A municipality will use various applications throughout the wastewater treatment process—from headworks, to primary and secondary treatment, to sludge processing and general pumping. In order to operate, each process requires a power source. How users choose to connect those applications can vary based on preference and operating conditions.
Selecting the right coupling type for an application can increase equipment performance and reliability, reduce maintenance costs and minimize downtime.
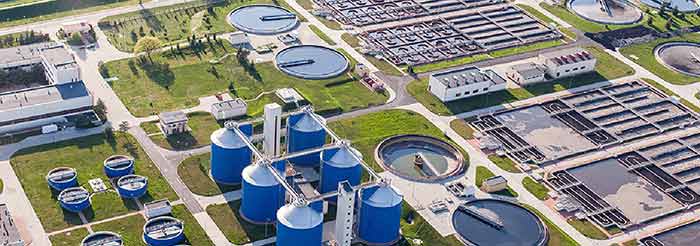
What Are Couplings & How Are They Used?
Couplings are designed to connect two shafts and transmit torque in a rotary motion from one piece of equipment to another. Based on the wide variety of styles, couplings can perform secondary functions such as accommodating misalignment between the driving and driven shafts, vibration dampening, absorption of shock loads, allowing for soft start applications, and protecting equipment from torque overload. Some variations offer spacers for applications where equipment cannot be moved.
Couplings are categorized in two groups usually referred to as elastomeric and metallic, and further categorized as flexible and rigid.
All elastomeric-style couplings are flexible to some degree. This coupling style typically uses a rubber, urethane or other composite material to transmit torque. The advantage of elastomeric-style couplings is that they can handle high vibration and shock load dampening. This makes elastomeric couplings popular in pumping, compressor and agitator applications where high vibration is common. Their misalignment capabilities make them viable for applications that are not capable of precision alignment. They are designed to align easily and require no lubrication for a maintenance-free design. They also tend to be less costly.
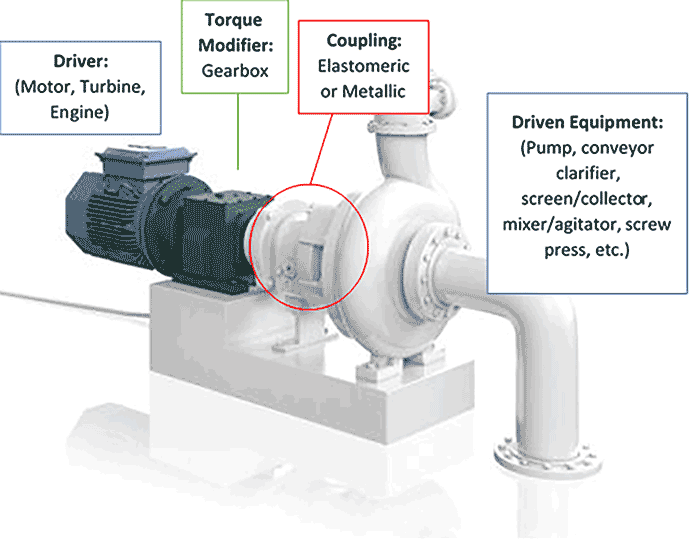
Elastomeric-style couplings can be categorized into two types: compression or shear. Couplings that operate in compression are also a fail-safe design, where even though the element should fail, the hubs come into contact and can continue to transmit torque (example: jaw couplings). Couplings that operate in shear will not transmit torque once the element fails.
Elastomeric Coupling Material: Urethane vs. Rubber
One concern in a wastewater treatment environment is water. There can be a lot of water ingress and exposure that affects how a coupling operates. Elastomeric-style couplings are commonly found in many wastewater applications. Understanding the material used can extend the equipment life in these tough applications. Urethane, for instance, tends to absorb water while natural rubber repels it.
This impacts performance of coupling elements that are used in a coupling assembly.


Hysteresis is a disadvantage found in urethane and rubber couplings. Hysteresis in urethane occurs when the material absorbs torsional vibration from high-frequency pulsations. In dampening these vibrations, it converts the energy to heat. If the frequency is high enough, the urethane cannot dissipate the heat fast enough, and the urethane temperature continues to rise until it melts. Hysteresis also occurs in rubber, but due to its chemical makeup, higher levels of conductivity and temperature capabilities, it is more efficient at dissipating heat. When the effects of vibration are high enough, however, rubber will begin to locally revert toward its initial natural properties prior to vulcanization. The result is a soft and/or tacky rubber material.1
Other considerations in material could include the hub and shaft material being used; some may specify stainless steel to minimize rusting and corrosion. This will make it easier to replace or conduct maintenance on couplings.
