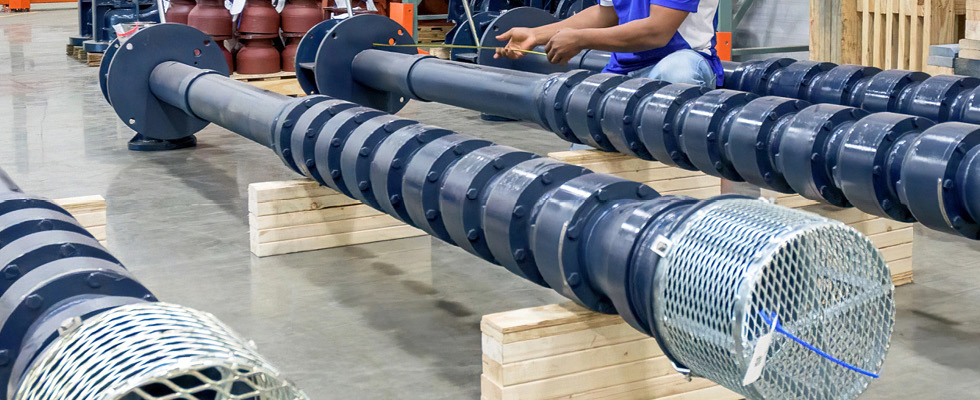
Engineers who design residential and municipal pumping systems are often faced with the critical task of specifying and maintaining a water delivery system that meets high performance demands and distributes water that is consistently safe for human consumption. That is what makes the standards for drinking water applications so important. These strict standards are used throughout the United States and Canada to help engineers identify products that are certified safe for drinking water system components.
However, identifying certified components is only one part of the specifying challenge. Engineers must also understand how those components are vetted and how they will deliver the hydraulics and functionality needed for the application. Meeting the challenges of performance while ensuring public safety can be complicated, even for industry professionals. What steps can engineers take to ensure they are specifying a system that addresses the application requirements? Consider these insights regarding drinking water standards—what they mean, how they have changed and how they can be used to design a system that meets a home or community’s performance demands.
Designing for Tomorrow
Continuous improvement is critical in the water industry, and drinking water standards are no different. In fact, these standards are constantly in review. For example, a specific drinking water standard first adopted in the late 1980s has been republished over 40 times. Innovative new materials, new threats to water quality and new variables are all important to engineers and are all considered when new standards are developed. That allows the standards to address any new science related to water quality while making sure engineers can design systems that are safe to use today and well into the future.
The team that evaluates and writes the drinking water standards is extensive and includes representatives from three core sectors: manufacturing, general interest (such as the Environmental Protection Agency [EPA] and state regulators) and the certifying bodies themselves.
Manufacturers are involved in these discussions for an important reason: They can provide insight into feasibility and performance. While public safety is paramount, standards must be achievable from a production standpoint. Are the materials realistic and cost effective? Can a pump be produced to meet a standard, and what will it take? When new standards are established, it can take several months to literal years for a manufacturer to build these compliant products. By having a voice at this table, manufacturers help ensure that quality products are constantly in the development pipeline.
Meeting Drinking Water Standards
Every part of a pumping system that comes in contact with water and is intended for consumption will need to be evaluated against drinking water standards. This means all components and materials in the system should be known and understood. Additionally, the manufacturing process and factory conditions at a supplier’s and the final manufacturer’s facility are critical. There should be no introduction of an unwanted negative agent that could be in violation of the standard. Variables like these can ultimately affect product certification.
Here are a few critical questions engineers should ask themselves to ensure all components are fully vetted and safe for potable water:
- Is the entire product or pumping system certified? When pumps are evaluated for compliance, all wetted areas must include compliant materials. From submersible to above-ground systems, this means any type of pump and its components (the entire unit) must meet strict standards to gain certification. Engineers should work with manufacturers and certifying bodies to determine the compliance of their products. They can also visit the certifying body’s public listing and browse via product and manufacturer plant.
- Is the complete manufacturing facility certified? When products, packaging or literature are marked as certified, this covers the manufacturing facility and the product. This certification is important since manufacturers participate in ongoing evaluations to remain compliant. Plants and suppliers are regularly inspected and validated for adherence to processes and requirements, ensuring the fabricated products and their critical components can be certified to meet drinking water standards.
Online selection tools can help engineers build a system that meets the latest standards. These tools can swap out noncompliant materials for compliant ones, making product selection easier. They can also instantly provide the documentation needed to verify compliance.
Ensuring Performance & Public Safety
With drinking water systems, health and safety always come first; however, engineers must also make sure they are installing a system that delivers water reliably and at peak performance. The overall hydraulic design—including the flow rate and pressure, pump efficiency and head curve—are still important. Other variables may also come into play. For example:
- Does the system need to operate quietly?
- Is backflow prevention important?
- Does the pump seamlessly integrate with other system components like piping, valves and storage tanks?
Drinking water systems are expected to last for many years and operate reliably throughout their life span. Designers must choose durable materials and incorporate features that facilitate easy maintenance and repairs.
This is also where online selection tools provide incredible benefits. Advanced selection tools allow users to filter or narrow down their selection based on the parameters that are most important to them. In addition to certification needs, users can specify suction/discharge size, power requirements, net positive suction head required (NPSHr), desired speed of operation, number of stages, bowl diameter, power rating and other relevant factors. These tools will do all the calculations related to performance curves, eliminating manual tasks and time-consuming data searches. This can include the recommended system components, a complete price quote and important accompanying documents (e.g., performance curves, dimensional drawings and detailed specifications of components).
Cost
Of course, one of the biggest questions of all is how to ensure performance needs and public health/safety within the parameters of the project’s budget. This is also why manufacturers are a key voice in writing, changing and improving drinking water standards. Drinking water compliant products need to be functional, reliable and efficient while still being cost effective.
This often involves optimizing designs for low energy consumption, minimal maintenance and long life spans. Feasibility includes ensuring water delivery does not suffer, engineers have the solutions they need and water users are satisfied with the results. Finding the right balance between these factors can be challenging, but manufacturers also know it is critically important no matter the changes new standards may bring.