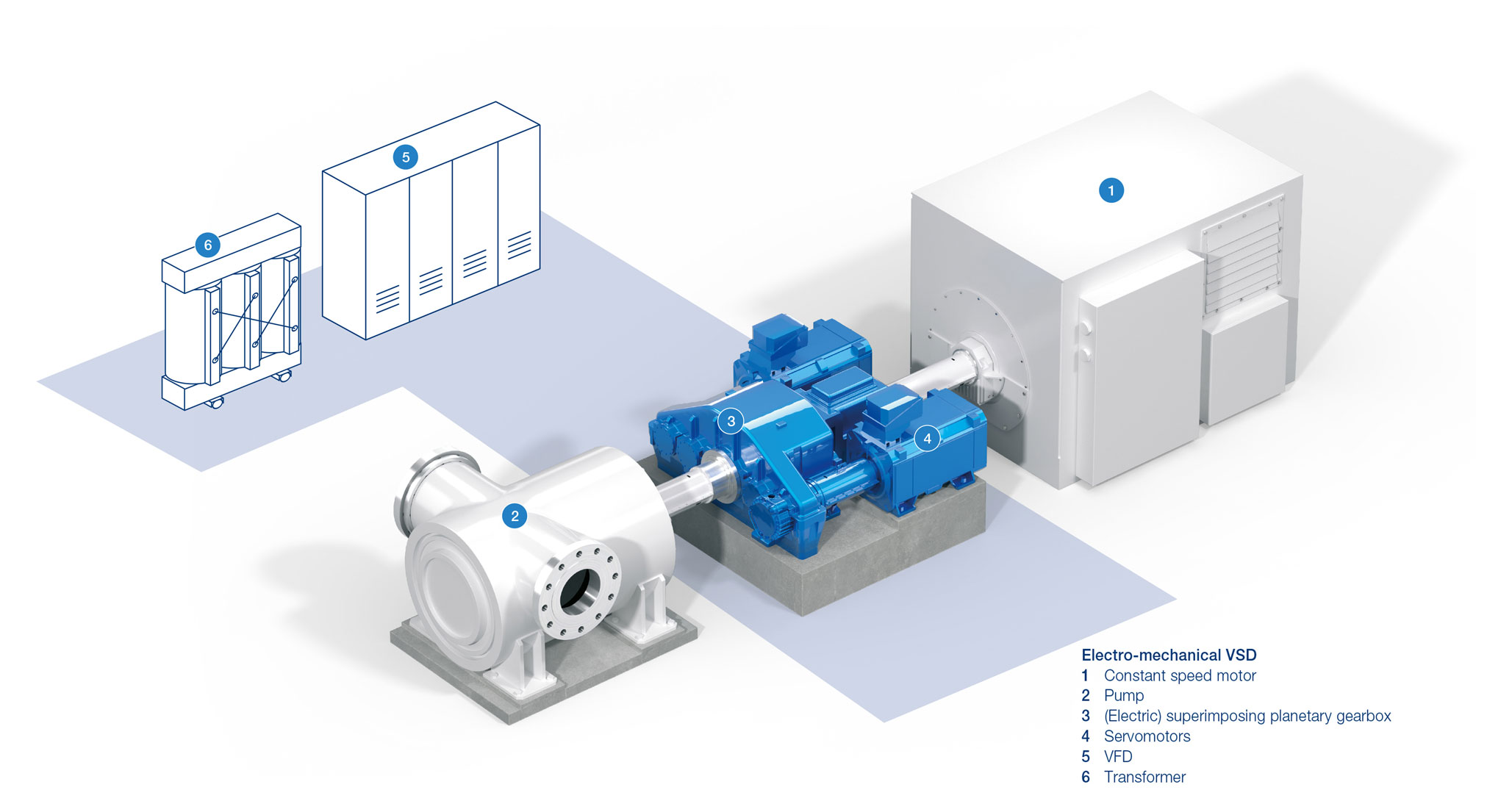
The oil and gas, chemical and energy sectors use many high-power, high-speed pumps in various applications, often being driven by large electric motors that consume a considerable amount of plant energy.
Within these sectors, trends and requirements are ever-changing, and one topic of interest is improving plant efficiency to save energy and operating costs over short- and long-term periods.
This needs to be done without compromising availability and reliability. An important global goal for these sectors is to support decarbonization and reduce greenhouse gas emissions in line with the Paris Agreement. New technologies are needed to support this goal.