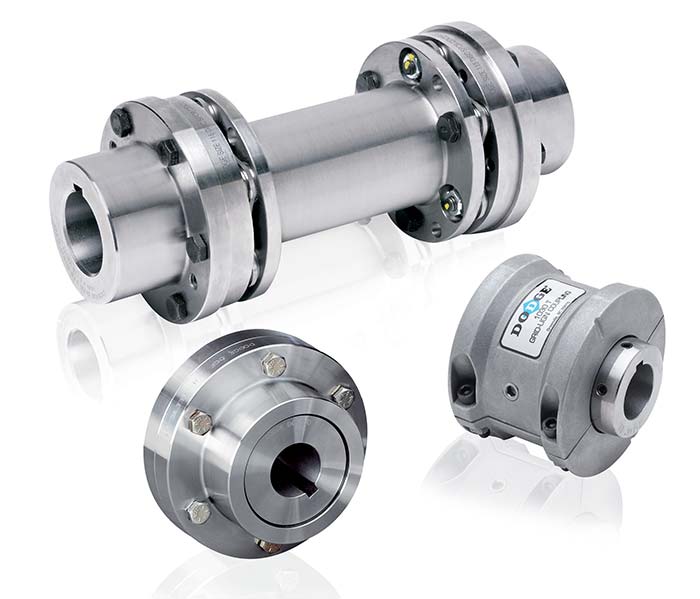
Metallic-style couplings are more compact and can handle higher speeds. Because they are metallic, this style of coupling can be balanced for increased equipment life in high-speed applications. Metallic-style couplings can be categorized into two types: lubricated and nonlubricated designs. The lubricated designs can handle some misalignment (example: chain, grid or gear couplings) while the nonlubricated designs cannot handle any misalignment (example: rigid couplings).
Coupling Selection
When evaluating an application’s ratings to perform a selection, six primary criteria should be examined:
- torque
- speed
- shaft sizes
- type of application
- distance between the driver and driven shafts
- type of driver
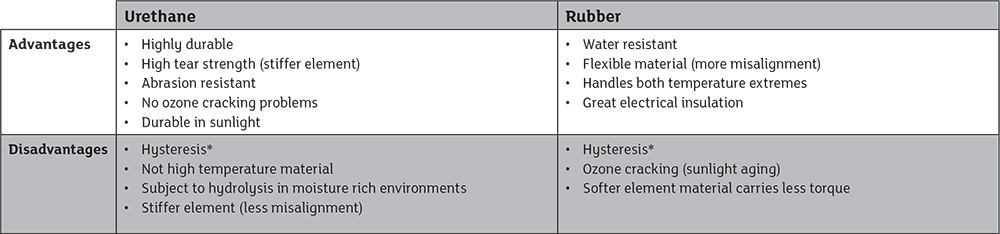
Other criteria to take into consideration:
- equipment history
- misalignment capability
- temperature
- chemical exposure
- orientation
- frequent starts, reversing
- shock loads
- space constraints
With an application’s equipment ratings and details, based on the above criteria, a style of coupling is selected. The size of the coupling is determined by a service factor.
A service factor is a multiplier applied to a nominal torque rating to account for starting torques, shocks, vibrations and other wear factors. Additional service factors are added for harsh startups, oscillating torque, continuous vibration and, in some elastomeric styles, high temperatures.
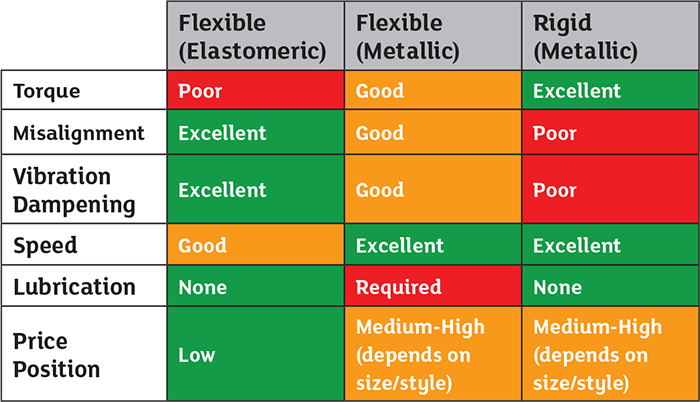
Wastewater treatment facilities have several applications that couplings are used on. Screening and multichannel oxidation ditches are examples that require specific application considerations. During the filtering process, screens can become clogged with excess material such as rags, paper, plastics and metals. For the process to be efficient, the excess material must be removed. Processes used to remove the material can cause shock loads to the shafts and couplings. Elastomeric-style couplings are commonly used in these applications because they can handle higher shock loads.
