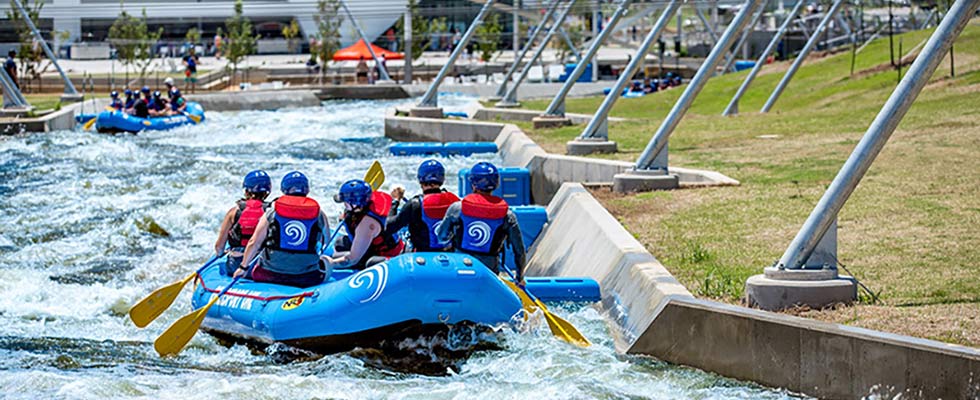
Oklahoma City’s Boathouse district brings a unique spin to entertainment and attraction in the region. Offering a multitude of outdoor adventures and located conveniently in the OKC metro, the Boathouse district brings adventure for residents and tourists with rowing, high-speed slides, paddleboarding, kayaking, canoeing, zip-lining and more.
The Riversport Rapids is the most recent add-on to the Boathouse district. This is one of only three man-made whitewater attractions in the United States. This facility includes a large lift station structure that houses six medium-voltage (4,160 volts), 700-horsepower (hp) mass flow submersible pumps. Each pump weighs 22,000 pounds (lbs) and is capable of moving 82,000 gallons of chlorinated pool water per minute. They pump through two channels and create class II-IV rapids.
On a normal day, three to four pumps can be running together in order to provide whitewater rapids for tourism customers. During Olympic trial events, all six pumps are used to create true whitewater rapid conditions. This course has half a million gallons per minute moving when all six pumps are on. Each of these pumps is controlled by a soft starter.
During the initial construction phase, installation and startup, several challenges were identified with these pumps. Multiple vibration problems were immediately noticed and Oklahoma City began looking for help to identify the issues. Together, with the pump manufacturer and user, an aftermarket service and repair company assisted in finding solutions and completing all startup requirements for the lift station structure.
The manufacturer and municipal customer also needed a long-term total service provider capable of not only assisting during the startup phase of the project but also helping to maintain six large submersible pumps for years to follow. The provider was able to give field support, in-shop repairs, adjustments and long-term solutions.
Since inception, several minor vibration problems were identified along with adjustments in length needed to wire rope and lift the apparatus. Some of the work included replacing thrust bearings, guide bearings, mechanical seals, lip seals, seal sleeves and O-rings.
The service provider was also able to assist in the replacement and repair of the impeller and locking nut and provide a new power cable. Throughout the repair process, all parts were steamed and cleaned, including stator housing. Then they were baked out, dried and clean electrical baker tests were performed and documented.
The rotor was put on the balancing machine where it was balanced to a G1 specification. Final assembly, electric testing and paint were completed prior to the return of the pump. Other challenges were long lead times on parts coming from overseas providers.
Solution
In collaboration with Oklahoma City and theme park management, the repair service provider decided to order a spare parts kit, including a spare impeller. This equipment is pre-positioned and stored in the aftermarket repair shop.
In the event that one of the mass flow pumps goes down and/or starts having any vibration issues, the service provider can then minimize downtime for the user. The provider also works with the city and theme park to rotate two pumps through the repair shop during off-peak season for preventative maintenance. This allows more time for pulling pumps, transporting pumps to the shop, making required repairs and reinstalling pumps.