When electric motor-driven variable speed regulation is needed on high-power, high-speed pumps in a typical speed range of 50% to 100%, an electromechanical variable speed drive (VSD) could be considered. These VSDs operate with power ratings up to 20 megawatts (MW) and 15,000 rotations per minute (rpm) rated output speeds. An electromechanical VSD supports the interest to improve plant efficiencies, save energy and support decarbonization.
Intro to Electromechanical VSD
Traditionally, three VSD options could be used to provide variable speed regulation for pumps when driven by large electric motors:
- Hydrodynamic fluid coupling, with or without gear stage(s)
- Hydrodynamic controlled superimposing planetary gear
- Full-scale variable frequency drives (VFDs) with or without a step-up gear
The electromechanical VSD is a recent technology that combines the superimposing planetary gear with VFD technologies and incorporates a concept called the power split principle. The drive layout consists of a constant speed main motor, which is directly coupled to a superimposing planetary gearbox, which is then coupled to the driven pump. Two control servomotors are then connected to the superimposing planetary gearbox, creating an electric superimposing planetary gearbox. The pump speed can then be regulated together with the electric superimposing gearbox plus the constant input speed from the main motor. A VFD provides the control needed for the two servomotors. The layout of the electromechanical VSD solution is shown in Image 2.
Variable Speed Regulation via Electrical Superimposing Planetary Gearbox
The diagram shown in Image 3 details how the electrical components are connected to the mechanical gearbox that provides the variable speed regulation. The constant speed motor (1) drives the input shaft, (2) which drives the ring gear on the planetary gearbox at a constant speed (3). The sun gear (4) is then connected to the output shaft (6), which provides variable speed for the pump. The servomotors (7) are connected to the planet gears (5) by the planet carrier (8). The sun gear is orbited by the planet gears, which are enclosed by the ring gear. The servomotors are operating in clockwise and anticlockwise directions, which change the direction and speed of the planet gears, allowing the speed of the pump to be increased or decreased across the 50% to 100% operating range.
Electromechanical VSD Using the Power Split Principle
Electromechanical VSDs use two power flows to provide the required power for the driven pump. At rated point, the constant speed main motor will typically provide 85% of power to the pump and the remaining 15% power will be provided by the VFD and servomotors, which is the power needed for providing the variable speed regulation. This is called the power split principle.
When compared to one of the previously mentioned VSD options, full scale VFD, 100% power is provided by the VFD and variable speed motor to provide variable speed regulation. As the full-scale VFD system components are installed in-line, they are transmitting full power, meaning the losses are subjected to the full power flow. The power flow of the two technologies is shown in Image 4.
As the electromechanical VSD solution only uses 15% of control power for variable speed regulation, this means VFD losses are proportional only to 15% of power instead of 100% of the power. When calculating the drive train efficiency provided by an electromechanical VSD, the formula in Equation 1 can be applied, which takes into account the power split principle and uses the 15% and 85% power flows within the calculation.
The electromechanical VSD system, therefore, achieves high efficiency across the pump operating range due to only a small portion of power flowing through the VFD line and the majority of power is transmitted purely mechanically. At rated point, efficiencies of up to 97% are possible, which can result in efficiency gains of up to 2.5% when compared to full scale VFD (Image 5). The electromechanical VSD using a small amount of power for control means the VFD has a small footprint and there are savings in weight. Also, there are savings in auxiliaries such as power savings for cooling, the transformer is simplified and the constant speed main motor footprint is reduced from the possibility of derating by around 15% to 20%.
The electromechanical VSD can provide the highest efficiency drive solution using the power split principle, which can contribute to improved plant efficiencies, save energy and support decarbonization on new build projects or upgrade projects in existing facilities. The energy savings and reduced control power may also contribute to total cost of ownership savings up to typical 25-year periods.
Aside from high efficiency, electromechanical VSDs may also offer further support when driving high-power, high-speed pumps including:
- Motor-assisted start option that protects the grid from high inrush currents. The two servomotors can be used to start up the constant speed main motor before connecting to the grid.
- Various electric topologies can be applied to provide different redundant options, especially for critical process pumps. The two servomotors also provide redundancy, allowing the drive train to continue to run in an emergency operating mode in case of an unlikely issue with one of the servomotors.
There are many solutions for providing variable speed regulation when powered by large electric motors, so it should be noted that VSD technology should always be selected per individual project requirement, location and type of industry. Therefore, early evaluations are always recommended to define the best VSD for each pump application.