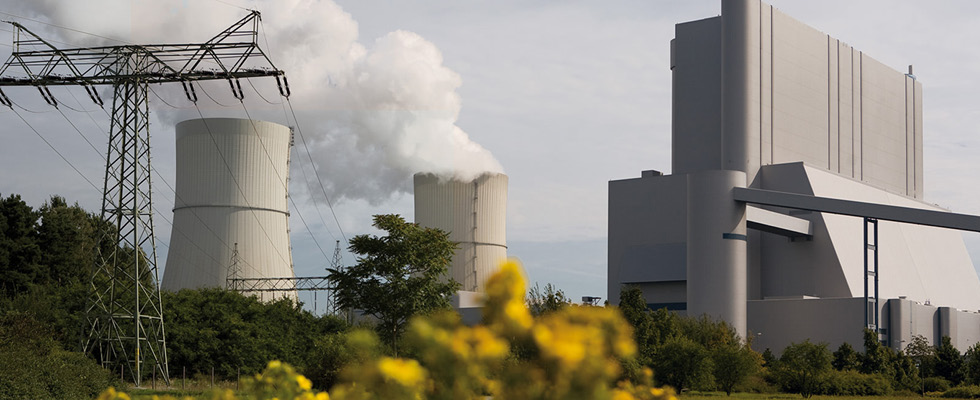
An in-depth look at the applications, advantages and types of compressors used in power generation.
Atlas Copco
07/17/2025
A critical component in power generation systems is the air compressor, which facilitates various operations in power plants. These machines convert power into potential energy stored in compressed air, which is then used to support essential processes in power generation.
Applications
- Instrument air systems: Compressed air is essential for operating pneumatic tools and control systems, such as actuators and valves. These systems rely on a steady supply of compressed air to function precisely and consistently, ensuring the safe and efficient operation of the power plant.
- Turbine startup and purging: In gas and steam turbine power plants, compressed air is used for purging systems to remove moisture and contaminants before the startup process. This ensures that turbines operate under optimal conditions, reducing the risk of damage or inefficiencies.
- Ash handling systems: In coal-fired power plants, compressed air is utilized in ash handling systems to convey fly ash from the combustion chamber to storage silos, minimizing environmental impact and improving operational cleanliness.
- Fuel atomization: For power plants using liquid fuels, compressed air aids in the atomization process, ensuring a fine spray of fuel for efficient combustion.
- Cooling and cleaning: Compressed air is often used for cooling components and cleaning equipment, particularly in environments where maintaining cleanliness and temperature control is crucial to performance and safety.
- Maintenance support: Power plants rely on compressed air to power pneumatic tools for maintenance tasks. This streamlines operations, reduces downtime and ensures that equipment remains in optimal working condition.
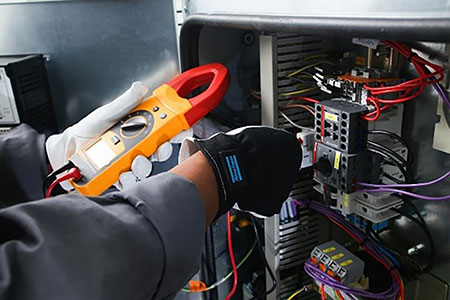
Advantages
- Improved operational efficiency: Air compressors ensure critical systems operate smoothly and efficiently. By supplying high-quality compressed air to control systems and turbines, power plants can maintain precise and consistent performance, reducing energy waste and optimizing output.
- Enhanced reliability: Modern air compressors are designed for durability and reliability. Their robust construction and advanced technology minimize the risk of breakdowns, ensuring uninterrupted operation of essential power generation processes.
- Energy savings: Many air compressors feature energy-efficient designs, such as variable speed drives (VSDs), which adjust air output to match demand. This reduces energy consumption and lowers operational costs.
- Reduced environmental impact: By optimizing fuel combustion and enabling effective ash handling, air compressors contribute to reduced emissions and cleaner operations. This aligns with industry goals to minimize environmental impact and comply with stringent regulations.
- Customizable solutions: Air compressors come in various types and capacities, allowing power plants to select equipment tailored to their specific needs.
- Simplified maintenance: Advanced air compressors are designed with maintenance in mind, featuring user-friendly interfaces and accessible components. This reduces downtime and maintenance costs.
Types
- Centrifugal compressors: These high-capacity compressors are ideal for large-scale operations. They deliver a continuous flow of compressed air, making them suitable for instrument air systems and turbine applications.
- Rotary screw compressors: Known for their efficiency and reliability, rotary screw compressors are commonly used in power plants for a range of tasks, from operating pneumatic tools to supporting control systems.
- Reciprocating compressors: These are well-suited for applications requiring high-pressure air. They are often used in smaller power plants or specific tasks like fuel atomization.
- Oil-free compressors: These compressors provide high-quality compressed air without the risk of contamination.
Considerations
- Capacity and demand: Power plants must assess their compressed air requirements to select equipment that meets current and future needs. Oversized or undersized compressors can lead to inefficiencies and increased costs.
- Energy efficiency: Choosing energy-efficient compressors with features like VSDs can reduce energy consumption and operational expenses.
- System monitoring and control: Advanced monitoring systems allow operators to track compressor performance, identify potential issues and optimize operations in real time.
- Maintenance planning: Implementing a proactive maintenance schedule minimizes downtime and prevents unexpected failures. Maintenance practices can include filter changes, lubrication, performance monetization and a component check.