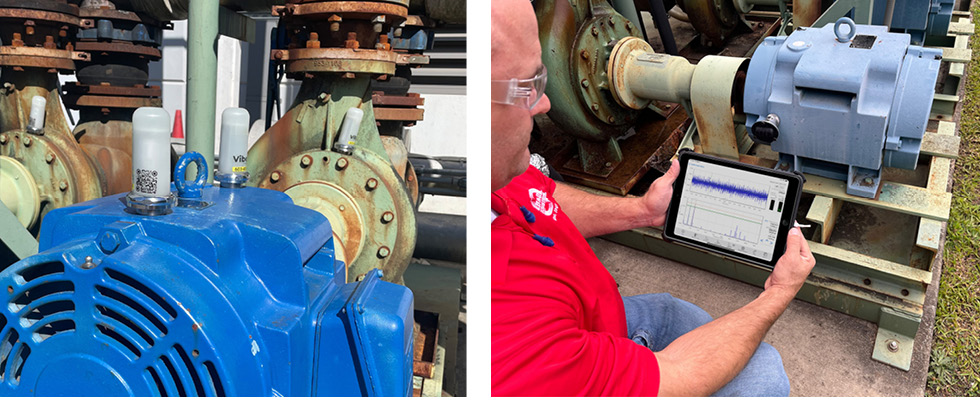
Unplanned downtime can significantly impact a company’s bottom line. It leads to wasted resources, delivery delays and, ultimately, unhappy users and thinner profit margins.
Thankfully, it is avoidable. This is where predictive maintenance comes in, offering a proactive approach to equipment maintenance that can save both time and money. At the heart of every modern predictive maintenance program are machine analysis tools. This article will explore predictive maintenance, its key components, its history and the technology that fuels it.
While predictive maintenance can be used on many types of equipment, it is particularly effective for rotating machinery such as pumps, air coolers, mixers, compressors, turbines, motors, spindles, gearboxes and others. These machines play critical roles in production processes, making their reliability essential.
Understanding Predictive Maintenance
Predictive maintenance uses data-driven insights to predict when equipment is likely to fail, allowing maintenance to be performed before it is needed. This approach offers several advantages over traditional maintenance methods:
- Reduced downtime
- Lower maintenance costs
- Extended equipment lifespan
- Improved safety
- Decreased need for replacements
The value of predictive maintenance lies in its ability to prevent unexpected failures, optimize maintenance schedules and maximize equipment performance and efficiency.
Components of a Predictive Maintenance Program
A comprehensive predictive maintenance program consists of several key components, including the maintenance plan, skilled personnel and, most importantly, the hardware and software that collect data and make it available for analysis.
Maintenance plan: This strategic plan outlines goals, procedures, responsibilities and scheduling. A list of equipment in order of most to least critical provides a good road map on which equipment to focus on first.
Hardware: This is comprised of sensors and data collection devices.
Software: This includes advanced analytics platforms that process and interpret the machine data.
Skilled personnel/partners: These are the trained technicians and analysts who implement the program, analyze data and determine required actions in response to what is uncovered. Companies have the option to contract out analysis services or to perform them in-house. Working with a reliable third-party allows companies—typically smaller to mid-sized ones and sometimes larger ones—access to talent and ability to scale without having to employ technicians full time.
Tools & Functions
Various tools and sensors are employed in predictive maintenance, each focusing on its own set of parameters to assess equipment health. Image 1 outlines the key components and their roles within the system.
Approaches to Data Collection
There are two primary approaches to implementing predictive maintenance: route-based and permanent solutions.
With route-based, technicians periodically collect data using portable devices, following predetermined routes to equipment throughout the facility. This method is flexible but labor-intensive. With permanent solutions, sensors are installed on critical equipment, providing continuous monitoring. While more expensive initially, this offers real-time insights and is often more cost-effective in the long run. The choice between these approaches depends on factors such as equipment criticality, budget constraints and available resources.
Historical Context: From Preventive to Predictive Maintenance
To fully appreciate the value of predictive maintenance, it is helpful to understand its evolution. Traditionally, maintenance was performed on a fixed schedule, regardless of the equipment’s actual condition. This approach, while better than reactive maintenance, often led to unnecessary maintenance activities and did not prevent all unexpected failures.
As technology evolved, so did predictive maintenance. By leveraging data and advanced analytics, predictive maintenance allows for more precise and timely interventions. This shift from time-based to condition-based maintenance represents a significant advancement in asset management strategies.
The Impact of Technology
Predictive maintenance in its present form could not exist without many advances in technology. The Internet of Things (IoT) allows for deployment of connected sensors. Big data analytics provide the ability to process and interpret vast amounts of data. Cloud computing provides scalable storage and processing, with on-demand access worldwide. These technologies have transformed maintenance from a reactive necessity to a proactive strategy that contributes to overall operational excellence.
Implementation Challenges
While the benefits of predictive maintenance are clear, some organizations find it difficult to implement programs of this kind. The most common barrier is the initial investment required for sensors, software and training. Companies must weigh these costs against the long-term decrease in downtime and maintenance expenses. Fortunately, the evolution of cloud-based solutions and scalable sensor networks has made predictive maintenance less expensive than ever before, making it possible for companies of any size to roll out these strategies incrementally.
Another problem is data management. Predictive maintenance generates vast amounts of data that must be stored, analyzed and interpreted correctly. If firms lack analytics capabilities, they may not be able to immediately derive actionable insights. This hurdle can be cleared by either investing in training or partnering with a company that provides analytics
as a service.
Finally, organizational cultural resistance may also inhibit adoption. The transition from traditional maintenance practices to a data-driven approach requires leadership commitment and staff training. Employees should be trained on the benefits of predictive maintenance and shown real-world success stories to help drive adoption and enable a smooth transition process.
Looking to the Future
Machine analysis tools play a central role in modern predictive maintenance programs. By providing insights into equipment health and performance, these tools enable manufacturers to move from reactive to proactive maintenance strategies. As technology continues to advance, so will the capabilities of predictive maintenance, offering even greater potential for operational efficiency and cost savings.
Embracing predictive maintenance and investing in the right machine analysis tools can give organizations a competitive edge in today’s data-driven industrial landscape. As the industry looks to the future, the integration of artificial intelligence and machine learning promises to make predictive maintenance even more powerful, paving the way for truly smart factories and highly optimized operations.