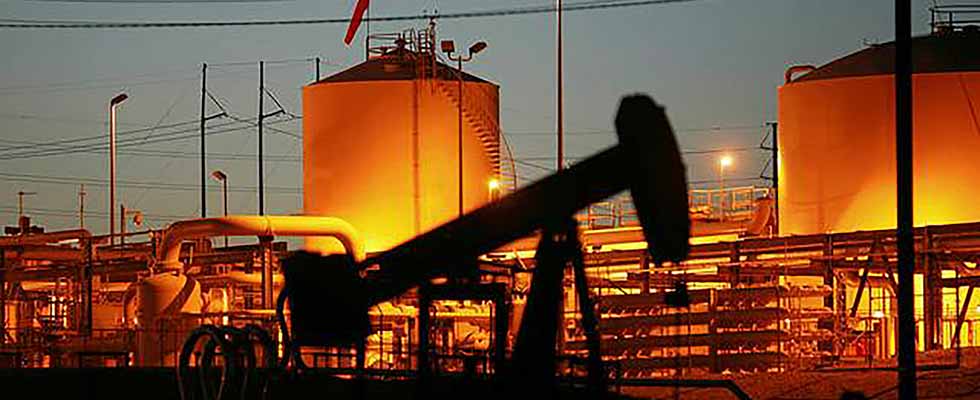
More than 100 countries produce oil and gas around the globe, and metering pumps play a critical role in upstream production. This article takes a look at how metering pumps are used in oil and gas applications. It identifies the criteria that all of the various players in the supply chain evaluate to select the right pump.
When it comes to selecting a metering pump for oil and gas operations, it is not enough to know what a pump can do. All participants in the supply chain (operators; consultants/engineers; integrators; engineering, procurement and construction (EPC) firms; and pump manufacturers) should know each other—the who. It is helpful if they already have working relationships in place and have demonstrated previous success. Everyone in the value chain should know when the specifications for a project will be identified and released, as the timelines for large projects can span several years.
With these variables identified, the players in the supply chain can then evaluate how metering pumps meet the project’s specifications.
Once the short list of pump manufacturers has been determined, the selection criteria often expands beyond the pump’s capabilities to include purchase price, total cost of ownership over the life of the pump, and the manufacturer’s ability to meet the required lead times, which includes provisioning the pumps to the required specifications and testing them to ensure they meet expectations.
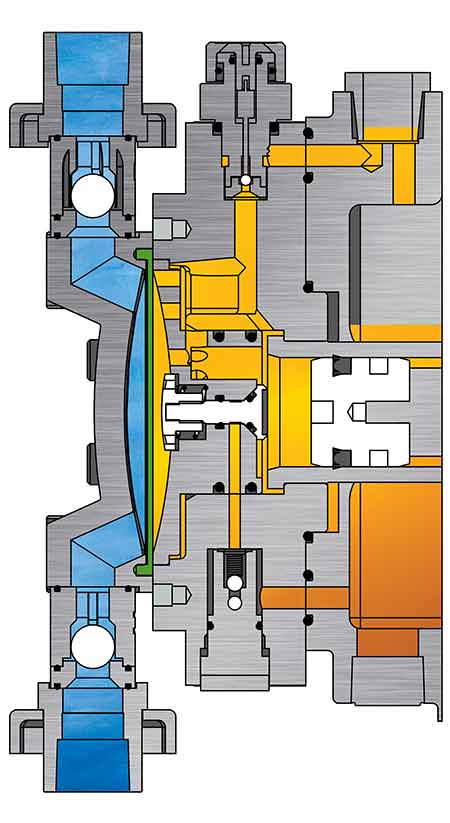
What & How
Metering pumps are positive displacement chemical dosing devices that can deliver accuracy to within one-half of 1.0 percent. Hydraulically actuated diaphragm metering pumps can be a preferred choice for oil and gas operations for two reasons: accuracy and reliability.
The operating principle for this type of pump is simple and has remained relatively unchanged since they were patented in the 1940s. Chemicals enter the pump when the motor drives a piston to create a vacuum that pulls chemicals into the liquid end from external tanks.
Alternating piston strokes create pressure that closes the inlet valve, opens the outlet valve, and forces the chemical out to the process. As the piston moves, it pushes hydraulic fluid into the diaphragm, which flexes the diaphragm at a specific angle and at a specific stroke rate to move a precise volume of chemical through the liquid end and out to the process. Hydraulic fluid in the pump’s liquid end acts as a barrier between the piston and the diaphragm.
Because the piston never contacts the diaphragm, and because the diaphragm is balanced perfectly between the hydraulic and process fluids, there is little wear on the diaphragm. As a result, this type of metering pump can run for decades.