Due to the large size of multichannel oxidation ditches, mixer and aeration equipment perform over larger areas. With this, application alignment becomes harder to achieve, resulting in equipment usage that has high misalignment capabilities. To avoid additional operational costs due to inefficient equipment performance, equipment optimization is key when breaking down organic matter. With high misalignment capabilities, elastomeric-style couplings are a preferred choice for multichannel oxidation ditches.
Selecting the best coupling style can provide longer life not only for the coupling, but also the driver and connected equipment. Longer life equates to lower maintenance costs.
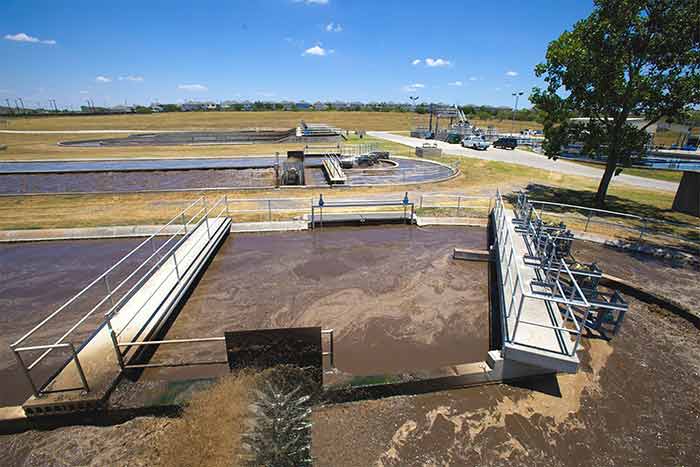
The water/wastewater industry faces numerous challenges, including aging infrastructure, population demands and impending regulations. Selecting a supplier partner with products and technical expertise to assist with application review and proper equipment selections can help a
wastewater treatment plant maintain, expand and/or upgrade their facilities.
Safety
All couplings, regardless of application, should be guarded with a coupling guard. These guards are not meant to keep contaminates out or act as a scatter-shield for the coupling if it were to fail, but to keep the operator safe from injury.
Proper personal protection equipment (PPE) is required when on-site.
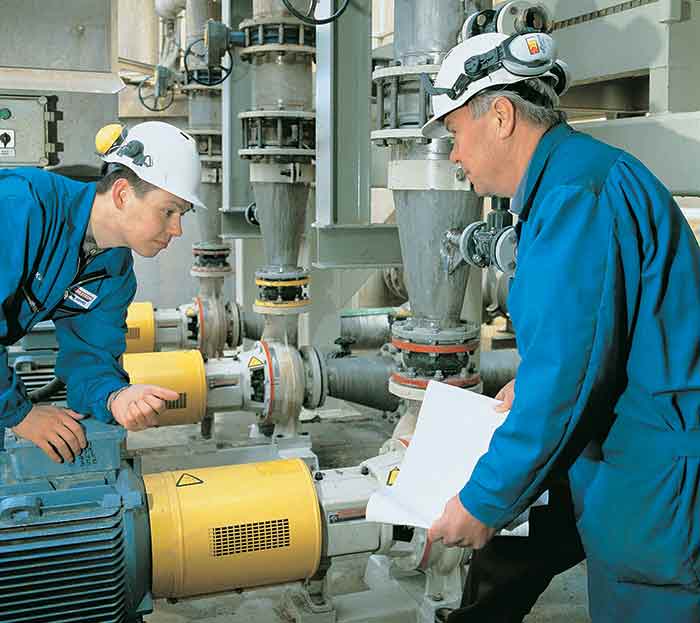
Do not attempt to open a coupling guard while the equipment is in operation. Follow proper lock-out, tag-out practices before maintenance is performed on the equipment.
References
1. MPTA-C7c-2010 “Common Causes of Tire Coupling Failures”