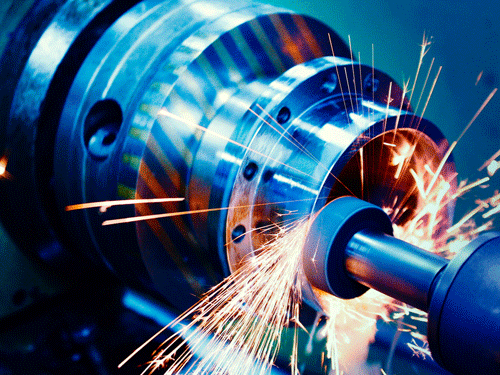
Pumps are used in various industrial applications, including manufacturing and computer numerical control (CNC) machining.
CNC machines play an essential role in the manufacturing of components for everyday products. In contrast to additive manufacturing (3D printing), molding or forming CNC tools, such as drills and cutters, are used to remove or grind away material from workpieces of steel, aluminum, carbides, brass, copper and even plastics to form shapes for a specific purpose. The material is removed with bits, or lathe tools, rotating at high speeds, which create holes, generate voids and/or remove surface layers to close tolerances. These cutting tools are mounted onto a variety of chucks and driven by precision servo motors that control the position and movement of the tools or workpieces under computer supervision.
In addition to drilling and cutting, CNC machines are designed for numerous other purposes, including grinding, milling and routing.
Pumps in CNC Machining
Pumps play a key role in the function and operation of CNC machines.
For example, many CNC machines include an apparatus for applying coolant to the tool and workpiece, in order to facilitate a clean, high-quality cut. The coolant is often a mix of water with lubricant and serves several purposes, such as reducing thermal expansion of the material, reducing wear on the tools, preventing rapid oxidation in some materials and, most importantly, clearing or evacuating the material chips that are produced in the cutting process. The accumulation of chips on the tool surface or inside cut cavities of a workpiece can cause defects in the cut and accelerate the wear and tear on the tools. The coolant is pumped from a reservoir and sprayed onto a tool from one or more nozzles directed at the tool tip. This coolant then flows back into the reservoir, or sump, generally after filtering. The pump used in the coolant system provides accurate coolant flow and pressure, making it essential to the proper operation of CNC machines.
In automated CNC machine operations, pumps also play a key role in the hydraulic system, the architecture used to regulate the handling of multiple tools clamped into the spindle chuck. This hydraulic system is responsible for the control of cutting tools of various weights and sizes, the precision installation and the exchange of the cutting tools in the spindle chuck, which requires a high degree of automation with hydraulic fluids operating under pressure ranging from 522 to 580 pounds per square inch (psi).
Sensor Data & Key Signals in Pump Condition Monitoring
Various measurable operating parameters of CNC machine assets can help provide visibility into the performance of the overall machine operation. Examining this machine operation data in order to determine the need for maintenance fits within the larger practice of condition-based monitoring (CbM). Pressure, coolant flow or velocity and even vibration measurements are all essential types of sensor data necessary for condition monitoring. This data feeds embedded algorithms in order to detect and flag emerging anomalies and trends, giving actionable insights to operators and decision makers within the organization.
For pump condition monitoring, the key measurement signals needed are vibration, pressure, flow rate and temperature. Vibration, specifically, has the greatest importance given its sensitivity to several pump failure modes. Vibration signals are typically extracted and analyzed at a high sampling rate, requiring signal processing techniques to evaluate the pump waveform in the frequency domain. Vibration-based condition indicators are calculated and consist of metrics that consider the overall vibration magnitude and the frequency domain magnitude at the characteristic bearing, shaft and vane pass frequencies. The pressure, flow and temperature signals are usually at a lower sample rate. Other common condition indicators to consider are statistical features or metrics derived from the pump performance curve. Considering pumps have many different failure modes, it is advantageous to combine multiple condition indicators into a health index in order to monitor the pump and compare its measured signals to a reference baseline condition. With this pump health indicator, early detection of emerging problems can be discovered, as well as information revealing which sensor variable contributes most to the unhealthy condition.
Case Study
A global manufacturer was looking to adopt a condition monitoring solution for the CNC grinding machine in its production line to optimize maintenance and increase overall productivity. With the help of a predictive maintenance solution provider, this company was able to leverage the provider’s advanced data processing techniques and algorithms, as well as the developed health index, to detect and predict data trends indicative of healthy machine operations, expanding the use of sensor data beyond operational control within the typical practice of CbM.
The hydraulic system and pump were identified as key subsystems of the CNC grinding machine. A data collection system was set up to monitor the vibration, pressure and flow rate for the pump, along with additional measurements regarding the grinding machine operation. The analysis approach segmented data on a cycle-by-cycle basis and extracted condition indicators from the vibration, flow rate and pressure signals. A baseline time period of approximately one month was used to train the machine learning model to learn what condition was considered healthy for this pump. Vibration, pressure and flow rate condition indicators were then compared to this baseline model. The multivariate health index showed a developing and increasing trend in the health value as the pump’s condition degraded. Vibration was identified as the main contributing factor since it had the most clear and noticeable trend over time. More subtle downward trends and reductions in flow rate and pressure were also observed.
A Predictive Monitoring Solution
With this solution, the company was able to recognize the emerging pump issue and repair the pump before its flow rate and pressure were reduced to a state in which the pump would not be able to perform its function. Therefore, costly unplanned downtime and failure were avoided, and the pump repair took place at a more convenient time outside of production.
The condition monitoring system improved pump health with vibration values reduced to a much lower value, and the pressure and flow rate values returned to their original baseline and higher values.
Outcomes
As the case study illustrated, the main value proposition for adopting a pump condition monitoring solution is the reduction of unplanned downtime. Additional benefits include a decrease in the time to repair the pump, supplementary diagnosis information and energy savings. Achieving the cost savings can only be realized if the condition monitoring system provides an early detection of pump problems as they develop. Fortunately, many common pump failure modes (bearing failure, cavitation, shaft misalignment, unbalanced impeller, seal failure, etc.) are covered by monitoring the vibration, pressure, flow rate and temperature. Although early detection and diagnosis are typically feasible, accurate failure prediction depends on the failure mode and could require past examples of failure for the model to learn the fault progression pattern.
As machines become more complex and operate at a higher performance level, monitoring systems that leverage multiple sensor technologies, signal processing and data analysis techniques will become the standard for modern CNC machines and pump systems.
Getting Started
With this overall trend toward advanced data insights, there are several recommended steps for getting started with pump condition monitoring:
Perform criticality analysis to select assets for condition monitoring in which downtime would be costly and failures not extremely rare.
If available, review the data collection system already in place. As needed, add additional sensors and instrumentation, keeping in mind that the key signals for pump monitoring are vibration, flow rate, pressure and temperature, with vibration being the most important.
After a proper data collection system is in place, the right foundation must be set to begin developing and implementing the pump condition monitoring system.
Be sure to select a predictive solution that is end-to-end and scalable, designed specifically for use within the industrial sector, and usable by both your knowledgeable personnel working to develop the solution, as well as the key stakeholders that will make use of the provided information to ensure the right actions are taken before costly issues can occur.
When getting started with data analysis, focus on a baseline-based machine learning analysis approach as failure data is often not sufficiently available, and the baseline-based approach has many successful examples of early detection, providing value for various applications.