Metering pumps play a critical role in the following oil and gas applications:
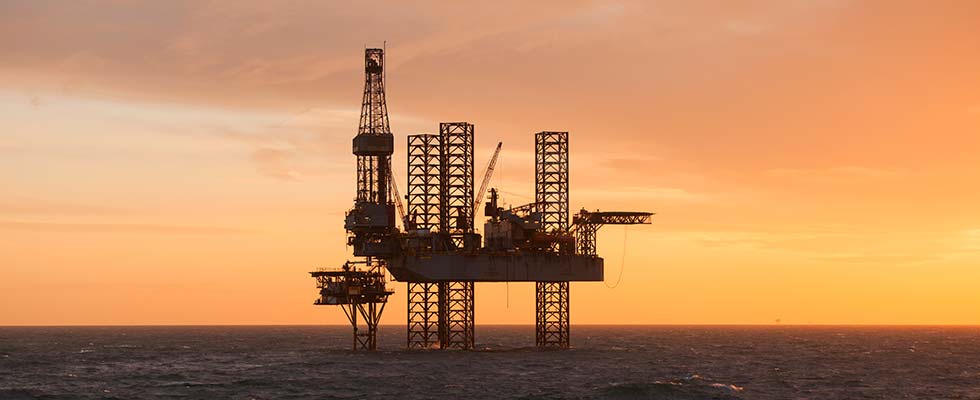
Flow assurance: When working in deep offshore environments, one of the biggest issues is the formation of hydrates, which form when light hydrocarbons and water mix under high pressures and low temperatures. Hydrates restrict flow and can damage equipment. Remediation is expensive and dangerous to people, equipment and the environment, so a sound strategy for managing hydrates is critical. Metering pumps are used in offshore environments to deliver flow-assurance chemicals, such as methanol, monoethylene glycol and other corrosion inhibitors. These chemicals are pumped directly to the wellhead on the seabed (via umbilical cords) to not only prevent hydrates from forming, but also to increase recovery rates and prevent the wellhead from freezing.
Separation and pipeline transport: Once brought up from the wellhead, oil, gas and unwanted items must be separated on the platform or floating, production, storage and offloading (FPSO) unit before oil and gas can be pumped into pipelines. During this separation, liquid hydrocarbons can become unstable, as asphaltenes and paraffinic materials in the oil can reduce “flow-ability” and damage pipelines. To remedy this, a wide range of asphaltine and paraffin inhibitors must be metered in specific doses during this separation phase. Accuracy matters because these chemicals are expensive and injecting too much upstream requires removal downstream.
Enhanced oil recovery (EOR): When a new well is initiated, the top 10 to 20 percent of the hydrocarbons will flow freely because immense natural pressure in the reservoir pushes oil and gas to the surface. The next 30 to 40 percent of a reservoir’s content is typically recovered by injecting large volumes of water (or gas) into the reservoir to displace oil and drive it toward the wellhead. The third and final recovery phase (where up to 50 percent of a reservoir’s content can remain) is known as enhanced oil recovery (EOR). This requires a mix of gas, steam, water and chemical injections to move the remaining contents toward production zones where they can be extracted.
To reach the deepest parts, polymers and active agents are dosed into the reservoir via metering pumps. Chemicals known as surfactants lower surface tension between oil and the rocks trapping the oil. These chemicals improve the “wettability” of porous rocks and allow water and other chemicals to flow through the rock to displace oil. Once dispersed from rock formations, oil droplets can be extracted by metering different combinations of polymers that work like a squeegee on a windshield—pushing oil droplets together into larger bunches that can then be swept toward production zones and extracted.
Because the age, geology, depth, temperature and pressure are different at every reservoir, the chemistry required for EOR is unique to each reservoir, and the mix will change throughout the extraction life cycle. As a result, metering pumps used to deliver the catalysts must be accurate and flexible to interpret data and analytics and adjust flow volumes to render the optimum cocktail needed for the EOR extraction.
Water Treatment Applications:
Upstream: Metering pumps are used throughout the United States Bakken shale region to treat the enormous volumes of water used in fracking operations. Water’s life-giving properties encourage bacterial growth, which fouls pipes and equipment surfaces. Water also dissolves gases (like oxygen and carbon dioxide), which can corrode metals. If left untreated, scale deposits and fouling will diminish efficiency and lead to unplanned downtime. So, the water used in upstream applications should be cleaned to protect equipment, and it must be treated after use, before it can be discharged back into the environment.
Downstream: Refineries are enormous consumers of water. Every 50,000 barrels of refined oil generates 1 trillion British thermal units (Btu) per hour, which is removed by water evaporating in cooling towers. Large refineries can use more than 10,000 gallons per minute (gpm). As cooling towers eliminate heat from evaporating water, dissolved solids like calcium and magnesium remain in the tower. Over time, these solids diminish thermal efficiency and cause corrosion. To prevent this, API 675-compliant metering pumps are used to dose specific volumes of acids, caustics, scale inhibitors and disinfectants. These water treatment applications enable cooling towers to run at higher cycles of concentration, which enables refineries to save money by reusing water and limiting blowdown activities in their cooling towers.
