Size and revolutions per minute play a key role.
Atlas Copco Power Technique
11/20/2018
When it comes to groundwater and stormwater applications, selecting the right pump is crucial. The most common reason pumps fail is due to a misstep during the pump selection process. Using the wrong pump can mean expensive, critical errors—and a big mess.
Know Your Application
Prior to selecting a pump, the application should be known. What type of water is being moved and where is it being moved? Begin by looking at elevation change, distance and flow. The elevation change determines the pump strength needed to overcome gravity resistance. The suction elevation from the water to the eye of the impeller and the discharge elevation from the eye of the impeller to the water’s destination should be known. By adding these two numbers, the sum total elevation (gravity resistance) will be revealed. The distance determines if the line size should be increased to reduce friction loss due to friction resistance. Friction occurs in all pipes and hoses when liquid travels through. Two things that affect friction are the velocity at which the product is traveling through the pipe or hose and the overall distance of the pipe or hose to the delivery point. The distance from the suction point to the water’s destination needs to be known. Additionally, if pumping into a piping system that requires a certain pressure, the pressure required must be converted into equivalent feet of static head. For the static head measurement in feet, multiply the pressure required by 2.31. Valves and fittings also add resistance to flow.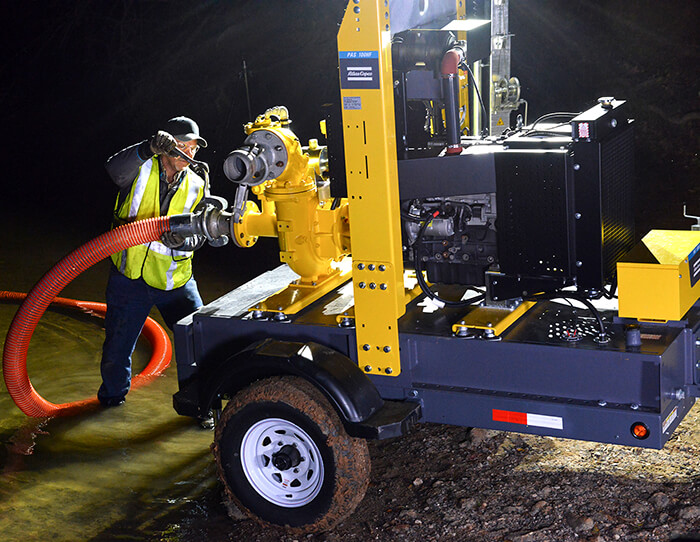
Factors for the Right Pump
It is important to know what type of water is being moved and how quickly it needs to be moved. If it is water from a storm, it could have solids in it, which could include large trash pieces. Groundwater will have rocks, silt, sand and mud. In groundwater and stormwater applications, knowing the pH is imperative if chemicals are in the picture. The following guidelines will assist in selecting the correct pump:- Electric submersible pumps excel in deep groundwater.
- Well-point pumps work well in less than 25-feet-deep groundwater systems and are highly efficient. They are designed for long, straight pipes in the ground as well as when digging a construction site.
- Centrifugal pumps excel in situations where there are solids and trash. A great example is sewer applications.
Additional Considerations
Once you have the application down and know the type of pump to work with, also consider: Size and power:The biggest reason pumps fail is due to incorrect sizing. For example, there might be too much horsepower and not enough flow, which can produce a rattle that could lead to the pump coming apart. Selecting the wrong size can lead to seal, impeller and shaft failures. Hose: Selecting the right hose is as important as selecting the pump. Discharge hose or high-density polyethylene (HDPE) can lower friction losses, but it all depends on the distance. The general rule of thumb is that for anything under 1,000 feet, use the same line size as the pump suction and discharge. For anything over 1,000 feet, use the next largest size hose or pipe as the pump suction and discharge. The exception to this rule is with HDPE pipe. Control box and technology: A full-featured control box is important especially if what is pumped varies in flow. The level transducer, pressure transducer and floats help regulate the flow. The pump can be turned on and off from a cellphone with remote start and stop.
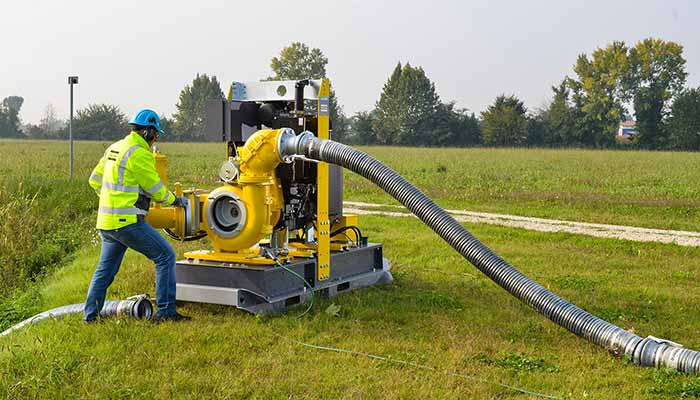
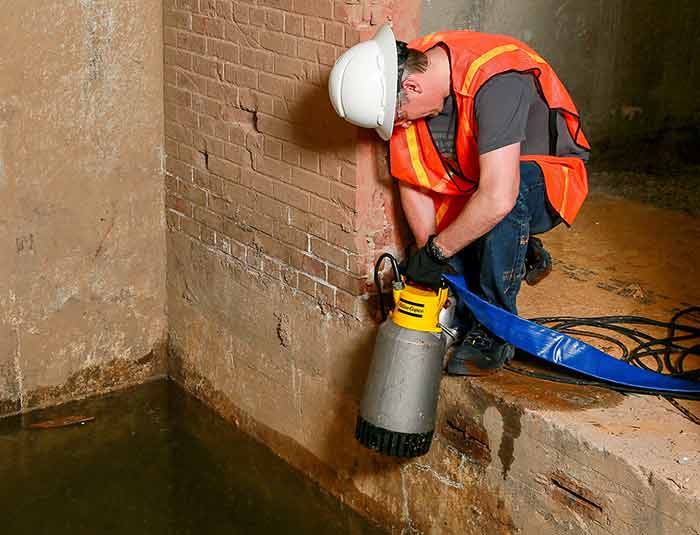
Renting or Buying?
If renting a pump, know the distance, elevation change and the type of water. With this information, any reputable pump solution store will be able to provide the correct pump. If buying a pump, it is generally because a solution is needed often as similar issues keep occurring. A good salesperson will be able to use the distance, elevation change and type of water to suggest the right pump(s) for the application(s). Remember these three things to ensure success:- Pick the correct pump.
- Pick the correct hoses and fittings.
- Run it at the lowest rpm.