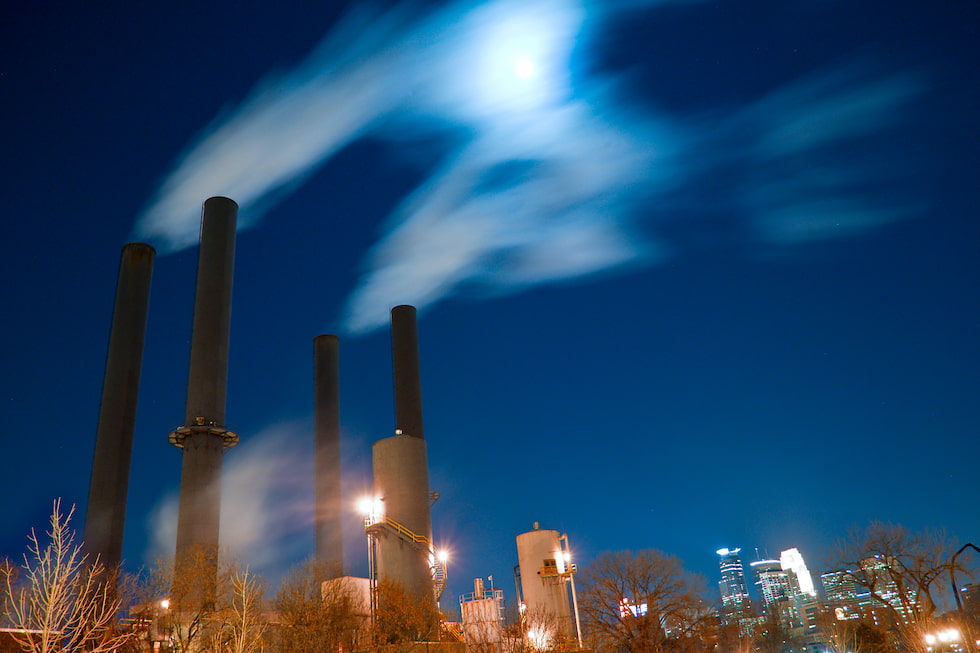
Two-thirds of fuel used in manufacturing escapes as waste heat and, for many companies, this waste heat has become a way to reduce expenses and become more energy efficient. Many firms have taken to using waste heat to power (WHP) systems to recapture as much of that lost energy as possible. They have turned to a few reliable and some newer technologies to cogenerate power while their business performs its primary purpose, while others use waste heat to generate power. Combined heat and power (CHP) systems are one way to reclaim fuel and heat lost in the industrial process. The options for combined heat to power are microturbines, steam turbines, gas turbines, fuel cells and reciprocating engines. For WHP CHP systems, the various cycle systems are Kalina, organic Rankine (ORC), and steam Rankine (SRC). However, some of the more proven technologies are steam turbines or heat recovery steam generators among cogenerative CHP systems and the SRC or SRC system among WHP systems. There are other systems available to add WHP, mostly in the research and development phase. Steam turbines and SRC systems are of some of the most widely used and well-honed technology for heat to power systems. They are known for their adaptability and reliability. Each system is different, and each has its benefits and detriments.