Metering pumps are also used to treat boiler feedwater in refineries and petrochemical plants in a variety of ways, including: disinfection applications (by metering chemicals such as sodium hypochlorite or benzene), pH control (by metering sulfuric acid to lower the pH or caustic soda to raise the pH), and to render polymers and scale inhibitors to protect plant equipment.
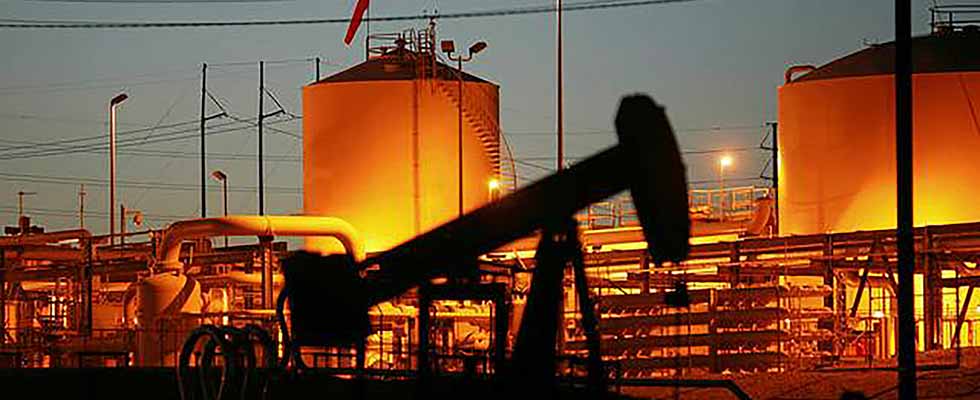
Metering Pump Must-Haves
Although metering pumps are relatively small components on an oil and gas rig, the role they play is enormous, because if they fail for any reason, the entire enterprise can be compromised.
With any oil and gas application, the value of a single day’s production vastly exceeds the cost of the pumping systems. For these reasons, metering pumps must be manufactured to the highest standards, and they must address the following requirements:
Accuracy: They should be measured to within 1 percent accuracy with 1,000-1 turndown capabilities. The flow rate dispersed from diaphragm pumps can be altered remotely by actuators that adjust the stroke length, or the speed of the motor, to provide the precise volume of chemical that is required by the process.
Reliability: The design of the hydraulically actuated diaphragm pump is critical for pumps that are deployed on offshore platforms or in remote onshore locations.
Streamlined maintenance: All pumps require basic maintenance to keep them running at optimal efficiency. All spare parts required (diaphragm, check valves, valve seat and the sealing gaskets) should be available with a single part number, and these parts should be easy to install when required.
Compact, efficient footprint: Each ton of equipment on an offshore platform costs roughly $30,000 per ton. Considering that hundreds of pumps are required on a platform, the weight and footprint of each pump matters. Metering pumps are now available in smaller and lighter packages.
Construction materials: The liquid ends for metering pumps should be available in a variety of metal or plastic materials to accommodate the wide variety of acids, bases, viscous liquids and corrosive chemicals that are required for various applications.
Delivery times: Hydraulically actuated diaphragm pumps are not off-the-shelf items. Once the specs are identified, each pump is custom built to meet the flow, pressure and chemical handling requirements of the application. A quick turnaround (measured in two to three weeks) is important because system integrators have to incorporate dozens of pieces of equipment onto skids. Any shipping delays for one piece of equipment can have ripple effects on the delivery date for the entire skid.
Addressing API standards without exceptions: The standard applied to metering pumps in oil and gas environments is the API 675 specification. This standard provides the framework that pump manufacturers and purchasers agree on for the design, fabrication and testing of a metering pump. Since 2014, a number of exceptions and waivers have been allowed to this specification for items such as flanges, relief valve settings, bolting materials and other ancillary items. A variety of clarifications stipulate how flow and pressure tests should be performed and additional stipulations define how documentation should be provided. This is important not just for system integrators who initially purchase the pumps, but it also brings peace of mind to EPCs and plant operators by letting them know that no corners have been cut concerning the safety and the reliability of their metering pumps.
When it comes to selecting a metering pump for oil and gas operations there is no question—the design and the performance of the pump matter. These characteristics help explain why a system integrator chooses a particular pump.
But, from the perspective of the manufacturer, or the reseller supporting that manufacturer, it is critical to see the bigger picture that also brings the who, what, when, where and how into the equation.
With all of these factors in mind, pump manufacturers—and the distributors, systems integrators and EPCs they work with—can best address a number of new (and large-scale) upstream projects coming online in North America, the Middle East, India, Africa and China in the year ahead and beyond.