications from the Institute of Electrical and Electronics Engineers (IEEE) for software. In the power and process industry, precise guidance for RE of parts and components is given in Electric Power Research Institute (EPRI) Technical Report 107372 Rev. 1. The EPRI approach was developed for use in nuclear safety-related power plant applications. This best practice guidance holds true for fossil fuel power and oil and gas facilities.
To properly reverse engineer a part, the following steps must be performed:
- Identify the application and function of the parent component or system and the objective of the reverse engineering activity
- Identify the design characteristics of the original item for reverse engineering
- Recover known and unknown item characteristics through physical testing, document reviews and
- technical evaluation
- Establish a design for the replacement component
- Review the replacement item design against the known, recovered and inferred characteristics of the original component, including consideration for in-service and environmental conditions
- Determine if there are any disposition discrepancies between the replacement and original designs via a technical evaluation to document the replacement item’s fitness for service.
- Provide for stakeholder review and approval prior to fabrication of the replacement part
It is worth noting that the forthcoming discussion of these steps and this method is through the lens of a manufacturer and designer of ferrous and nonferrous metal components. For a full treatment of the RE process for complex systems such as software, circuit boards, etc., it is suggested the reader review applicable EPRI, IEEE or other industry guidance.
What Are the Benefits & Risks of Reverse Engineering?
Whether or not to employ RE as a way of producing obsolete parts is a question of whether to use a proven and costly OEM part against an unknown and less expensive aftermarket part. An analogy to auto parts applies here: A car can be taken to the dealership for OEM parts and service but at a premium in dollars and time. It can go to the neighborhood garage where the aftermarket brake pads will work just as well for a fraction of the price. A user can buy the “economy, daily driver or premium” level of quality where the premium part may last longer than a base model OEM part. The most typical benefits of RE are reductions in lead time and cost.
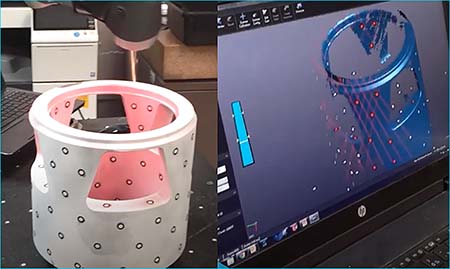
As an example of this high cost, a threaded rod ordered to an obsolete material specification would require a steel mill to produce a minimum lot size of 40,000 pound-mass (lbm) for a part that might use 40 lbm of material. Another example would be the use of castings in valve trim. If one was to order a casting to the original print, it is possible that the casting pattern or vendor no longer exists. In this scenario, the casting vendor would have to create a new mold and pour a batch of material that they may not typically work with.
In these instances, the OEM would quote a high unit cost and long lead time to account for these challenges in working with an obsolete material. This is a common problem; the geometry and application of the part are not obsolete, but the material or manufacturing method used is. This can be overcome with sound engineering principles and by offering an available material. Therein also lies one of the risks of RE and, by definition, this would be a design change. If not properly evaluated with appropriate technical rigor, the replacement component performance may not be equivalent to the OEM.
Reverse Engineering vs. Design Equivalency
For a component to be successfully reverse engineered it must be “like for like” with no changes from the original part. For ferrous and nonferrous metal parts, this includes all dimensional characteristics and material properties such as chemical composition, mechanical strength and others. All of this information can be known with enough time and samples for laboratory testing, but this is not always practical with compressed schedules and limited budgets.
For a part to be a true “like for like,” all design characteristics must be known and recoverable by using the proper equipment. For example, the outer diameter of a valve plug is a critical dimension. Should the recovered dimension be too large, the plug will not fit the cage. Should the diameter be too small, the plug will not maintain alignment within the cage and a fluid leak will occur that will alter the valve’s flow characteristics.
In this application, typical clearances between the cage/plug interface are 0.002 inches to 0.003 inches, which would then require the remanufactured plug to have an outside diameter (OD) of ± 0.001 inches from the recovered dimension. If the plug OD was recovered with a tape measure with a tolerance of ± 1/32-inch, this would be an unknown characteristic given the manufacturing tolerances required and the poor accuracy of the measurement. However, when measured with laser scanning equipment with tolerances of ± 0.0005 inches, this dimension can be definitively known when taking into account the required manufacturing tolerance of ± 0.001 inches on the OD.
It is sometimes argued that dimensional characteristics cannot truly be known unless the OEM tolerances are known. This statement is inaccurate in that it dismisses the maturity and standardization of sound machining practices. For example, the “bible” for computer numerical control (CNC) machining, Machineries Handbook3, has been in print for over 100 years and has defined tight tolerances, interference fits and assembly clearances for generations. The same tolerances specified by the OEM are the tolerances that providers manufacture to. In addition, there have been improvements in CNC machining over the years, and the tolerances that were intended for manual machining 30 years ago can be reliably attained with less variation on a modern CNC.
In some cases, characteristics cannot be recovered by measurement but must be inferred using what data is available and sound engineering principles. For example, material data is typically ascertained by using X-ray fluorescence positive material identification (PMI) technology to recover chemical composition and nondestructive hardness testing for material tensile strength. PMI technology can recover the unified numbering system (UNS) chemical composition for the alloy and stainless steels typically used in valve trim, but it cannot recover the material specification—such as American Society for Testing and Materials (ASTM), the German Institute for Standardization (DIN), Aerospace Material Specifications (AMS), or the Society for Automotive Engineers (SAE)—to which it was manufactured. Sometimes this can be recovered from a packing list or other documentation but is usually not available. A practical example of this would be determining whether or not a cast or forged material was used in the manufacture of a valve cage.
Cast or Forged?
UNS J91540 is a commonly used martensitic stainless steel casting material covered by four ASTM specifications and is referred to as CA6NM. It is nearly identical in chemical composition to the forging UNS 41500 covered by an additional 10 ASTM specifications. The differences in chemistry are minor and are due to the differences between manufacturing a cast versus forged material. There are also ASTM documents that state the materials are equivalent. Both casting and forging are supplied equivalent tensile strengths depending on the final heat treatment, and the required tensile strength can be recovered from a hardness test.
Ultimately, whether or not the original material of manufacture is a casting or forged, it may not be able to be recovered. Therefore, if the original material specification cannot be ascertained, a true “like for like” part cannot be supplied. However, if UNS J91540 and UNS 41500 can be considered equivalent materials, the “form, fit and function” of the replacement part will be identical to the original.
Maintenance cost pressures, long lead times and part obsolescence are not going away. With advances in metrology, manufacturing and methods, reverse engineering is a reliable and cost-effective way of dealing with these challenges.
References
Kwon, Augustine “Natural Gas Generators Make Up the Largest Share of Overall US Generation Capacity”, 12/18/2017, www.eia.gov/todayinenergy/detail.php?id=34172
“When Was the Last Refinery Built in the United States?”, Last updated June 23rd, 2020, www.eia.gov/tools/faqs/faq.php?id=29&t=6
Guidance for the Use of Reverse-Engineering Techniques: Revision 1 to EPRI TR-107372. EPRI, Palo Alto, CA: 2018.3002011678
Oberg, Erik, 2020, Machineries Handbook, Industrial Press Inc.