The technology offers a lower cost of ownership, reduced maintenance needs and a longer service life than some conventional plunger pumps.
Wanner Engineering
10/06/2016
In the oil and gas exploration business—as with most every other industry—downtime is money down the drain. When a company is routinely pumping thousands of gallons of oil in a remote oil field, an unplanned break in production can be costly. Saltwater is a natural byproduct of oil exploration, and it must be properly disposed of once it is separated from the oil. Typically, it is pumped back into the ground by way of disposal wells, using plunger pumps requiring 500 to 700 pounds per square inch (psi) of pressure. But saltwater and the contaminants it contains are corrosive and, when carried through pipes at high pressure, can erode seals, causing them to leak, clog or fail.
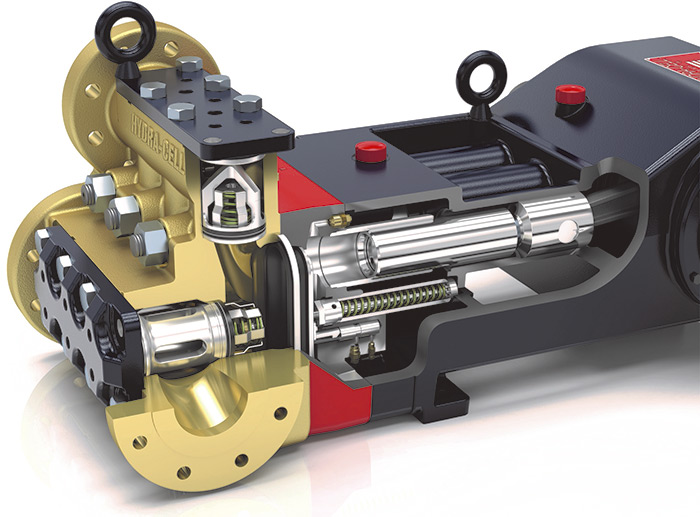
High Cost of Breakdowns
Silver Oak Energy, an oil and gas exploration and production company based in Silsbee, Texas, has dealt with issues typical to its industry. In this case, it involves legacy pumps that frequently experience problems because of reliability issues, most notably plungers with packing that can dry out, crack, clog or leak, particularly if the pipes run dry. “Most complex pumps have an open plunger, so whatever you’re sending through, such as saltwater, will leak through the packing,” said Robert Clark, production foreman at Silver Oak. “We experience breakdowns, on average, every six weeks. We spend thousands of dollars each year sending mechanics out to the sites to fix the pumps—and that doesn’t include the money lost due to the slowdown or shutdown.” J-W Operating Company, an exploration and production company based in Dallas, Texas, has experienced similar issues at its more than 400 natural gas and 13 injection wells. “With the standard metal rod pumps, there’s a lot of metal-on-metal grating, which causes wear and tear to occur fairly quickly,” said James Barber, production foreman for J-W Operating, which is a subsidiary of J-W Energy. “They break frequently, meaning we have to stop production, find the problem and fix it. That gets costly and, of course, slows down production.” Both companies were asked to test a new product: a sealless pump. With flow rates up to 96 gallons per minute (3,300 barrels per day, 366.1 liters per minute) at pressures up to 1,500 psi (103 bar), the pump model could be ideal for a variety of applications, including saltwater disposal or injection, bulk transfer, hydraulic lift and steam generation.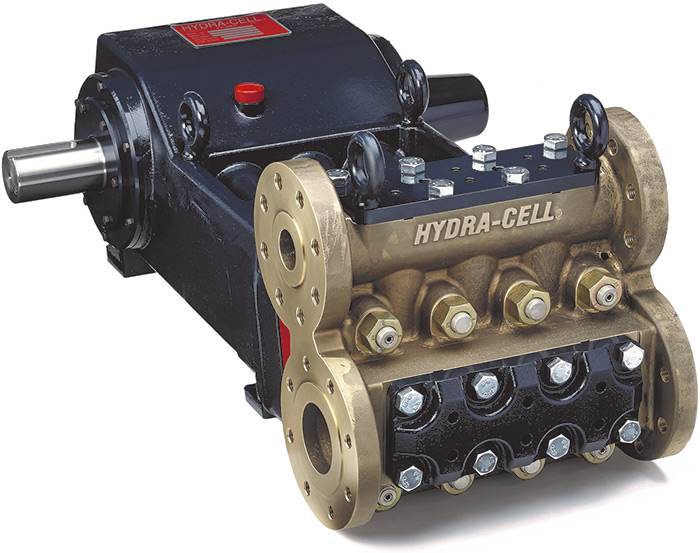
Sealless Vs. Plunger Pumps
This particular sealless pump differs from plunger pumps in several ways. The selected pump features a unique, patented technology that utilizes a sealless multiple-diaphragm design that keeps the pumped liquid 100 percent contained, eliminating leakages, cleanup and disposal costs commonly associated with packed plunger pumps. The innovative design also eliminates the need for external lubrication and maintenance, as well as plunger wear problems associated with packing. The pump is also packing-free and designed to replace horizontal centrifugal pumps and packed plunger pumps in oil and gas applications. Benefits of the pump include:- zero leakage because the sealless design separates the power end from the process end
- elimination of hazardous volatile organic compounds (VOC) emissions
- reduced cleanup and disposal costs associated with packed-pump leakage
- hydraulically balanced diaphragms handling high pressure with low stress
- virtually pulse-free, linear flow with the multiple-diaphragm design
- operation with a closed or blocked suction line and the ability to run dry indefinitely without damage to the pump
- abrasives handling capabilities—particles up to 800 microns in size can pass through the pump
- no requirement for positive inlet pressure because low net positive suction head requirements allow for operation with a vacuum condition on the suction
- reduced energy costs compared with other types of pumps
- compact design and a double-ended shaft providing a variety of installation options
- rugged construction contributing to a long service life with minimal maintenance