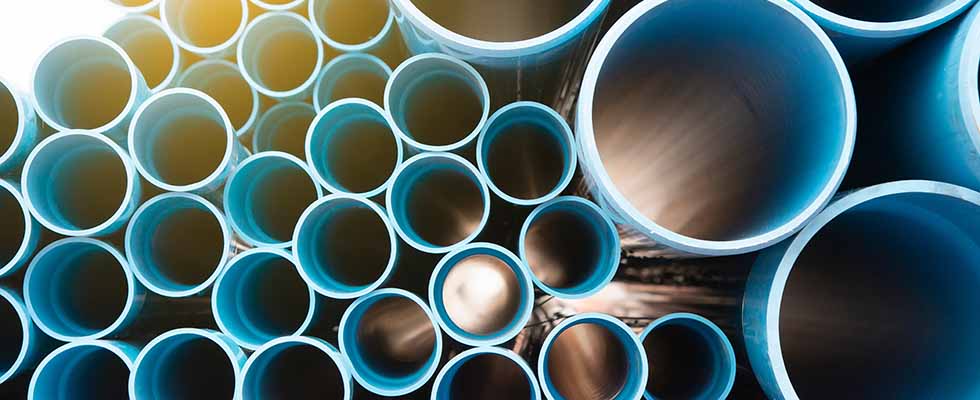
As the use of nonmetallic piping systems becomes more prevalent, the demand for gaskets that can seal effectively at low loads continues to rise. Nonmetallic piping systems offer numerous benefits and are increasingly popular across industries such as potable water, semiconductors and hydrogen. Conventional fiber, polytetrafluoroethylene (PTFE) and metallic gaskets have historically been designed for use in metallic flanges, where the amount of compressive stress available is significantly higher than that of nonmetallic or plastic flanges. Emerging gasket technologies have been specifically designed to adapt to this evolving landscape, enabling the creation of robust, chemically resistant seals even with limited load capacities. These advancements ensure that nonmetallic piping systems can maintain their integrity and performance, meeting the growing industry demands for reliable and efficient sealing solutions.
Nonmetallic piping systems like polyvinyl chloride (PVC), chlorinated polyvinyl chloride (CPVC), fiberglass reinforced plastic (FRP) and high-density polyethylene (HDPE) offer various benefits, including lower cost, lighter weight, improved corrosion resistance and easier installation compared to their metallic counterparts. These advantages can come at a cost, though, namely reduced system pressures or lower allowable torque/gasket assembly stress. Plastic flanges often have torque limitations, as the compressive forces generated by steel fasteners can damage the flanges if not controlled.
In addition, nonmetallic flanges must be flat face designs, as raised faces would create bending moments that could crack the brittle material. Full face gaskets have a much larger surface area compared to ring gaskets, so the compressive force generated is spread out over a much larger area, which results in much lower overall gasket stress. The gasket stress is reduced further due to the low allowable torque that must be followed to avoid compromising the structural integrity of the flanges.
Because of this, nonmetallic flanges have traditionally been sealed with simple rubber gaskets, which have possible drawbacks. Elastomeric materials can degrade over time and may not be suitable for critical service chemicals. Traditional elastomeric material also may not meet purity requirements for applications like ultra-pure water found in the semiconductor and hydrogen industries. They can also lose load over time, especially with plastic flanges that are prone to creep. As application requirements become more demanding, the need for more advanced sealing solutions increases. However, the limitations on compressive forces may make it difficult to utilize conventional means of sealing these flanges with traditional PTFE or other flat gaskets materials that require a significant amount of gasket stress.
Compressive stress can be broken down into two components: the magnitude of the force and the area over which it is applied. As mentioned earlier, nonmetallic systems can be especially tricky, as flanges are often flat face, requiring a full-face gasket, which has a significant amount of surface area. Since the force is limited by the material properties of the flanges, it is necessary to look at reducing the contact area of the gasket to maximize the available stress.
One method would be to utilize stress concentration points on the gasket itself. This would reduce the contact area between the flange and the gasket to a much smaller size, allowing the force to be concentrated. Such stress concentration points can take a variety of forms, such as concentric rings that are molded into the gasket themselves. These would create strategic areas of stress concentration surrounding the inner diameter of the flange, preventing a leak path from connecting to the outer edge. Such a method would allow high-purity PTFE gaskets to be used in potable water and even the ultra-pure water applications found in the semiconductor and hydrogen industries. The limitation of this technique is that these gaskets require expensive molds, so the available sizes are limited to standard flange sizes that have existing molds.
While a technique like this may be suitable for PVC or CPVC flanges, which are made to standard dimensions, there are often applications that need more flexibility. Nonstandard flanges or applications such as manway gaskets may require a solution that does not rely on having molds created for a specific size. Traditionally, gasket sheet material has been used since it can be cut to the exact dimensions required. To accommodate these applications, solutions such as profiled PTFE gasket sheet material can be used to harness the benefits of stress concentration points while retaining the ability to be cut to custom shapes. This is especially useful for FRP tanks or other manways with thin flanges that limit the amount of torque that can be applied.
Profiled PTFE gaskets offer other benefits as well. Concentrating stress in smaller peaks throughout the gasket allows for more even force distribution and avoids generating bending moments in the assembly. Conventional flat gaskets tend to concentrate the compressive force to the areas directly around the fasteners. Limiting the contact area increases the compressibility of the gasket, allowing the force to spread out more evenly. This also allows such a gasket to functionally seal worn out or pitted flanges that have an irregular sealing surface.
The evolution of gasket technology is crucial to the continued success and reliability of nonmetallic piping systems. By utilizing advanced materials and design techniques such as stress concentration points and profiled PTFE gasket sheet material, engineers can ensure that even the most demanding low-load applications are met with robust, chemically resistant seals. This not only enhances the capabilities of nonmetallic systems but also supports the growing demands of critical industries that rely on these advanced technologies.