Last of Two Parts
11/30/2015
Part 1 of this series (which can be read here) discussed the lack of a formal, comprehensive global standard on pump efficiency and the importance of understanding the difference between actual field efficiencies of installed pumps and the initial original equipment manufacturer (OEM) efficiencies. As noted in part 1, studies show that the efficiencies of installed pumps are commonly reduced by 10, 20 and often close to 50 percent below the OEM-quoted (rated) point.4a/b Several factors can contribute to this trend: wear over time (clearances), changed flow conditions, degraded internals (impellers, casing) and other issues. When measuring actual efficiencies, end users should keep the following factors in mind.
Measurements Errors
Efficiency is the ratio of productive power (to move flow against pressure) to total power applied to the unit by the electric grid (see Equation 1).
Flow Meters
Flow meters are either not installed (at least not per each pump) or not calibrated for a long period of time. External flow meters (ultrasonic or similar) require straight piping runs before and after the meter, as well as knowledge of the piping wall thickness, fluid characteristics and many other parameters. Most people would expect a measuring instrument to have a value of at least +/- 0.5 percent. As studies show, however, reported flow data from the field is often 10 to 30 percent off the mark.5Differential Pressure
Differential pressure (p) is usually a simpler and easier parameter to measure, certainly with better accuracy and less expense as compared with flow.Electric Power
Electric power presents a controversy right from the definition: What power? Is it power delivered to a pump (as OEMs report in catalogues or quoted curves) or to the motor (which is what is actually accessible)? Is it measured at the motor box or miles away at the switchgear junction? Are kilowatts measured directly or calculated from measured amps and volts? Are power factor, motor efficiency and line losses taken into account?Measuring Efficiency
A pump rarely operates at a single point and almost never at the best efficiency point (BEP). If an end user were to conduct the same test both today and tomorrow, flow would likely be different. As a result, no meaningful comparison of these two efficiency values can be made.Trending & Online Live
Trending, as noted above, suffers from lack of flow constancy from one measurement to the next. Doing a live test (by opening and closing valves to construct the entire curve) is a much better way to have an apples-to-apples comparison. This method determines BEP, and all tests are consistently compared to this BEP. This is certainly a step in the right direction, but it requires significant involvement of plant personnel—including operators and mechanics—which is why such tests can be logistically difficult to arrange. A continual automated test is a much better approach and is gaining popularity.7 This method involves installed measuring equipment and probes that allow the system to acquire data continually. Hardware captures the data, and software converts this data to the actual performance and compares it with the OEM data.Pump User Approach
Many end users are not too interested in the philosophy of global concepts of energy assessment or in how much money can be saved if power plants become more efficient. These users need detailed information about their specific piece of equipment—how reliable and efficient it is. If their equipment is not reliable, they want to know why and what can be done to make it more reliable and last longer. If it is not efficient, they want to know how much money the system (pump/motor) wastes and how it can be improved. End users typically look for a specific number, not a general concept. The current draft (Revision 2) of the International Pumps Efficiency Standard does just that. While addressing the concepts just discussed, the standard goes directly to efficiency evaluation. It incorporates a computer program that estimates the typical industrially achievable efficiency based on flow, head, speed, specific gravity and a number of stages (for multistage pumps) and also displays power and the expected typical size of the impeller to help the pump user evaluate the immediate and obvious issues in the application.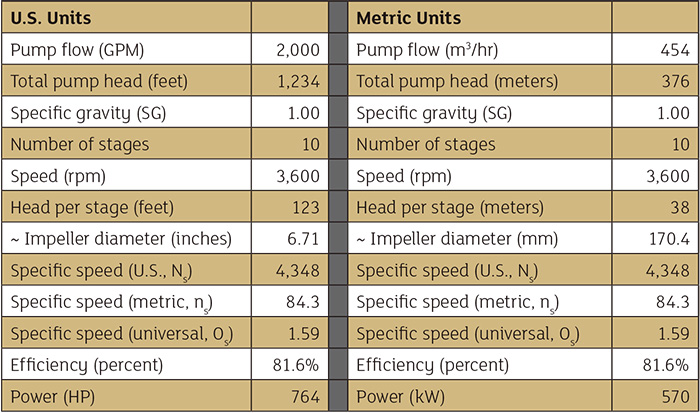