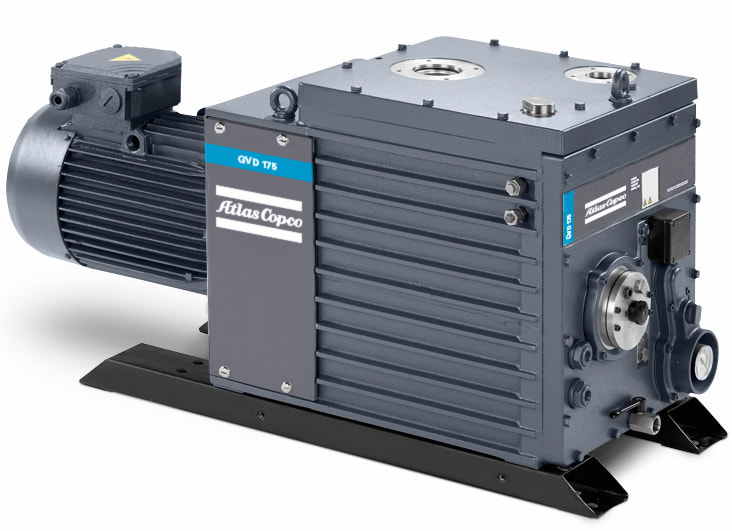
Today’s cannabis production has evolved beyond those of times past, when the traditional flower product was its primary market driver. While the demand for cannabis in traditional leaf form still exists, many modern-day users of tetrahydrocannabinol (THC) and cannabidiol (CBD) opt instead for cannabis extracts/concentrates in the form of topicals, edibles, vaporizer cartridges and the like.
For the consumer, these products provide a much more potent product—THC extracts, for example, can contain a THC percentage of somewhere between 90 and 99 percent, as opposed to the 15 to 20 percent found in the traditional flower product. Creating these higher-potency products requires extracting highly concentrated THC and CBD oils from the cannabis—introducing an extra step known as cannabis distillation to the production process. And for operations looking to produce THC and CBD extracts in high volumes, incorporating a vacuum pump into the distillation process can alleviate headaches, save time and lower the chances of making costly mistakes.
Vacuum Pump Use in THC & CBD Extraction
There are two stages where vacuum is used in the production of THC and CBD oils:
- Removal of ethanol used for extraction
- Purification and distillation
Ethanol is typically used to separate waxes and other products in the cannabis plant from the cannabinoids (other solvent options include butane).
No one would want solvents in their CBD or THC oils, though.
.jpg)
The target is a solvent-free extract. Therefore, the ethanol used in the extraction needs to be removed. Ethanol boils away at around 78 C (172.4 F) at atmospheric pressure. However, if users can pull a vacuum deeper than about 28.5 inches Hg gauge (HgV), the ethanol’s boiling point is reduced to 12.8 C (55 F), which is well below room temperature.
As a general rule, the greater the depth of the vacuum used, the more the boiling point can be reduced. CBD and THC have higher boiling points than the solvents that were needed in the evaporation steps. Because they are terpenes, THC and CBD have high boiling points (312 to 482 F, 156 to 250 C). Distillation under atmospheric conditions is undesirable as it would potentially change the characteristics of the desired product. To prevent the material from burning, a deeper vacuum is required to aid in the transition to the gas phase.
The depth of vacuum needed for any purpose depends on the size of the vacuum system, the types of compounds being distilled and the speed of distillation desired. Consequently, the size of pump required for cannabis distillation is dependent on the size of the vacuum system itself, the cubic feet per minute (CFM) required to maintain the desired flow through the system, the specific type of process the lab is running, and the amount of biomass the lab aims to process in a day, week or month. Generally, for botanical extractions such as cannabis distillation, a medium to high vacuum is ideal.
In summary, vacuum conditions are used to lower the boiling temperature. By applying vacuum, the boiling points are lowered, with the additional bonus that oxygen is removed, thereby eliminating oxidation of the product. These vacuum conditions protect against product degradation by reducing thermal decomposition due to heat exposure and by removing oxygen to create the vacuum.
Another aspect to consider is safety. A top vacuum pump-related concern regarding chemical hazards in the distillation process is the risk of volatile substances contaminating the pump oil and subsequently being released into the work environment. Because common solvent extraction methods employ a hydrocarbon like methane, butane, propane, carbon dioxide or ethanol, risks for ignition can also exist.
Should this lead lab owners to purchase an oil-free vacuum pump? For some applications, yes—but it is far from always necessary. While the optimal choice will depend on the specific application of the pump, most CBD/THC applications employ oil-sealed rotary vane pumps. When oil-lubricated pumps are employed, it is important that they be properly maintained at the manufacturer’s suggested service intervals and to ensure that the oil is changed as needed depending on the environment the pump is being used in.
Looking at the market, rotary vane or liquid ring pumps are typically employed for cannabis distillation. Typically, these high-performance pump types are capable of maintaining the vacuum depth required, and they allow users to flush the vacuum pump to maintain the precise base pressure over time. Further, these are usually among the lower-priced pump options, providing high-value options for operators. Scroll pumps work well for purging vacuum ovens to collect the terpenes produced during distillation.
For larger systems, lab operators may want to consider a pump with variable speed drive (VSD) capabilities, or even look at a centralized vacuum system, which can meet vacuum requirements while creating efficiencies by shutting down when not needed). With a central system, multiple vacuum loads are balanced into a stable demand monitored and served by VSD plus vacuum equipment co-located in a utility room. They also allow duplex application with two pumps on a tank. Generally, though, centralizing a pump is sufficient when the required vacuum level is maintained for the duration of the application.
So, which pump is right for users? Like most mechanical products, the answer is: It really does depend. The references show that one does not really need a vacuum deeper than 0.001 – 0.010 Torr (29.91996” HgV - 29.91961” HgV). These pressures border on the deepest “medium” vacuum range, potentially approaching the beginnings of the “high” vacuum range.
Other Vacuum Pump Uses in the Cannabis Industry
Drying: Vacuum pumps are often used for drying hemp and removing water and other solvents without overheating the material. Heating can allow some constituents to burn or evaporate before the real process begins. Liquid ring pumps and claw pumps are often used for these applications.
Winterization: Further purification often requires fractionate crystallization or winterization. The product from distillation is chilled to allow some constituents to precipitate. Filtration is required to remove those, so vacuum is often used to accelerate the process. Liquid ring pumps and claw pumps are often used, given that deeper vacuum levels are not required.